In today’s rapidly evolving technological landscape, the warehousing of television (TV) products is crucial in the global consumer electronics industry. As society connects more and entertainment preferences diversify, the demand for advanced TVs with great visuals, features, and connectivity has surged. This article explores the key success factors for effectively managing TV product warehousing. It is important to recognise that the key to a successful TV supply chain is efficient warehousing. In order to meet demand and ensure smooth operations, companies must focus on several crucial factors. They include the storage layout, climate control, inventory, security, skilled labour, and software system. By addressing these factors, companies can achieve optimized operations, better customer satisfaction, and develop a competitive market edge.
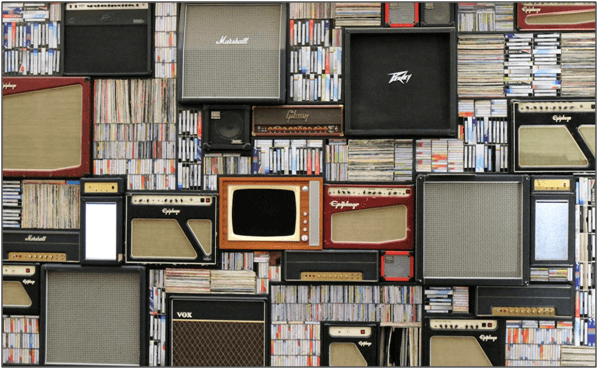
Table of Contents
Effective Warehouse Storage Layout
A comprehensive approach is essential to designan effective warehouse storage layout for television products. The design includes requirements that optimizes space utilization, enhances operational efficiency, and ensures the careful handling of delicate electronics. The layout must prioritize the principles of accessibility, organization, and safety to facilitate the seamless flow of goods from receiving to shipping. To begin with, the layout should incorporate designated areas for receiving, inspecting, and sorting incoming television products. This helps in minimizing the risk of damage during the initial stages of handling. Once received, the televisions should be organized in racking systems that consider their dimensions and weight. The use of adjustable shelving or pallet racking allows for flexibility to accommodate varying sizes of TV units. Moreover, a well-designed warehouse employs a “first-in, first-out” (FIFO) or “last-in, first-out” (LIFO) approach, ensuring that older stock is rotated and dispatched before newer arrivals.
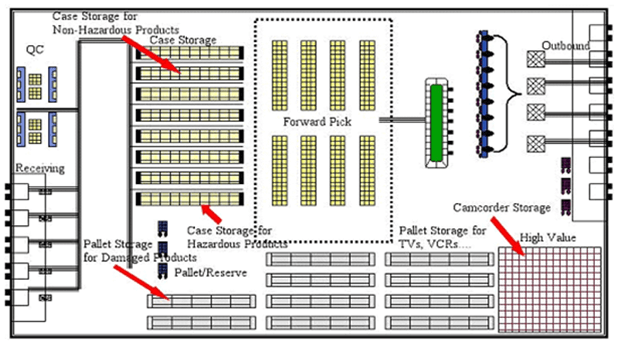
Efficient storage also involves leveraging automation and technology. Implementing an inventory management system that integrates barcode or RFID technology assists in accurately tracking each unit’s location and status. This streamlines the process of locating and retrieving specific television products, reducing search time and minimizing errors. The layout should also incorporate clear pathways and aisles wide enough to accommodate forklifts or other handling equipment. This will promote easy navigation and reducing the risk of accidents.It could be required to use specialized equipment, such as anti-static shelving or climate-controlled areas, to protect the integrity of delicate components. To prevent damage during transportation within the warehouse, cushions, padding, or dividers can be utilized within storage units to separate individual items and prevent any impact-related mishaps.
Climate Control in Warehouse
Maintaining optimal climate conditions in a warehouse dedicated to television products is of utmost importance to ensure the preservation and proper functioning of these sensitive electronic devices. It is crucial to uphold a consistent and controlled environment within the facility to prevent fluctuations in temperature and humidity. They could potentially result in the deterioration and malfunction of the products. By implementing advanced HVAC systems, temperature monitors, and humidity regulators, the warehouse can secure a specific temperature range. This precise management of the climate not only safeguards the quality of the television products’ internal components but also extends their lifespan.Moreover, it reduces the likelihood of defects caused by environmental factors. By investing in state-of-the-art climate control technologies, the warehouse can ensure that customers receive television products in impeccable condition. This will lead to an improved viewing experience and heightened customer satisfaction.
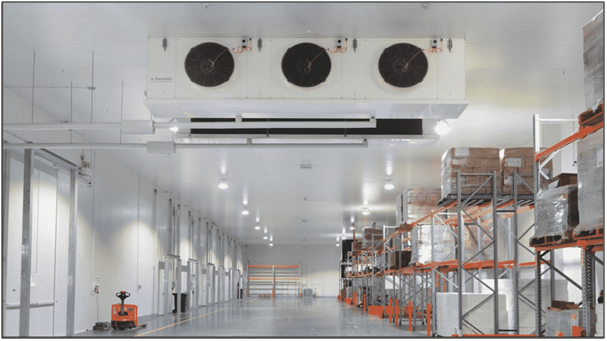
Successful Inventory Management
Successful inventory management for television products is a critical component of any retail or distribution operation. It requires a delicate balance between anticipating consumer demand and optimizing supply chain efficiency. A robust inventory management strategy involves accurate forecasting techniques that take into account factors like seasonal trends, market trends, and consumer preferences. By closely monitoring these variables, businesses can ensure they maintain optimal stock levels, preventing both overstocking and stockouts. Implementing a reliable inventory tracking system, such as barcoding or RFID technology, aids in real-time visibility of stock levels and simplifies the reordering process. Additionally, a well-organized warehouse layout and efficient order fulfillment processes contribute to minimizing holding costs and order processing times. Regular analysis of inventory turnover rates and identification of slow-moving or obsolete items allow for timely decision-making on clearance sales or product discontinuation. Successful inventory management not only guarantees customer satisfaction through product availability but also enhances profitability by reducing carrying costs.
Warehouse Security
Warehouse security for television products is of paramount importance in ensuring the protection of valuable inventory and preventing losses due to theft or damage. Television products are high-value items that can be attractive targets for unauthorized access. Implementing robust security measures is essential to safeguarding these products throughout their storage and distribution processes. This involves employing advanced surveillance systems, including CCTV cameras and motion sensors, to monitor the premises and detect any suspicious activities. Access control mechanisms, such as biometric authentication and secure entry points, restrict entry to authorized personnel only. Additionally, inventory management technologies, like RFID tagging, can help track the movement of television products within the warehouse, ensuring transparency and accountability. Regular security audits and training sessions for staff members further contribute to maintaining a secure environment. By addressing potential security vulnerabilities comprehensively, warehouse operators can uphold the integrity of their television product inventory and uphold customer satisfaction.
The full content is only visible to SIPMM members
Already a member? Please Login to continue reading.