Inventory control for vehicle spare parts enable efficient management and tracking of spare parts inventory. Some common techniques include consignment inventory, supplier managed inventory, reorder point and two bin system. These techniques help to improve the overall efficiency and effectiveness of the vehicle spare parts inventory management system. They ensure that the right parts are available when they are needed, reduce excess inventory, minimize inventory costs, prevent stockouts and ultimately increase customer satisfaction. Companies can also streamline their inventory management processes, increase their profit margins and gain a competitive advantage in the marketplace by adopting these techniques.
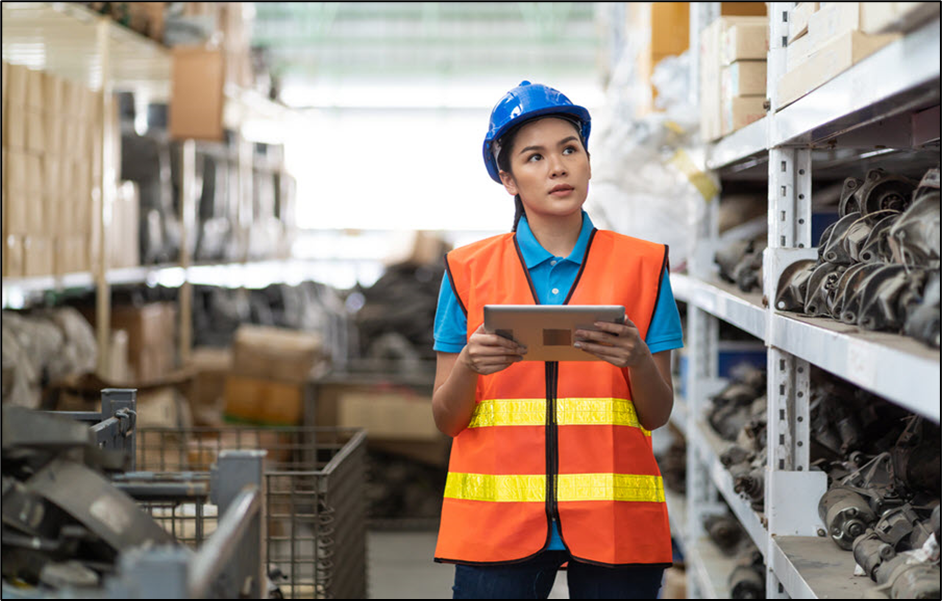
Image taken from SIPMM: https://publication.sipmm.edu.sg/essential-techniques-manage-machine-parts-inventory
Table of Contents
Consignment Inventory
Consignment inventory involves stocking products owned by a supplier at the customer location until they are used or sold. Suppliers ensure that their goods are easily accessible to customers, and customers save money upfront by buying only what is needed. Consignment inventory guarantees the availability of automotive spare parts without the upfront costs associated with buying and keeping significant amounts. The implementation of consignment inventory for vehicle spare parts necessitates selecting reliable suppliers. It also involves drawing up formal agreements and negotiating terms with suppliers to resolve any concerns immediately. Consignment inventory generally simplifies inventory management, lowers expenses and raises customer satisfaction in the vehicle spare parts sector. The potential limitation of the customer control over item availability and selection is a disadvantage of vehicle spare part consignment inventory.
