In developing a strategic supplier, the organization must ensure that the selected supplier has obtained certifications such as ISO/TS 16949 or ISO 9001, financial stability, products innovation ability, R&D and engineering capability to design and develop new products, and cost competitiveness, and commitment to on-time delivery. Organizations must consider factors such as market supply risks, supply base rationalization, supplier performance evaluation, and supplier new product development capability when an organization decided to develop a strategic supplier because the essential and critical parts or services will be supplied by them for a long-term period and organization cannot afford any risks and disruptions to the supply chain.
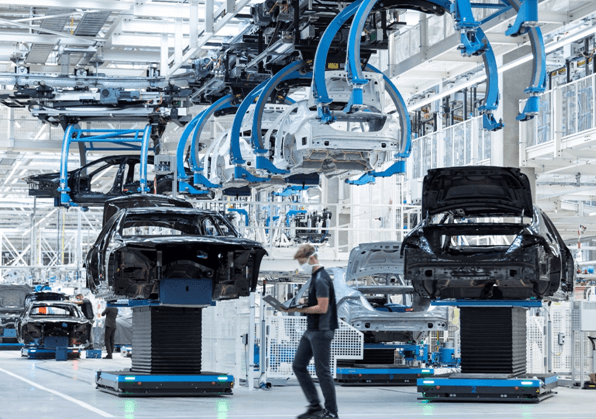
Table of Contents
Assessing Market Supply Risks
A vehicle consists of an estimated 30 million individual parts, which will be either in-house manufactured or supplied by a third party. Poor visibility and routing of products can result in delays in the manufacturing process. Disruptions in the supply chain will cause the manufacturing and distribution of critical components to slow down or cease completely, causing manufacturing downtime and production line to stop.
The profitability of an organization can be affected by lack of visibility, and high fixed and variable costs. It is essential to obtain the transparency of expenses on both a fixed and variable basis, since machinery and production line investment, employees’ high salaries, new product research and development, commodities cost, and other party costs can significantly impact the price and profit margins.
Products that do not meet the quality requirement and products with defects manufactured will lead to product failures and product recalls. Product quality issues can be caused by a lack of suppliers’ oversight and auditing. Due to this, the reputation of the organization will be directly affected and result in a loss in revenue.
External impacts from the political, economic, environmental, marketplace, and pandemics can cause significant disruption to the automotive supply chain. The cost of the import and export of products and vehicles can be significantly affected by tariffs, trade deals, and political maneuvering. The earthquake and tsunami in Japan in 2011 and the coronavirus epidemic in China in 2019 had caused parts shortages and wreaked havoc across the global supply chain.
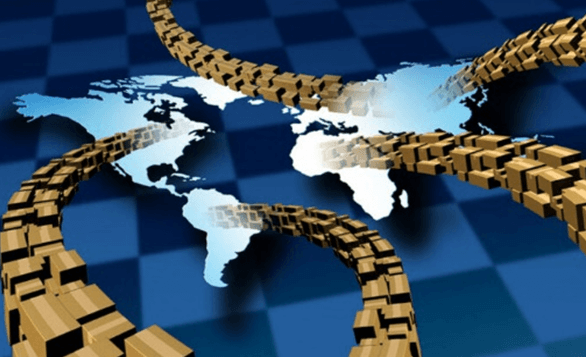
Rationalization of the Supplier Base
Rationalization of the supplier base can be explained as the utilization of the right appropriate suppliers in the right quantity. The supply chain will become more complicated when there are a lot of suppliers in the company and the cost to manage will increase. The company must ensure that there will be no supply chain disruption when performing the action to reduce the number of suppliers and must also ensure that the quality standard must be maintained and cost objectives are achieved.
To ensure the stability of the product quality, the company must select suppliers who have implemented quality management systems, such as International Organization for Standardization (ISO). The number of suppliers can be minimized with the implementation of these criteria. At the same time, the consistency of the product quality can be controlled and the rejection rate can be minimized.
