In the logistics sector, KPIs are significant for estimating production, costs, and quality rates. It includes certain measurements that are common in the logistics sector. It can help distinguish and sort out issues during its ordinary activity. These estimations can be viewed as elements for the improvement of the activity in the calculated.
Logistics involve the coordination of various functions, including procurement, warehousing, order management, and transportation, to ensure that goods flow efficiently from point-to-point to meet customer demand and focus on measuring the practicality, proficiency, quality, and precision of customer satisfaction.
By observing negative outcomes in the measurements, logistics can discover the perspectives that need improvement and can recognize the regions where the business is strong. Executing these measurements logistics area can draw up arrangements or plan to upgrade its exhibition and to make the administration progressively compelling in doing the targets of the association.
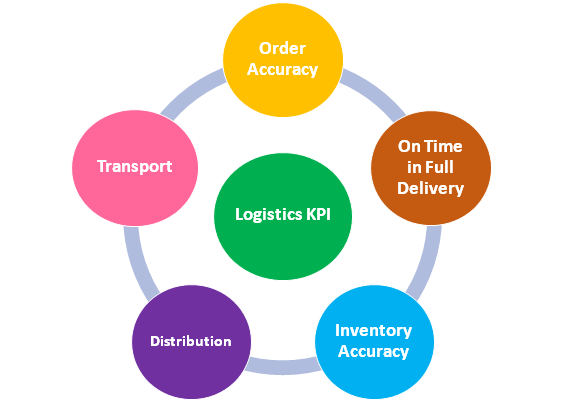
Table of Contents
Order Accuracy KPI:
The Perfect Order Rate is another exceptionally significant logistic metric with regards to your inventory network effectiveness. It gauges the measure of requests that are handled, transported and delivered without any incidents on its way. The transportation time just as the delivered time is both regarded, the request is certainly not an off-base one and the products are not harmed.It is significant as it shows the effectiveness of your production network and delivery, and that leads obviously to progressively fulfilled customers that are eager to return or prescribe your administrations.
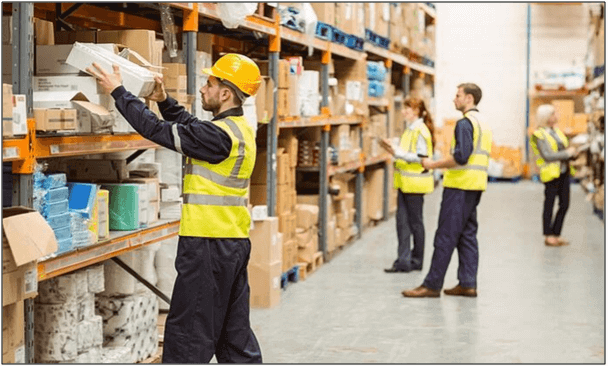
On-Time in Full Delivery KPI
On-Time in Full Delivery (OTIF) is a significant proportion of the logistics effectiveness metric that causes you to monitor how precise your delivery time. It is most important that packages should arrive on time if it as late deliveries negatively affect customer loyalty and can cause you to lose business.
Better performance of OTIF can lead to a streamlined supply chain and greater customer satisfaction. There’s a greater expense to not showing signs of Improvement OTIF execution be that as it may, and in case you’re not moving in the direction of it, you’re likely losing far an unexpected result. Missing the OTIF imprint can be unplanned and unnecessary expenses.
Inventory Accuracy KPI
Inventory is a major significant part of warehousing, and inventory accuracy is a critical KPI for warehouses because if your stock is incorrect, your costs will increase rapidly, and your consumer loyalty levels will plunge. If you are depending on Excel or manual processes, your stock exactness will below, and there’s a good possibility you’ll end up reordering or reproducing parts you already have due to the inaccuracy of stock. The expenses of transport cost an excessive amount of stock, or of rankling customers when you don’t have stock available that you showed is available, will hurt your main concern as well as your reputation. One solution for an inaccurate stock is picking a framework that utilizes standardized identifications to follow stock. Some warehouses find that barcoding, RFID systems integrate with their current Inventory management systems (IMS). These frameworks improve stock control by giving a system to overseeing stock, supplies, and other distribution center materials. Moreover, some IMS can have the ability for following shipments, overseeing buy requests, and checking stock and stock levels.
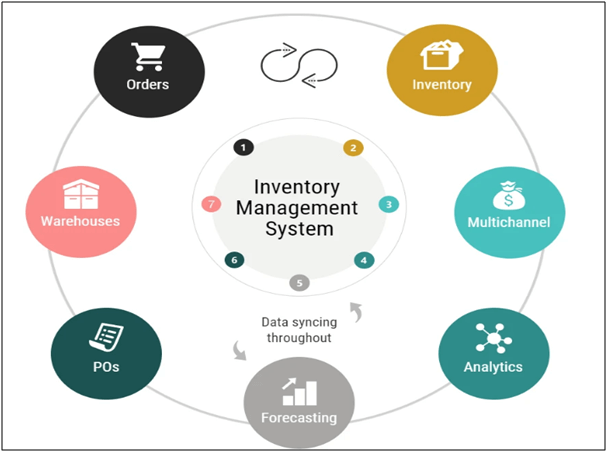
Distribution KPI
Distribution center administration influences expenses and efficiency; subsequently, we should focus on these estimation parameters such as Units prepared per square foot. We figure out this proportion isolating the units we handled at a given period by the distribution center’s usable space.By knowing the volume of items moved in each working hour, you will have the option to know your representatives’ productivity. Percentage of utilized space. In addition to other things, it has to do with an absence of room where to put your crude materials or completed items; it is critical to think about the accessible space before putting in new requests.
The full content is only visible to SIPMM members
Already a member? Please Login to continue reading.