The success of a warehouse has a direct impact on its efficiency, productivity, and daily operations. A well-organized layout design can provide easy access to store goods, minimize travel time, improve order fulfilment rates, boost productivity, and reduce expenses. In order to optimise warehouse operations, proper warehouse layout design, handling equipment, and the right technology should be selected to streamline the operations. Training should be provided to all workers to ensure awareness of the operation processes, as many accidents are a result of human error, and the only way to reduce incidents is to always train employees on the safest methods to complete the operation process. This article discusses the factors that are crucial to optimise warehouse operations.
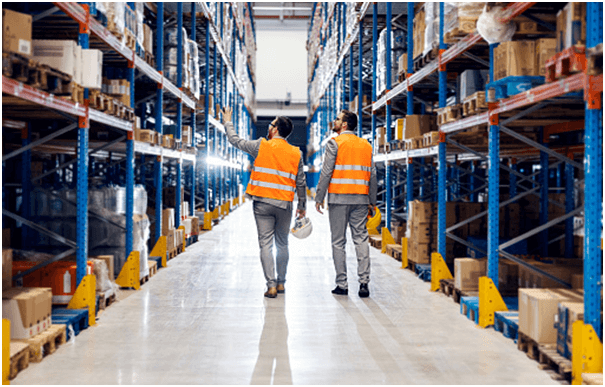
Table of Contents
Warehouse Layout Design
An efficient warehouse layout design improves the flow of traffic in the warehouse, reduces stock losses, and boosts overall efficiency. The layout of a warehouse is an essential factor for effective warehouse management. Conversely, poor warehouse layout has a negative impact on the entire operation. This will lead to increase travel time for shifting, picking, loading, unloading, and retrieval of goods and slow down warehouse operations. A good layout and design can reduce the chances of things being misplaced or mishandled in the warehouse. It is vital to consider all the requirements, such as storage requirements, material handling equipment, and areas for loading, unloading, picking, packing, and dispatching according to the organization’s needs. A fully optimised warehouse layout will not only improve the usage of space but also boost warehouse productivity and save money.
Implementing the Right Technology
Today’s role of technology is the driver of success for every business to improve service level, cost-effectiveness, and speed up the operation process. Technology provides an actionable solution, organizes more efficiently, generates movement reports, and increases visibility. Technology is transforming warehouses, supporting leaner, more agile operations, and enabling warehouses to offer rapid delivery and error-free orders. WMS, for example, may optimise the receiving, inventory records, put-away, picking, inventory replenishment, and shipping processes in a warehouse. Warehouse automation can reduce human error, the need for people to spend time completing paper forms, and generate efficiencies to reduce labour intensiveness. It is time to upgrade the warehouse with technology to replace the manual system and prevent human errors, theft, and inventory loss.
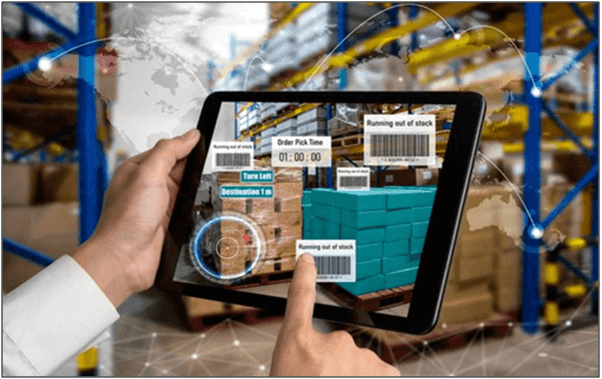
Staff Development and Training
Training and development are vital to sustainable business growth and success, ensuring that warehouse workers’ knowledge is relevant, up-to-date, and compliant with the latest regulations. Employee development is a process to create a development plan that identifies areas to determine what actions or activities are needed in the organization. An ongoing training and development program drives workplace productivity by training employees to be more all-rounded and better skilled at every aspect of their jobs. Employee training involves programs that enable employees to learn precise skills or gain knowledge to improve job performance, especially in safety, software, and MHE training. Investment in training and development provides employees with a greater understanding of the organization’s processes, procedures, and goals.
Adequate Health and Safety Procedures
With such a range of onsite activities, the risk for at-work injuries and fatalities is higher in warehouses than in other occupations. Workplace accidents not only hurt the people involved but also affect their families and co-workers. Warehouse safety at work protects health and lives, helping to maintain economically sustainable warehouses. Employees need to ensure that they follow the correct SOP, follow safety guidelines, and maintain a safe workplace that will reduce the risk of work-related illnesses and injuries. The risks in the warehouse include manual handling, slips and trips, falling objects, vehicles in and around the warehouse, working at heights, and hazardous substances. The organization needs adequate health and safety procedures, such as identifying the hazards, evaluating the risks, implementing the findings, communicating with all workers, reviewing assessments regularly, and updating them, to protect against those risks.
Warehouse Space Utilization
Warehouse space utilization shows how much of the storage area in a warehouse is used and costly for companies, hence, companies are always finding ways to improve their warehouse space efficiency. Warehouse space is at a premium these days, and the storage cost of an underutilized warehouse adds up quickly. If the warehouse has multiple locations for storing the same items, consider consolidating them to improve warehouse space utilization. Extending racks up and using all the vertical space available are usually ways to create more warehouse storage space. For example, single deep racking, double deep racking, narrow aisle racking, mobile racking, shuttle racking, and auto storage systems maximize the space utilization and efficiency of the warehouse.
The full content is only visible to SIPMM members
Already a member? Please Login to continue reading.