Inventory control is essential for the tobacco industry, just as it is for any business dealing with physical goods. This process involves carefully managing and monitoring inventory. The goal is to ensure that the right products are available when needed and avoid situations where products are out of stock. A well-executed inventory control system can bring several benefits. It can enhance overall efficiency by streamlining inventory management processes. It can help lower costs by preventing overstocking and reducing the need for storage space. Maintaining optimal inventory levels can improve customer satisfaction, as products are readily available. The ever-evolving business requires advanced techniques and strategies to adapt to shifting customer preferences, market trends and supply chain challenges. Effective inventory control maintains product authenticity and quality, which is especially important in industries like tobacco to ensure public health and safety.
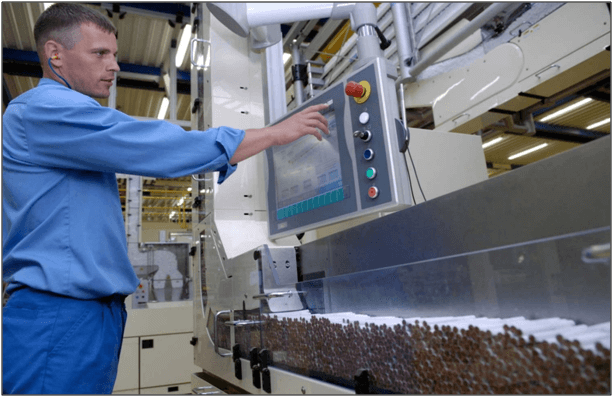
Table of Contents
Regulatory Compliance and Traceability
Maintaining effective inventory control in the tobacco industry relies significantly on regulatory compliance and traceability. Due to health concerns and the risk of illegal trade, this sector faces stringent regulations. Manufacturers and distributors must ensure that products can be traced from production to sale, ensuring transparency and accountability. Accurate traceability systems enable product movement monitoring, discouraging illicit activities and enhancing consumer safety. Adhering to industry-specific laws related to packaging and taxation is crucial to avoid legal issues and promote ethical practices. Modern technologies like barcode systems and RFID simplify the process, offering real-time insights into inventory. Embracing such solutions ensures compliance with regulations, improving efficiency, reducing errors and building consumer trust. By combining regulatory compliance and traceability, the tobacco industry can balance growth and responsibility, securing its position in a highly regulated business environment.
Products Shelf Life and Quality Control
Efficient inventory control, shelf-life management and quality assurance play pivotal roles in the tobacco industry. Methods like FIFO (First-In-First-Out) and FEFO (First-Expired-First-Out) are utilized to achieve these objectives. Adhering to these principles is essential to prevent the buildup of older products and ensure the delivery of fresh items to consumers. This practice not only upholds product quality but also reduces waste by preventing expired items from reaching store shelves. Rigorous quality control protocols further elevate consumer safety and contentment. Consistently monitoring, identifying and removing substandard products is vital to maintaining the industry’s reputation and complying with regulations. This comprehensive approach guarantees product quality and increases customer satisfaction and safety benchmarks. These inventory management strategies efficiently optimize resources, cut operating expenses and promote responsibility. In a dynamic market environment, these measures remain essential to maintain the tobacco industry’s competitiveness and preserve its credibility.
Fluctuating Demand and Seasonality
Stay ahead of the curve and master managing fluctuating demand and seasonality. Effective inventory management strategies must be agile and adaptable to various external factors influencing consumer preferences, legislative shifts and public health campaigns. The challenges posed by fluctuating demand and seasonality in the tobacco industry and leveraging artificial intelligence (AI) and predictive analytics can optimize inventory management. Tobacco product demand is far from stable. Market dynamics, legislative changes, consumer perceptions and other factors can all cause abrupt fluctuations in demand for certain tobacco products. Furthermore, seasonality demands are essential, with customer preferences frequently shifting throughout various periods of the year or events. Inventory management solutions could respond to these swings without causing stockouts and overstocking inventory.
Collaborative Supply Chain Management
In the complex world of the tobacco industry, on-time manufacturing, efficient distribution and product quality are critical. Collaborative supply chain management is the cornerstone of effective inventory management. Collaboration between manufacturers, suppliers and retailers is essential to ensure smooth operations and proper inventory levels. In the tobacco industry, supply chain success depends on collaboration, technology and communication. By promoting teamwork, using advanced technology solutions to share real-time data and maintaining clear communication. The industry can ensure operational streamlining, regulatory compliance and timely response to market changes. These synergies increase efficiency and increase adaptability and growth, making these elements essential to effective supply chain management.
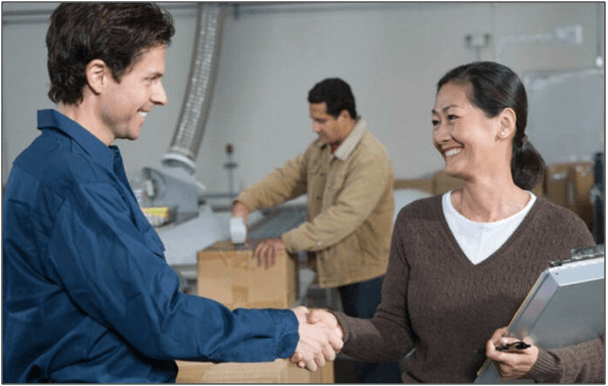
Digital Transformation and Automation
With the result of the digital revolution, the tobacco manufacturing business is undergoing a substantial transition. Automation of inventory management operations is one of the most significant changes. This transition evolution is how items are shipped, recorded and controlled within warehouses and distribution facilities. Automation is changing the landscape of tobacco inventory management. The benefits it can provide the business are real-time visibility with warehouse management software (WMS). For the tobacco business, the digital revolution has ushered in a new era of efficiency and accuracy in inventory management. Automation has emerged as a critical component of this shift. Automated systems are expediting several areas of the supply chain, from the movement of goods to the distribution of goods.
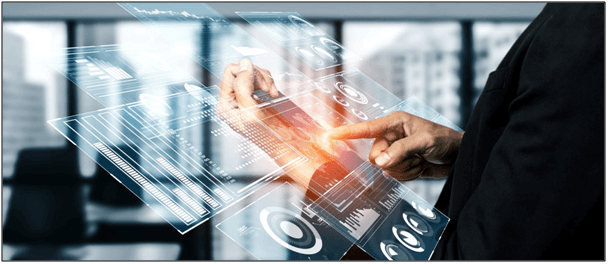
Embracing Technology and Data Analytics
Technology has changed the game in inventory control in recent years. Data analytics, artificial intelligence and automation are changing how businesses manage inventory. Predictive Analytics can forecast future demand patterns with better precision. As a result, there is less chance of stockouts or overstocking thanks to the ability of firms to modify their inventory levels proactively. Inventory Management Software provides better solutions for tracking, order processing, demand forecasting and more. These platforms combine information from multiple sources. These platforms combine data from numerous sources to provide a comprehensive perspective of inventory-related processes. Robotics and Automated systems can perform operations such as order picking, packing and restocking, decreasing human error and increasing efficiency. Warehouses can be navigated by robots, ensuring precise inventory counts and placements.
The full content is only visible to SIPMM members
Already a member? Please Login to continue reading.