“Warehousing” is the storage of goods until they are needed. The goal of warehouse operations is to satisfy customers’ needs and requirements while utilising space, equipment, and labour effectively. The goods must be accessible and protected. Meeting this goal requires constant planning and ongoing change.
The question is who should handle warehousing needs: should we do our own or let someone else do it for us? Either way the effectiveness of warehousing operations certainly will contribute to how your customers perceive your organisation. You can produce good products, but for them to receive high praise, your customers need to receive them promptly and in good condition.
Do you know your customers? Do you, for example, consider other departments in your organisation to be customers? If not, there could be trouble. The needs of all of your customers must be considered in all warehouse-planning activities. Otherwise, rather than meeting their needs, you probably are reacting to their demands.
Each problem can have multiple solutions. Such factors as available space, equipment, personnel, and investment capital, as well as a willingness to change, help determine which solutions are available to us. To achieve effective warehouse operations, there are five essential techniques.
The photo below shows the typical operations in a Warehouse

Table of Contents
Receiving Operation
Handle it once. The more times an item is handled and the more individuals involved in the handling, the more time and money you are wasting. Materials must be received and stored with total accuracy. Your database for inventory must be updated as goods are received. Having one person in receiving checking off received materials from a list, then sending the materials for stocking, then sending the list for database updating is not efficient. Inbound processing and the right Enterprise Resource Planning (ERP) software can allow one individual to check in materials and record the inventory in one step. Those materials can then be routed to the correct location in your warehouse.
Select a system of barcode scanning or RFID and take the extra handling out of your receiving operations. This system will also allow the data from incoming shipments to be sent directly to the purchasing and AP departments to update the information for timely payments of invoices.
Just-in-time (JIT) delivery is a method for keeping excess inventory from building up in your facility. The more material you have just sitting on shelves, the more money you have tied up in that inventory.
The photo below shows a Warehouse Personnel checking goods with RFID scanner
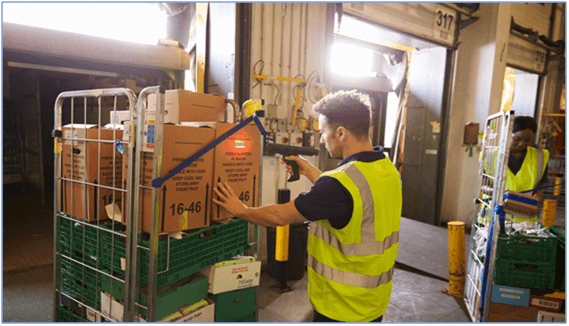
Inventory Layout
The organisation of your warehouse is extremely important since it determines how efficiently new materials are put away and items are retrieved for shipment.
Invest in a storage system that meets the needs of your facility. Your layout should be designed according to your unique operations. If certain items are ordered and shipped together, that is how they should be stored. If a numerical system works best, then that is the system to use.
If your materials are stored on pallets, have the right system in place for easy pallet access. If you use bins, have the racking system to accommodate them. The better your material organisation and access, the less time you lose in preparing orders for shipment. The critical thing to keep in mind is that workers should not have to make several trips around your entire facility to pick orders for shipment. The more time employees spend while traveling around inside your facility, the more productivity that you are losing.
The below photo shows a typical Warehouse Layout
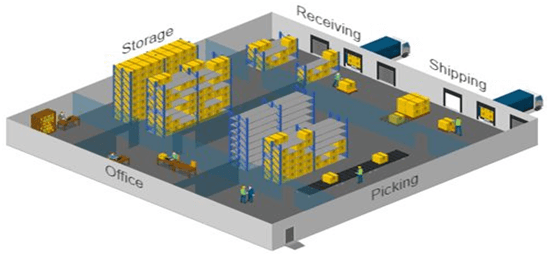
Picking Procedures
Picking and packing are another area where otherwise efficient warehouses can quickly fail. If the wrong materials are pulled, someone not only has to retrieve the correct material, but also the wrong items must be returned to where they belong.
When your stock is organised and marked with (for example) SKUs or a different system, employees will be less likely to pull the wrong materials for shipments.
With the right software, you can combine pick lists to complete several orders and then sort the individual items directly in your shipping department.
