Warehouse safety is very important and it protects health and lives. Good safety practices are always maintaining economical and sustainable warehouses to keep everyone safe. If warehouse safety treated as a priority, accidents and fatalities can be brought down significantly.
A company that does not have a safe warehouse, is in danger of losing good-quality workers, losing customer base and facing legal action or fines. The companies have to look at practical ways to prioritize and improve warehouse safety practices. This article describes the importance of warehouse safety and the prevention of danger.
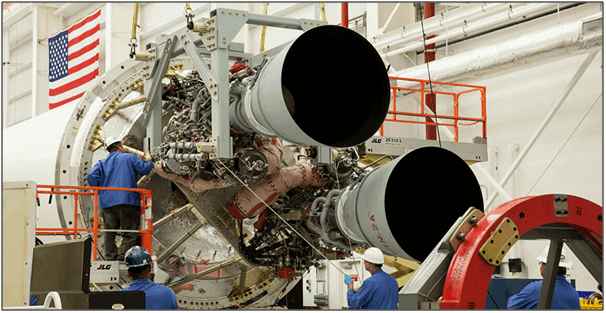
Table of Contents
Warehouse Safety Plan and Procedures
The warehouse safety plan does not end with implementation. It is also the principle that the execution of the safety procedures and maintaining safety procedures. The safety measures must protect from warehouse hazards and ensure that it can carry out work activities safely.
The following are areas to maintain warehouse safety and good practices:
- Always make eye contact with pedestrians while operating Forklift.
- Use proper lifting techniques and mechanical assist when possible.
- Carry out good housekeeping to prevent slips, trips and falls.
- Provide proper protective gear to prevent injuries and infection.
- Use of proper or stable ladder to prevent serious injury and death.
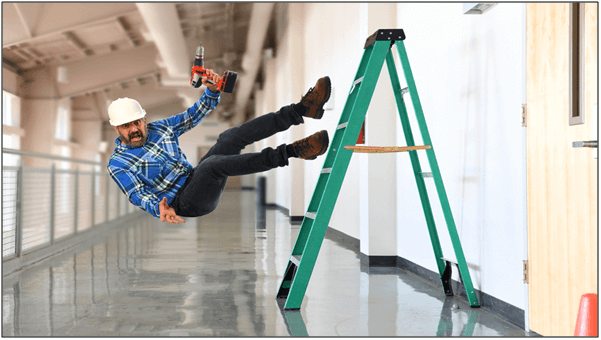
Safe Manual Lifting Techniques
To carry out safe manual lifting activities, need to implement suitable control measures to prevent “Work-Related Musculoskeletal Disorders” (WMSD). The WMSD relate to injuries or disorders of the muscles, nerves, tendons, joints, cartilage and spinal discs. The maximum manual safe working load (SWL) is between 20 to 25kg.
Staff should train in safe manual handling weight limits and proper handling techniques to minimize strain and to prevent major back injuries. Do not lift by bending forward, do not lift a heavy object above shoulder level and avoid turning or twisting the body while lifting or holding. Proper techniques are to bend hips and knees to squat down to the load, keep it close to the body and straighten the legs to lift. Alternatively can use other equipment’s rather than use manual handling example: Forklift, Reach Truck, Pallet Truck, Trolleys etc.
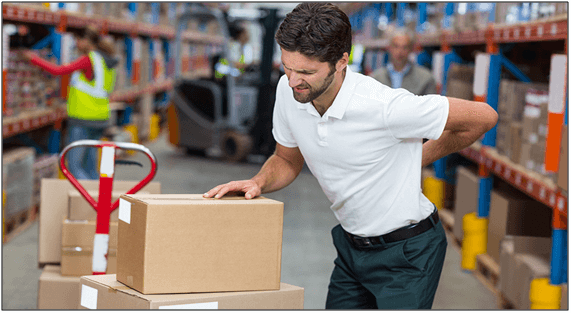
Hazards at the Workplace
Hazards cause the most potential harm in the warehouse. By identifying hazards at the workplace, be prepared to control or eliminate them. It will help to prevent accidents, injuries, death, property damage and downtime. Safety hazards signs are important to understand the common warehouse danger and providing useful information such as safety warnings. The signs are falling into several categories example notice, general safety, fire safety, hazard or non-hazard etc. There are three levels of classification: danger signs, warning signs and caution signs.
The various types of workplace hazards as follows:
- Safety hazards – unsafe working conditions that can cause injury, illness and death.
- Biological hazards – biological substance that can cause harm to humans or death.
- Physical hazards – affect weather conditions or harmful working environments.
- Ergonomic hazards – body positions and working conditions put a strain on the body.
- Chemical hazards – can cause illness, skin irritation or breathing problems.
- Work organization hazards – cause stress such as workload, lack of control etc.
Company Emergency Response Team (CERT)
In the critical situation of emergency or fire, a company should know how to react or respond immediately. The business needs first responders to restore the immediate health, safety and security of employees, in order to keeps the business operating smoothly during emergencies. The company must have a CERT team to acts until the SCDF or Ambulance arrives to take over. The CERT team should carry out fire drills at least twice a year, to familiarize the escape routes work in practice when there is an emergency. They should demonstrate to the staff that the location of fire exit routes and the assembly point of safe evacuation and emergency plan.
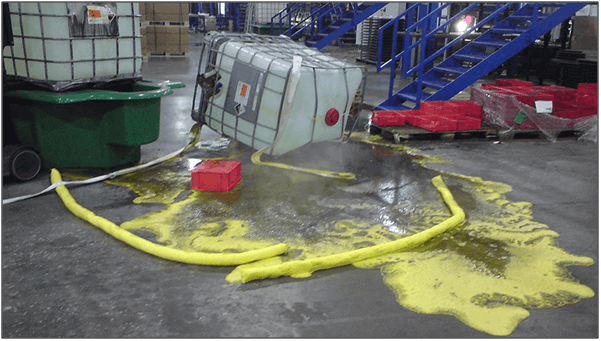
Maintaining Chemical Product
Check regularly all the chemical storage areas for leaking containers and old chemicals. Some chemicals become more hazardous as they age. Degraded should be disposed of to save storage space and remove unnecessary hazards.
The full content is only visible to SIPMM members
Already a member? Please Login to continue reading.