EPC refers to projects involving engineering, procurement, and construction. The term ‘Order fulfillment’ is commonly used to describe the act of distribution (logistics) or the shipping function. In a broader sense, it refers to the many ways firms respond to customer orders, and the processes they follow to move sold products or services to a customer.
Logistics management is the part of supply chain management that plans, implements, and controls the efficient, effective forward, and reverse flow and storage of goods, services, and related information between the point of origin and the point of consumption in order to meet customer’s requirements.
The challenges facing the construction industry include labor shortages, stagnant productivity level, safety and adoption of technology. The construction industry is not attracting enough talent to meet growing demand. Firms are having trouble finding qualified workers. Workers in construction are aging out and retiring at a faster rate than the younger generation is coming in.
Table of Contents
Effective Site Planning
Plan site set-up to move labour, plant, and materials around site efficiently (e.g. hoarding, gates, site accommodation, cranes, hoists, security, temporary services, material delivery, and waste management strategy, catering).Plan internal and external logistics routes through the project phases focusing on separation of vehicles, machinery, and people. Lay down areas and offloading points. E.g. Hoists can be mounted in a variety of ways. Pre-plan the usage of hoists to ensure planned asset meet the needs of the program.
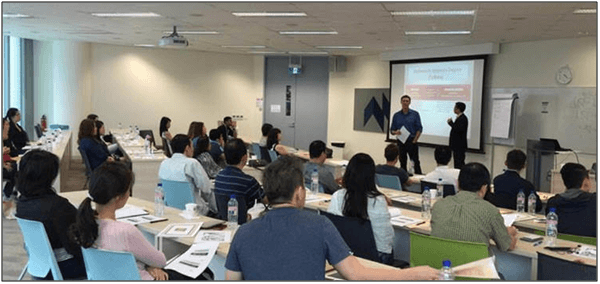
Peak Planning and Execution
It’s always a challenge to deliver a successful peak period due to the continued growth in e-Commerce and national retail events like Cyber Monday. However, the peak is a crucial time of the year for many businesses, especially those with seasonal spikes – and navigating it successfully is the key challenge. Competency in e-Commerce, particularly in managing its ongoing growth, is fundamental, along with excellent forward-planning, performance analysis, and forecasting – all of which fall under the umbrella of peak planning and execution. Access to information is a key factor in delivering a successful peak, so getting the right people on board that understand and know how to manipulate data is key. They’ll also need to possess comprehensive knowledge of the interim marketplace at all levels, as the workforce expands according to demand.
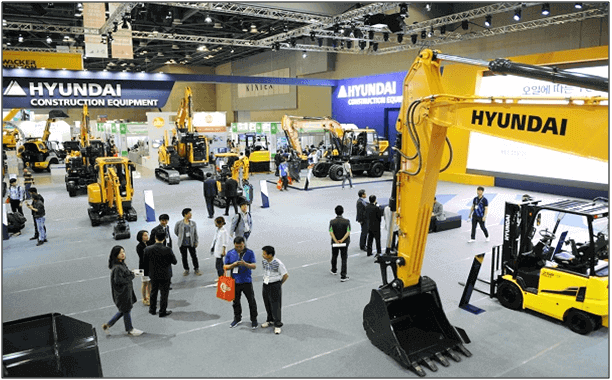
Logistics Strategy
Logistics is not confined to tactical decisions about transportation and warehousing. Logistics strategy is the set of guiding principles, driving forces and ingrained attitudes that help to coordinate goals, plans and policies between partners across a given supply chain. Article body. The four types of logistics are supply, distribution, production and reverse logistics.
A formal logistics strategy provides a foundation for the constantly changing nature of the supply chain. Companies are better prepared to be flexible and adapt to the changes with a logistics strategy in place. Not having one in place means companies will not be prepared to gauge the impact of any change in the supply chain has on its operations. This negligence can significantly impact customer service.
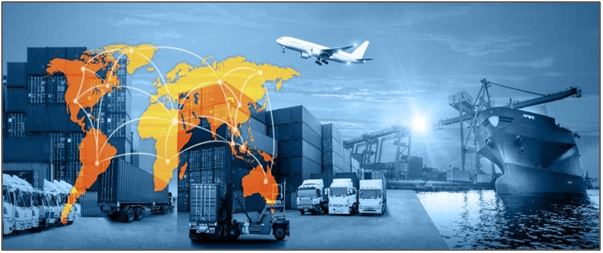
In the logistics strategy, there are 2 important areas that need careful consideration.
1. Develop Logistics Plan
Strategic logistics plans define how business plans to deliver products or services to customers. It addresses logistics in a methodical way that allows your business to scale operations or increase profitability and the importance of logistics on construction sites. In the above case, logistics is defined as the planning, execution, and control of procurement, transport, and stationing of workers and material and other resources to achieve the goals of a construction project.
Distribution resource planning (DRP) is a method used in business administration for planning orders within a supply chain. DRP enables the user to set certain inventory control parameters (like a safety stock) and calculate the time-phased inventory requirements.
2. Operations Planning In Logistics
Logistics is the management of the flow of goods from the supply to the point of consumption. Operation planning is a process that seeks to understand and develop operational processes. Inventory/stock control is a critical part of supply chain management.
Supply Chain Management
Describe the characteristics of the site, including site access/egress, storage capacity, and arrangement by programmed, labor, hoists, cranes, etc. Use the description to produce daily, weekly and long term movement’s plans. Plan and integrate with key contractors to meet the needs of the planned programmed and de-confliction of onsite space and time where appropriate.
The full content is only visible to SIPMM members
Already a member? Please Login to continue reading.
References
Adam Robinson. (2018). “What is Reverse Logistics and How Is It Different than Traditional Logistics?” Retrieved from https://cerasis.com/what-is-reverse-logistics, accessed 02/07/2019.
Brian Bass. (2019). “Logistics & Operation Planning”. Retrieved from https://smallbusiness.chron.com/logistics-operation-planning-14618.html, accessed 03/07/2019.
Chris. (2011). “What is Order Fulfillment?” Retrieved from: https://www.rileylife.com/blog/what-is-order-fulfillment, accessed 01/07/2019.
Michael Page. (2018). “10 skills your logistics team need to know”. Retrieved from https://www.michaelpage.co.uk/our-expertise/logistics/10-skill-your-logistics-team-need-know, accessed on 02/07/2019.
Mohamed Hardi Bin Abdullah, GDLM. (2018). “Autonomous Trucking in Logistics Transportation”. Retrieved from SIPMM: https://publication.sipmm.edu.sg/autonomous-trucking-in-logistics-transportation, accessed 04/07/2019.
Sonia Lai Jie Yin, DLSM. (2018). “Key Success Factors for Effective Logistics Practices”. Retrieved from SIPMM: https://publication.sipmm.edu.sg/key-success-factors-effective-logistics-practices, accessed 04/07/2019.