This article highlights the five key techniques for inventory management and control. Inventory Management is “the practice of planning, directing and controlling inventory so that it contributes to the business’ profitability”. Inventory management can help business be more profitable by lowering their cost of goods sold and/or by increasing sales.
The five important techniques for effective inventory control are:
1. Demand forecasting
2. Reorder point
3. Inventory turnover ratio
4. Performance measurement
5. Cycle counting
Focusing on these five fundamentals can yield significant bottom-line savings.
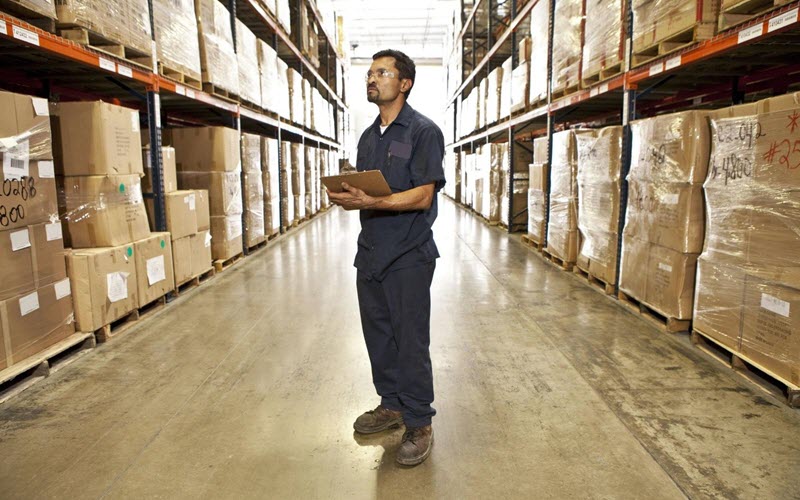
Table of Contents
1. Demand forecasting
The importance of demand forecasting can be short term, midrange, or long term. Accurate demand forecasting has the highest potential savings for any of the principles of inventory management. Both over supply and under supply of inventory can have critical business costs. Whether it is end-item stocking or raw component sourcing, the more accurate the forecast can be.
Establishing appropriate min-max management at the unique inventory line level, based on lead times and safety stock level help ensure that you have what you need and when you need it. This also avoids costly overstocks. Ideal inventory increases incremental costs due to handling and lost storage space for fast-moving.
2. Reorder point / Replenishment order
Inventory level of an item which signals the need for a replenishment order. The reorder point is classically viewed as the sum of the lead demand plus the safety stock. At a more fundamental level, the reorder point is a forecast of the future demand. The calculation of an optimized reorder point typically involves the lead time, service level, and the demand forecast.
In order to increase productivity, most ERP and inventory management systems implement replenishment rules to automate operations to some extent. Replenishment is typically triggered when the inventory level hits the reorder point (also called reorder trigger level), a setting from the system.
3. Inventory turnover ratio
The inventory turnover is the number of times the inventory must be replaced during a given period of time, typically a year. It is one of the most commonly used ratio in inventory management, as it reflects the overall efficiency of the supply chain, from supplier to customer. This ratio can be computed for any type of inventory (materials and supplies, work in progress, finished products or all combined), and it can be used for retail as well as manufacturing.
This is a calculation used to determine how quickly inventory is used up or “turned over” in a given time period. The higher the ratio the shorter the shelf life of the inventory and typically leads to higher sales volume and profitability for companies with lower profit margins. Inventory turnover should be closely watched for every item in the warehouse. Over the course of the product’s life cycle, demand will fluctuate and cause variability in the supply chain. Tracking demand patterns are one way to ensure product replenishment calculations are accurate and optimized.
Some companies also frequently express their inventory as days or weeks of supply. The main benefit of this approach is that it produces values that are rather intelligible and provides an immediate point of comparison with the lead time. In this case, another ratio, derived from the first, indicates how many days’ worth of inventory is available in the system – or how many days will it takes to sell the inventory.
When this ratio is applied to individual products, it is frequently called the stock cover.
4. Performance measurement
Evaluation and performance measurement requires that targets are established, against which actual achievements can be compared. Inventory systems enable this to be done through the provision of both volume and financial data when planning the inventory environment. However, care must be taken to fully understand the basis upon which the targets have been set as well as ensuring that the evaluation and performance measurements are compatible in the collection and presentation of the data, to the target setting process.
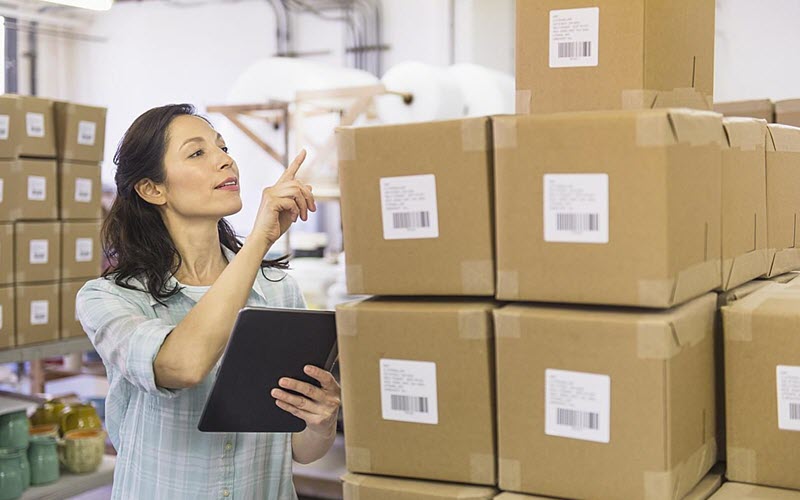
5. Cycle counting
One of the key methods of maintaining accurate inventory is cycle counting. This helps measures the success of your existing processes and maintain accountability of potential error sources. There are financial implications to cycle counting. Some industries require periodic 100% counts. These are done through perpetual inventory count maintenance or though full-building counts.
The full content is only visible to SIPMM members
Already a member? Please Login to continue reading.
References:
Artin.V. (2017) ‘Top 5 Principles of Inventory Management’.
Retrieved from https://www.purchasing-procurement-center.com/principles-of-inventory-management.html (accessed 3 December 2017)
Joannès.V. (2012) ‘Reorder Point Definition’.
Retrieved from https://www.lokad.com/reorder-point-definition (accessed 3 December 2017)
Joannès.V. (2012) ‘Stock Replenishment Definition’.
Retrieved from https://www.lokad.com/stock-replenishment-definition (accessed 3 December 2017)
Daniel Fritsch (2015) ‘6 Inventory Control Techniques for Stock Optimization’.
Retrieved from https://www.eazystock.com/blog/2015/08/03/6-inventory-control-techniques-for-stock-optimization/ (accessed 3 December 2017)
Mr. J. O. Kyei. (2008) ‘Principles and Techniques of Managing Inventory’.
Retrieved from http://apps.who.int/medicinedocs/documents/s17396e/s17396e.pdf (accessed 3 December 2017)
Ralph.C. (2016) ‘4 Benefits of Cycle Counting’.
Retrieved from https://blog.southeastcomputers.com/4-benefits-of-cycle-counting (accessed 3 December 2017)