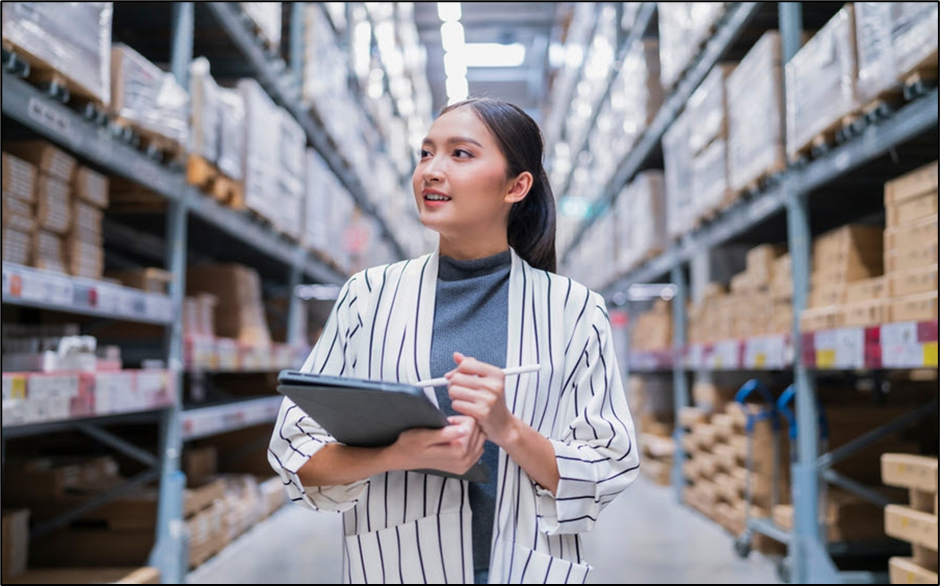
Image taken from SIPMM: https://publication.sipmm.edu.sg/practical-techniques-control-warehouse-inventory/
Supplier Managed Inventory
Supplier Managed Inventory (SMI) is a system in which the supplier takes responsibility for maintaining optimal inventory levels at the customer location. This strategy benefits both parties, where suppliers get insight into customer demand patterns, while customers profit from lower inventory carrying costs and increased product availability. SMI ensures that important vehicle spare parts are constantly in stock, eliminating the need for customers to manually control inventory levels. SMI implementation for automotive replacement parts requires creating a relationship with a reputable supplier that can reliably forecast demand and have enough stock levels. It is crucial to have comprehensive agreements that specify roles, inventory goals and communication procedures. The dependence on the supplier demand forecasting skills is a drawback of supplier managed inventory for vehicle spare parts. Inaccurate demand estimates from the supplier may lead to overstocking or stockouts. This may lead to delays in auto repairs and increased inventory costs.
Reorder Point
The reorder point is a critical component of inventory management since it indicates when to restock inventory to avoid stockouts. Computation of reorder point is based on lead time, demand variability and service level. Reorder point guarantees that sufficient spare parts are available to meet demand and ensures operations run smoothly. Additionally, reorder point is determined based on factors such as utilization rate, lead time and service level. When inventory reaches this level, it indicates the need to reorder, reducing stockouts and delays in vehicle maintenance. Overall, regulating the reorder point is critical for striking a balance between meeting demand and reducing excess inventory costs in automotive spare parts management.
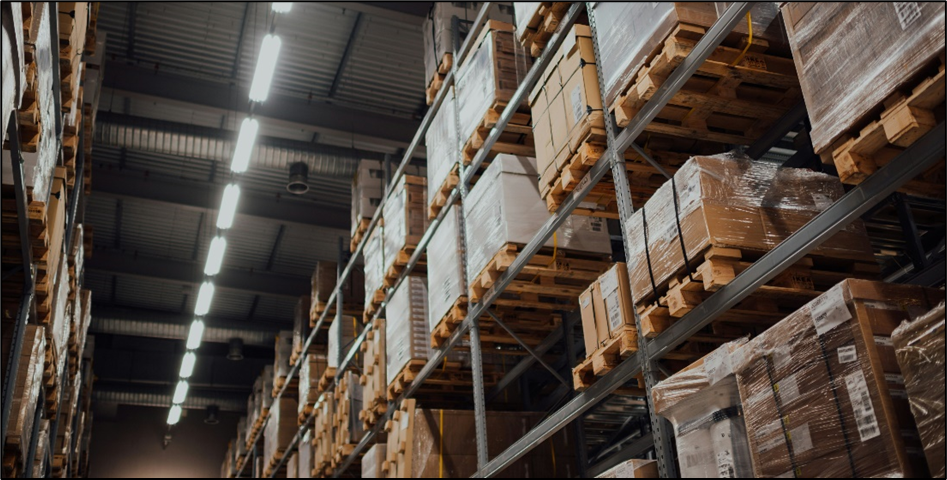
Image taken from https://unsplash.com/photos/brown-cardboard-boxes-on-white-metal-rack-BNBA1h-NgdY
Two-Bin System
The two-bin system is an inventory management strategy that uses two bins to hold inventory items. The empty first bin serves as a cue to reorganize the item while the second bin is being used. This technique is useful for maintaining the ongoing availability of important items while reducing the likelihood of stockouts. The two-bin method reduces downtime for repairs or maintenance by ensuring that necessary parts are always available in the context of vehicle spare parts. This technique for vehicle spare parts requires identifying important spare components and determining inventory levels for each bin based on demand and lead times. Aside from that, marking bins clearly and developing a reordering mechanism when the first bin is empty are both vital. The disadvantage of this system is how it may not be suitable for vehicle spare parts with unpredictable demand fluctuations.
