The Internet of Things (IoT) is the foundational technology of digital transformation, serving as the method by which items, equipment, installations, and other physical commodities are specifically massively converted into digital means. Another critical feature of IoT technology is its ability to integrate with somewhat Artificial Intelligence (AI) easily, Augmented reality (AR), Blockchain or other in-house systems breakthroughs. IoT devices provide efficient methods to track shipments, verify goods, and use other supply chain technologies. They can also cover product storage conditions, improving quality operations across the supply chain. This article discusses how the various technologies enable the business of logistics to be more innovative.
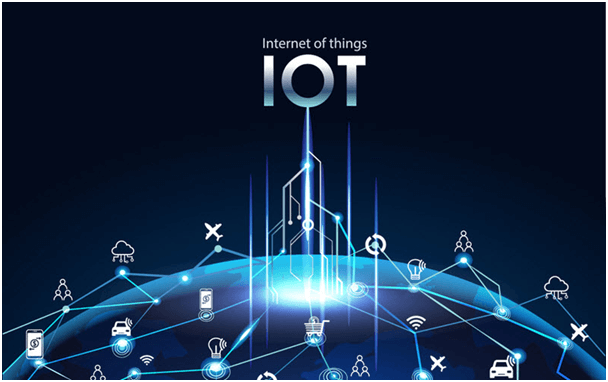
Table of Contents
Internet-of-Things (IoT) Technology
The IoT refers to a physical gadget that connects to the Internet and exchanges and gathers data across wireless networks without the involvement of a human. Wireless networks and low-cost computer chips may now link thousands of goods. IoT devices may detect, monitor, and communicate information about their surroundings. The solution provides logistics personnel with real-time visibility into the status of movements and shipments. This technology assists organizations in increasing efficiency, lowering expenses and reducing personnel needs. IoT applications include asset tracking, capturing commodities movement, and digitizing process documentation. The value of IoT in integrated logistics lies in its ability to forecast, control, and enhance both logistical operations. Businesses may use IoT to examine asset status, process processes, and even real-time reporting with a simple click from their mobile phone or tablet.
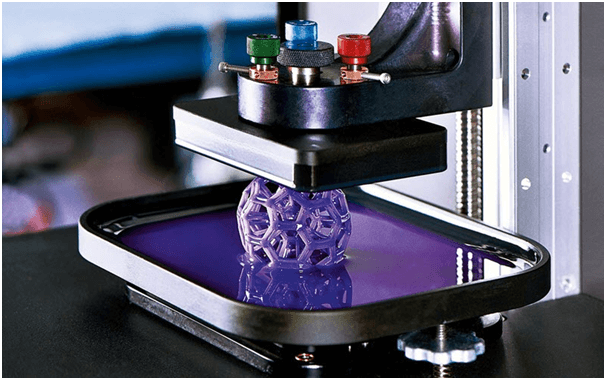
3D Printing Technology
3D printing is an additive method that creates 3D things by layering material. Precision components and products can be designed and printed by manufacturers, enterprises, or workers utilizing resins, polymers, composites, metals, and even human flesh. Companies that use contract manufacturers for 3D printing may decrease risk, gain better control over the whole product lifecycle, and gain more agility by procuring large volumes of components from a single source. Local facilities may 3D print designs on-demand from files delivered from around the world or from nearby vendors safely. 3D printing technology enables businesses to create one-of-a-kind components to match their specific requirements. Compared to previous approaches, 3D printing technology allows companies to remove the suppliers of in-house resources.
Radio Frequency Identification and Barcode Technology
Radio Frequency Identification (RFID) and barcode technologies use radio waves to gather digital data information from barcode or QR labels or RFID tags. RFID is being used by many businesses to replace traditional warehouse functions such as labelling, storing, and placement allocation. By attaching RFID tags and barcodes to products when goods are received, the following user can quickly retrieve the product information from RFID tags and barcodes. RFID and barcode technology significantly improve warehouses through the speed of goods receipt, identification of product information, and more efficient product storage. RFID and barcode technology ensure inventory management efficiency and accuracy. It also speeds up picking processes and improves warehouse inbound, outbound, and storage processes.