By minimizing the number of existing suppliers, the orders given to the remaining approved suppliers will be increased. This means that the company will have more bargaining power to negotiate with suppliers to reduce their prices. Not only the cost reduction goal is achieved, but the company can also spend more time concentrating on monitoring the supplier’s performance and working together with the supplier to improve the product quality.
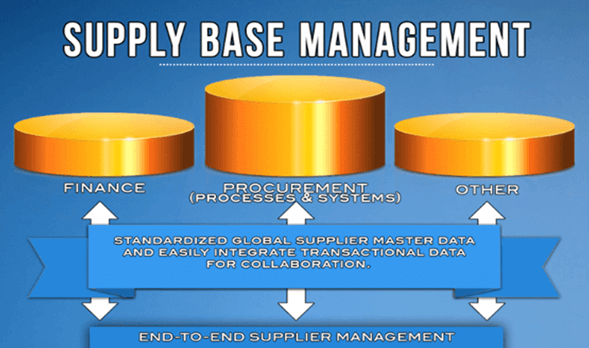
Managing and Evaluating Supplier Performance
The profitability of an organization is directly influenced by supplier performance because organizations depend on cost reduction, on-time delivery, and quality service to increase profits. Managing, measuring, and analyzing suppliers’ performance can allow a better understanding of the impact of cost, quality, and risk on businesses. Two of the important component that required organization attention is identifying if the supplier has fulfilled the performance targets stated in the contract and cooperating with the supplier to identify the performance gaps and implement improvement actions to improve the gaps. Supplier’s performance can be evaluated using key performance indicator, which is Quality and Defects performance indicators and the Supplier Complaint indicator. Organizations can use the indicators to record and monitor the quality performance of the supplier throughout the year. Defective and deviated products must be strictly restricted from being assigned to the production department as they will impose risks to the consumer and affect the organization’s reputation. By computing the ratio of discrepancy invoices with total invoices paid, the percentage of a defective product can be calculated.
The full content is only visible to SIPMM members
Already a member? Please Login to continue reading.
References
Automotive News Europe. (2020). “Nissan faces global parts shortage due to coronavirus, report says” Retrieved from: https://europe.autonews.com/automakers/nissan-faces-global-parts-shortage-due-coronavirus-report-says, accessed on 18/03/2022.
Blume Global. (2022). “Top 4 Automotive Supply Chain Challenges and Solutions”. Retrieved from https://www.blumeglobal.com/learning/automotive-supply-chain/, accessed on 18/03/2022.
Carol Chiam Yin Mee, DPSM. (2021). “Key Performance Indicators for Evaluating Suppliers”. Retrieved from SIPMM: https://publication.sipmm.edu.sg/key-performance-indicators-evaluating-suppliers/, accessed on 18/03/2022.
Lear Corporation. (2022). “Supplier Diversity”. Retrieved from https://www.lear.com/suppliers/supplier-diversity, accessed on 26/03/2022.
Song Fang, DPSM. (2021). “Essential Steps to Manage Supplier Performance”. Retrieved from SIPMM: https://publication.sipmm.edu.sg/essential-steps-managesupplier-performance/, accessed on 18/03/2022.
Statista. (2022). “Estimated worldwide motor vehicle production from 2000 to 2020”. Retrieved from https://www.statista.com/statistics/262747/worldwide-automobile-production-since-2000/, accessed on 26/03/2022.
Taktikos Evangelos. (2018). “Supplier involvement in New Product Development: A literature review and conceptual model”. Retrieved from https://repository.ihu.edu.gr/xmlui/bitstream/handle/11544/29007/TaktikosEvangelosDissertation.pdf?sequence=1, accessed on 18/03/2022.
Teddy Oh Sing Yie, DPSM. (2018). “Techniques for an Effective Global Sourcing Strategy”. Retrieved from SIPMM: https://publication.sipmm.edu.sg/techniques-effective-global-sourcing-strategy/, accessed on 26/03/2022.