Safety Stock Inventory
Safety stock is a buffer for extra inventory that a company holds to protect against fluctuations in demand, or unexpected delays in replenishment. It serves as a buffer to ensure that sufficient spare parts are available to meet customer demand, even during peak periods or in unforeseen circumstances. The process of building safety stock involves analyzing demand trends and lead times. It also entails assessing the importance of individual parts for vehicle performance in the context of vehicle spare parts. Based on these considerations, a safety stock is established and maintained. This is to ensure that sufficient spare parts are available to meet customer demand and reduce the impact of supply chain uncertainties on vehicle maintenance. Regular monitoring and adjustment of safety stock is necessary to adapt to changing demand patterns, and ensure optimal inventory management.
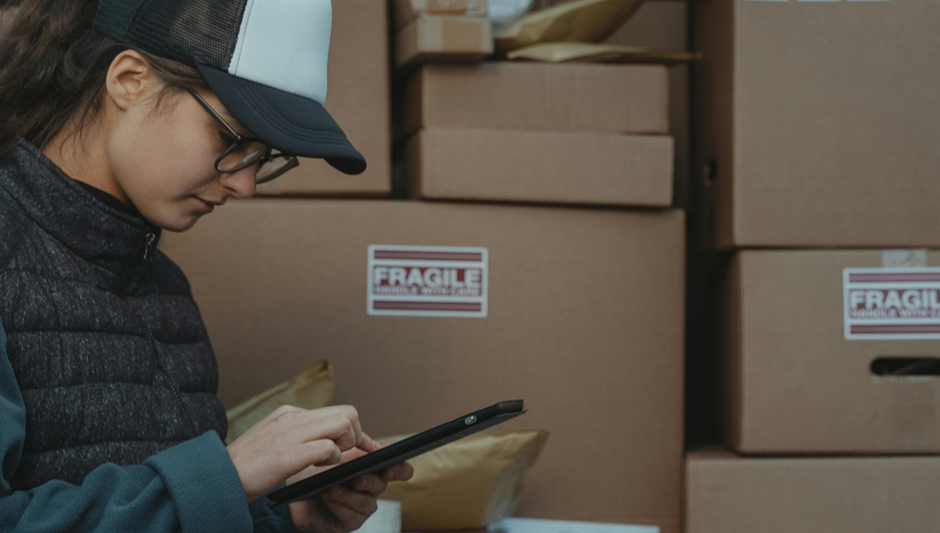
Cycle Counting Technique
Cycle counting is a technique in which a small, predetermined number of inventory items are counted regularly instead of performing a complete inventory check. This method is used to ensure inventory accuracy and to identify discrepancies or errors in inventory records. Companies can regularly check their inventory, detect errors early and keep accurate records without the need for a full audit, by cycle counting. Certain items are selected for regular counting, with a focus on valuable or frequently used parts when applying cycle counting to vehicle spare parts. Inventory management software can help streamline the counting process by creating lists of items to be counted, tracking counting progress and identifying discrepancies. Regular cycle counts combined with thorough investigation and resolution of discrepancies help to ensure the accuracy and integrity of the vehicle spare parts inventory.