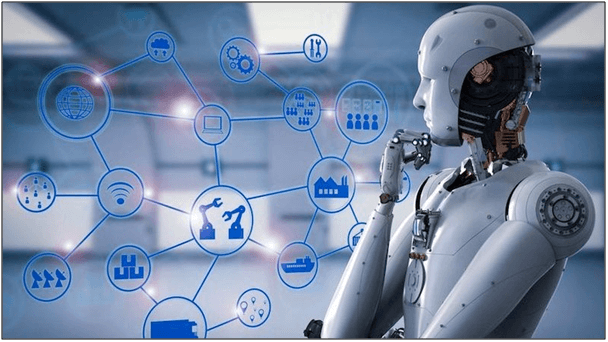
Artificial Intelligence and Machine Learning Technology
Artificial Intelligence (AI) and Machine Learning (ML) enable robots to perform some tedious tasks previously performed by humans, such as storing merchandise, inventory tracking, order picking, inventory counting, and product sorting. Production with AI technology helps companies increase productivity, ensure worker safety, and enable 24/7 production. Using AI technology can eliminate motion waste and significantly improve product quality. AI is a concept that revolves around the use of computer algorithms and methods that enable machines to perform functions beyond human capabilities. Until now, this has been a laborious task that humans have done. Personnel can then be delegated to focus on more important tasks, such as predictive planning based on analyzing data received from machines. In addition, machine learning algorithms can be used to estimate the fuel consumption of vessels. These algorithms can transform data from land-based sources and relate it to the fuel a ship needs. In the long term, AI can help supply chain companies reduce operating costs, reduce accident risk and energy waste, and improve air quality monitoring.
Warehouse Management Systems
Warehouse Management Systems (WMS) is essential software that manages all logistics’ everyday tasks. With WMS, it is possible to oversee facility operations as well as regulate and assist warehouse operations. WMS further enables tracking shipments, cycle counting and aids users in optimizing their inventory management systems. WMS advantages include quicker processing times, more warehouse output, better inventory accuracy, better space usage, and lower labour expenses. We should thank WMS’s integration with RFID technology, as WMS integration with RFID technology ensures that inventory management and asset tracking are possible. The reader reads digitally encrypted data from RFID tags, exchanges data, uploads the recorded data to WMS, and then sends and receives data from the tags.
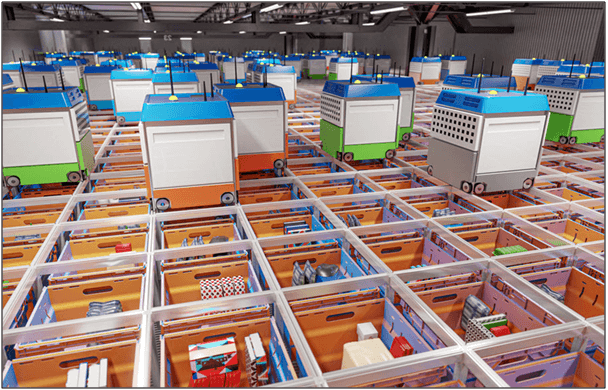
Automated Picking Systems
Manual picking is a time-consuming and labour-intensive activity, and as companies like e-commerce grow, the ability to handle greater product flow and complexity becomes increasingly crucial. Automation in pickings, such as pick-by-voice, pick-to-light, or goods-to-human technologies, has increased efficiency, reduced picking errors, and improved customer experience. All of these technologies are straightforward to integrate with existing and future material handling equipment, including conveyor belts and person-to-person picking. The use of visual and auditory signals can help prevent mistakes and help make more precise decisions. Because of the ease of interface with warehouse software, the module for orderly picking requires less training time. An automated picking system is a low-cost option with a rapid return on investment. Integration with other automation or support processes can achieve scalability and adaptability.
The full content is only visible to SIPMM members
Already a member? Please Login to continue reading.