Most businesses have plenty of areas to improve, especially in their warehouses. Good inventory control techniques for warehouse management start with an organised and well-maintained site. Managers should regularly inspect warehouse operations, ensuring that stock is stored in a way that allows staff to easily and safely access it. Below are some best practice inventory control techniques to help improve your operations and ensure the smooth running of your warehouse.
Table of Contents
Know Your Best Sellers
and orders for each product or customer. This information can be extremely useful for determining what your best sellers are. By placing this high-volume stock closer to the shipping area and ensuring it is easily accessible, you can eliminate unnecessary labour time.
Stock Inventory as Per Need
Keep the stock levels at 1.5 times the normal for abstaining from obstructing of working capital. With enhanced inventory holding, you can viably diminish the expense of storage.
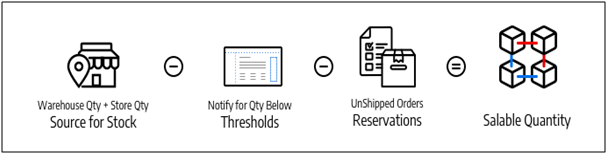
ABC Inventory Control
ABC analysis of inventory helps you keep working capital costs low because it identifies which items you should reorder more frequently and which items don’t need to be stocked often – reducing obsolete inventory and optimizing the rate of inventory turnover
A-Items – Best-selling items that don’t take up all your warehouse space or cost
B-Items – Mid-range items that sell regularly but may cost more than A-items to hold
C-Items – The rest of your inventory that makes up the bulk of your inventory costs while contributing the least to your bottom line
Plan an Efficient Layout
Plan the usage of each space in warehouse. Imprint each rack to limit perplexity while storing and getting stuff. Make sure warehouse has enough space for forklifts or pallet jacks to mobilize.
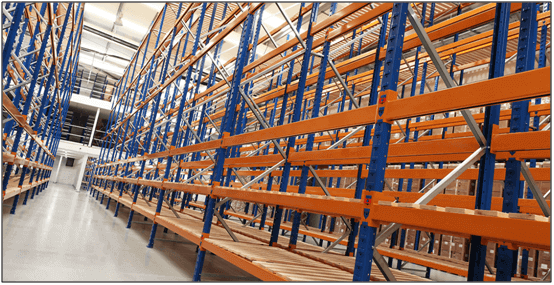
Use Fixed and Movable Tracking Options
Using movable tracking options will allow you to see where you placed a product, how you can access it and if it’s ready for shipment. Movable tracking enables you to see where items are located at all times, and it makes the entire process faster, easier and more intuitive.
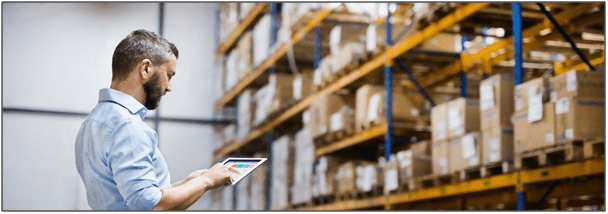
On the other hand, fixed tracking is also an option for many businesses. This way you can easily manage and assign destinations with precise efficiency. You can seamlessly combine fixed tracking with movable tracking if you want to acquire optimal results. At the end of the day, fixed and movable tracking options can do wonders if you use them correctly. Often times there is a learning curve and initial investment incorrect inventory management processes, but these short-term investments have large payoffs in the future.
First-in-first-out (FIFO) Inventory Control
The first in, first out (FIFO) method of inventory valuation is a cost flow assumption that the first goods purchased are also the first goods sold. A simple principle, yet vitally important to mention – especially if dealing with perishable items. For most retailers, the last thing you want is always using the newest stock to fulfil orders. This leaves older inventory sitting in the warehouse and susceptible to damage, decay or passing best before dates. It’s worth making a rule to store new inventory from the back of shelves and then take from the front – automatically enforcing a FIFO system.
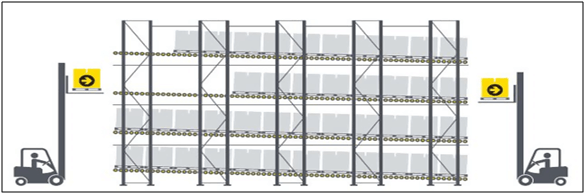
Use a Quality Inventory Management Software
Proper inventory management for warehouses can be done as long as have the right software. The latest tools on the market allow to acquire real-time updates on the products, which can be tagged with RFID for quick and accurate inventories.
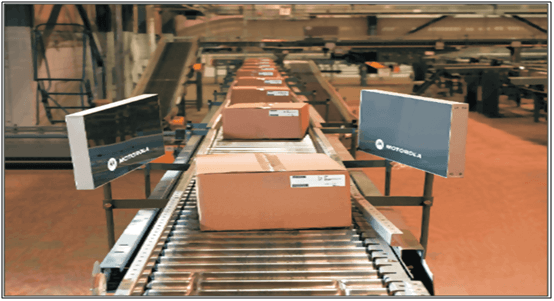
Apply Cross Docking to Maximize Space
The objective of cross docking is to reduce the shelf storage time of stocks in the warehouse. It helps in transporting warehouse delivered goods quickly to the outbound carriers that can take the stocks to distribution centres.
The full content is only visible to SIPMM members
Already a member? Please Login to continue reading.