Efficient warehouses ensure fast and accurate deliveries. This is critical for customer satisfaction. Furthermore, a well-organised warehouse layout promotes effective warehouse management and productivity. Warehouse operations require interaction between people, machinery, and technologies. Therefore, training new staff to be skilled is necessary. This ensures that the processes are understood. Training should emphasise the significance of adhering to safety and security protocols so that workflows are rigorously followed. This will increase workers’ productivity, which promotes efficiency in a warehouse’s daily operations. All these factors contribute to and reflect its success. This article discusses several crucial factors for a successful e-commerce warehouse.
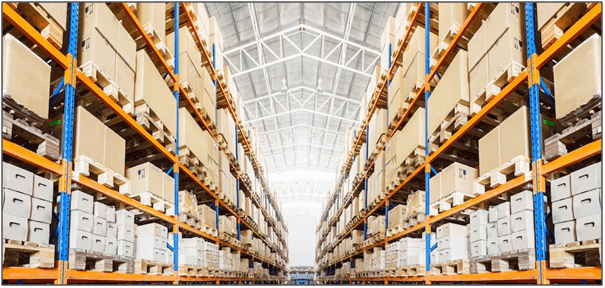
Table of Contents
Warehouse Organisation
Warehouse organisation includes the management of resources and the arrangement of items in a storage facility. It involves creating and putting in place mechanisms, effectively storing and retrieving products, keeping track of inventories, and maximising space usage. Effective warehouse management is essential to ensure that items are accessible when required. This reduces wastage, damage, and losses. An effective workplace should be well-organised so that it offers a safe environment for the workers. The flow of activities should be orderly and in sequence. The identification of work zones and inventory in the warehouse will ensure long-term organisation and smooth facility movement. Companies can consider putting notices for any risks or ceiling limits to improve staff safety.
Inventory Management
Inventory management is another crucial factor for successful e-commerce warehousing. E-commerce warehouses need to have an efficient system for receiving, storing, and tracking inventory. They should also have real-time visibility for inventory levels to ensure that they can fulfill orders on time. Inventory management systems should also be able to handle multiple sales channels, such as online marketplaces and direct sales to avoid overselling or underselling products. Inventory categorisation and appropriate storage techniques make the most out of a current facility. They also free up room that was previously wasted. This in turn increase capacity and improve productivity. E-commerce businesses can ensure timely and accurate order fulfillment by optimising these factors. It will then increase customer satisfaction and loyalty. Ultimately, a successful e-commerce warehousing operation is essential to fulfilling customers’ orders and the growth of an e-commerce business.
Order Fulfillment
In the context of eCommerce, fulfillment refers to the end-to-end procedure of sending a customer’s online order. The fulfillment process starts when a client puts an order on an eCommerce website. Making sure the consumer receives the item they requested within the time frame given is the responsibility of the store, supplier, or merchant. Several approaches can be taken. Direct-to-consumer fulfillment eliminates the need for outside logistical companies. Products are listed on a retailer’s website. When a customer makes a purchase, the product is delivered to them straight from the seller or manufacturer. When having control over the inventory, eCommerce fulfillment refers to the process of getting an order into the customer’s hands. This supply chain link also involves receiving and storage. Timely and accurate order fulfillment is essential for customer satisfaction and repeats business. E-commerce businesses must have efficient order picking and packing processes with the ability to quickly process orders and ship products. This may involve using technologies such as barcode scanners, automated sorting systems, and shipping software.
Technology
E-commerce warehousing heavily relies on technology to streamline operations and improve efficiency. Various technologies and warehouse management systems (WMS) are necessary for inventory control, product tracking, and effective order fulfillment. They enable real-time inventory tracking, aid in optimising inventory placement, and help to automate several processes that include selecting and packaging products. Barcode scanning technology makes it possible to track inventory accurately and efficiently. This in turn lowers mistakes to happen and boosts productivity. Its implementation helps to manage inventory, track orders as well as automate picking and packing processes. As a result, there will be precise picking, rapid product identification, and real-time inventory level updates. Automated storage and retrieval systems (ASRS) technology aids in maximising the use of warehouse space, enhances order accuracy, and lowers the possibility of mistakes in product handling. This technology automates the process of storing and retrieving goods, increases efficiency, and decreases the duration required to complete orders. Moreover, technologies like virtual reality (VR) and augmented reality (AR) can also be used to train employees on warehouse operations and ensure consistency in handling and storing products. WMS data can be used to accurately classify and slot inventory, decide on the best storage solution, and monitor inventory movement.
The full content is only visible to SIPMM members
Already a member? Please Login to continue reading.