First-In-First-Out (FIFO)
First-in-first-out (FIFO) is a method where the oldest inventory items are sold or used first, ensuring that goods are used in the order they are received. This method is useful because it prevents product spoiling, minimizes the risk of obsolescence and ensures that inventory remains fresh. Since older components are issued first, the possibility that vehicle spare parts become obsolete or damaged due to lengthy storage can be lowered. The FIFO principle is applied to vehicle spare parts by placing the oldest parts at the front and the newer parts at the back. Additionally, regular inventory level monitoring and stock rotation are required to assure compliance with FIFO principles and inventory integrity. Overall, FIFO helps optimize inventory management and ensures that parts are used efficiently in the vehicle spare parts industry.
Just-In-Time Inventory
Just-In-Time (JIT) inventory aims to cut inventory costs by only getting goods when they are needed for production, waste reduction and efficiency boost. The goal of JIT is to streamline operations, minimize inventory storage costs and improve cash flow by synchronizing production with customer demand. JIT ensures that the relevant components are available exactly when they are needed. This in turn reduces the need for extensive warehousing and inventory costs. JIT for vehicle spare parts requires close collaboration with suppliers. This ensures the timely delivery of components according to demand forecasts and production schedules. It also requires efficient inventory management systems to track inventory levels and anticipate demand fluctuations. Overall, JIT helps optimize inventory levels, reduce storage costs and improve responsiveness to customer needs in the vehicle spare parts industry.
Conclusion
Companies that neglect to use appropriate inventory control techniques for managing vehicle spare parts can face severe repercussions. Without proper management, there is a risk of overstocking certain spare parts and understocking others, leading to higher costs and possible delays in repairs. Poor inventory control can lead to inefficiencies in ordering and storage, wasting time and resources and making it difficult to locate and track stock. Excess inventory that is not properly managed can lead to higher inventory costs that impact the company profit and cash flow. Without proper stock management, there may also be delays in repairs due to unavailability of spare parts, leading to dissatisfaction and potential loss of business. Therefore, implementing effective inventory control techniques is essential to mitigate these negative consequences and ensure a smooth flow in the management of vehicle spare parts.
References
Foo Chuan Yang.(2022). Practical Techniques to Control Warehouse Inventory. SIPMM Publications. Available at SIPMM: https://publication.sipmm.edu.sg/practical-techniques-control-warehouse-inventory/. (Accessed: 01 March 2024)
Oboloo.(2024). What Is Supplier Managed Inventory? – Definition.
Available at https://oboloo.com/blog/what-is-supplier-managed-inventory-definition. (Accessed: 01 March 2024)
Schoelmann, E. (2023). Tracking Consignment Inventory: A Comprehensive Guide to Best Practices. Available at https://www.rfgen.com/blog/comprehensive-guide-to-tracking-consignment-best-practices/. (Accessed: 01 March 2024)
Sortly.(2024). Best Practices for Spare Parts Inventory Management.
Available at https://www.sortly.com/blog/parts-inventory-management-best-practices/. (Accessed: 01 March 2024)
Suzie Chee Lee Fong.(2021). Useful Techniques to Manage and Control Inventory. SIPMM Publications. Available at SIPMM: https://publication.sipmm.edu.sg/useful-techniques-manage-control-inventory/. (Accessed: 01 March 2024)
Terese Ong Yee Chiat. (2018). Five Important Techniques for Effective Inventory Control. SIPMM Publications. Available at SIPMM: https://publication.sipmm.edu.sg/five-important-techniques-for-effective-inventory-control/. (Accessed: 01 March 2024)
Veron Wong Sook Wei.(2018). Effective Techniques for Inventory Stock Control. SIPMM Publications. Available at SIPMM: https://publication.sipmm.edu.sg/effective-techniques-inventory-stock-control/. (Accessed: 01 March 2024)