The below photo shows a Warehouse Personnel picking in a warehouse
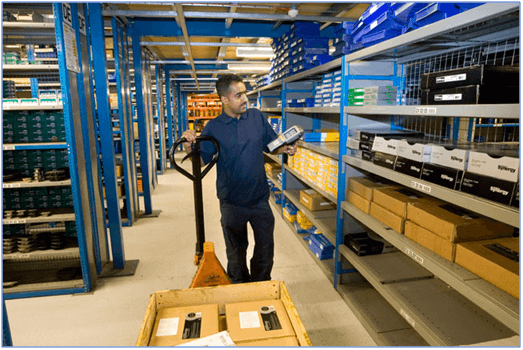
Loading and Shipping
When it comes to loading and shipping, first in is not first out. Trucks must be loaded in the reverse order. The last items placed in the truck will be the first items unloaded.
GPS systems can help you optimise your loading, routing and deliveries. This last step will help you ensure customer satisfaction. You will know where shipments are if customers have questions.
Make use of the organisation, communication, storage and software solutions available to keep your warehouse operations up to date. These implementations will improve your productivity, reduce errors and improve the bottom line for your facility.
The photo below shows a loading bay
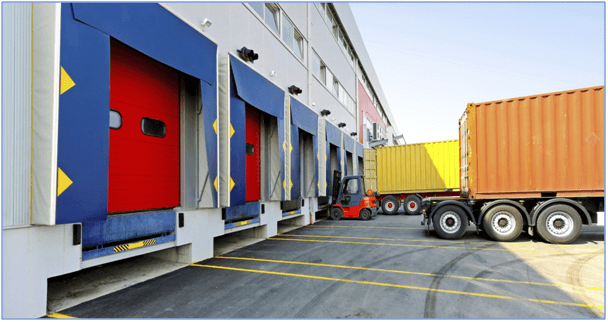
The photo below shows a workplace station before and after 5S implementation
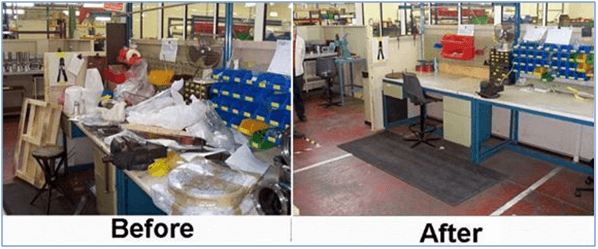
Organising Workstations
An effective workstation can improve productivity because workers do not have to search for tools or equipment. Use the “5S” method from lean manufacturing to ensure your workstations are as organised as possible. It consists of: Sort; Set in order; Shine; Standardise; and Sustain — all techniques designed to keep clutter at bay, reduce errors, and improve safety and organisation.
Conclusion
The warehouse is a key component of the supply chain in emergencies. It buffers uncertainties and breakdowns that may occur in the supply chain. When properly managed and appropriately stocked a warehouse provides a consistent supply of material when it is needed.
References
DLCA (2015) “Warehouse and Inventory Management”. Retrieved from http://dlca.logcluster.org/display/LOG/Warehousing+and+Inventory+Management#WarehousingandInventoryManagement-Definition, accessed 15/03/2018.
Denny Hammack (2018) “Five simple ways to improve warehouse efficiency”
Retrieved from https://www.cips.org/supply-management/opinion/2015/august/five-simple-ways-to-improve-warehouse-efficiency/. Accessed 15/03/2018.
Ee Soon Sern, SIPMM. (2018). “Autonomous Mobile Robotics for Effective Warehousing”. Retrieved from https://publication.sipmm.edu.sg/autonomous-mobile-robotics-effective-warehousing, accessed 10/03/2018.
Jerry Matos (2014) “5 ways to use technology to run a more productive warehouse”
Retrieved from http://www.apriso.com/blog/2014/10/5-ways-to-use-technology-to-run-a-more-productive-warehouse, accessed 15/03/2018.
Nurahim Masruri, MSIPMM. (2017). “Innovative Technologies for Warehouse Implementation”. Retrieved from https://publication.sipmm.edu.sg/innovative-technologies-warehouse-implementation, accessed 10/03/2018.
Rick Stinchcomb (2012) “Warehouse Operations”. Retrieved from http://aaupwiki.princeton.edu/index.php/Warehouse_Operations#Introduction_to_Warehouse_Operations, accessed 15/03/2018.