Procurement is an important aspect of a construction project, it is the process of acquiring high-quality goods and services within a specific budget and guidelines to bring a project to completion. Building materials are expensive to procure, thus implementing the right procurement methods could help the company to maximize the efficiency of a project and save cost. Delays in material delivery and material shortage are among the challenges encountered in the construction industry. These delays and shortages of material will delay the project and cause significant schedule disruptions. This article discusses some of the procurement methods that can be implemented by construction companies. These methods can help companies to mitigate supply chain disruption and stay competitive in the construction industry.
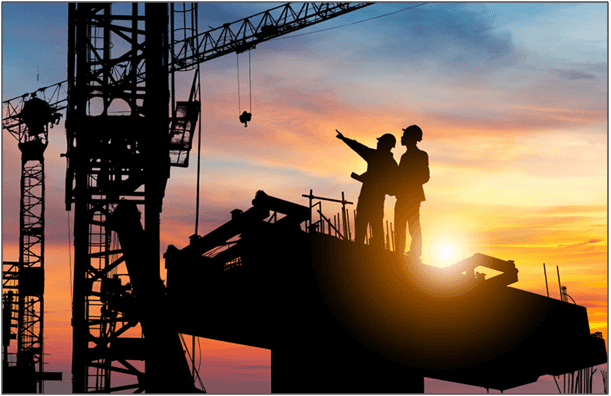
Table of Contents
Purchasing by Requirements
Purchasing by requirements method refers to goods being purchased only when needed and in the desired quantity. This method is normally used for uncommon items that do not require keeping stock or order in advance. The purchasing department must know the suppliers of such goods in order to be able to make purchases without wasting time. When the material prices are not stable or the project requirements are not consistent, it is advantageous for the company to implement this method by buying the materials in lesser quantities. It is a key consideration for the construction industry, as it allows the company to increase its efficiency, reduce its wastage, minimize raw material inventory and lessen the amount of inventory carrying cost.
Scheduled Purchasing
With this scheduled purchasing method, the suppliers are given a probable time schedule to prepare and arrange for delivery. An accurate schedule is prepared for estimating future requirements. These requirements are normally based on the needs of the project. The suppliers are informed of the requirements and the orders are sent accordingly by them. However, the schedule provided to the supplier is not a contract, it is more like a verbal agreement made between the purchaser and supplier as a form of term and condition of the purchase. The aims of implementing this procurement method are minimizing raw material inventory level, getting fast service from the suppliers when it needs to replenish stocks, receiving good quality products, and enjoying low prices from the suppliers.
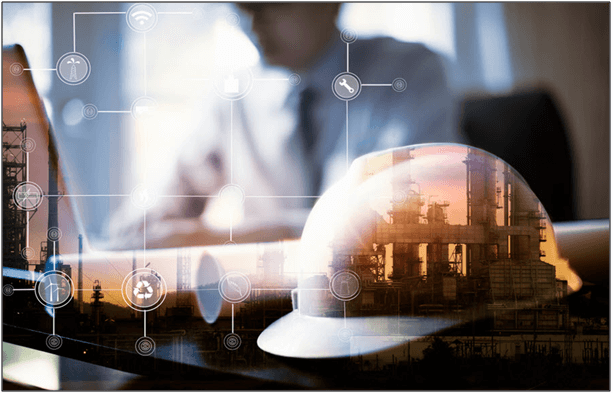
Contract Purchasing
As the name suggests, contract purchasing is the purchasing under contract with a supplier, in which the purchaser will receive a regular supply of goods at an agreed price for a fixed duration as stated in a signed agreement with the supplier. A contract is defined as a better price or discount on the purchased products. This procurement method allows companies to reduce their operational costs and gain greater control over spending. Although the goods are procured in the future the price and other terms and conditions are fixed at the time of the contract. This method is useful when prices are expected to increase, and the purchaser can accurately estimate the material requirements for future usage.
Purchasing for Design and Build
Design and Build is a procurement method in which the main contractor is appointed as a single point of responsibility for delivering the entire project. The main contractor has been appointed to both design and construction works as described in the contract. The main contractor has a direct contract with the client, this brings ease of communication because the client only needs to liaise with one party. This method is opposed to the traditional procurement method, in which the client first has to appoint consultants to design, and then a contractor is appointed to do the construction. The benefits of implementing this design and build method are a reduction in project duration due to earlier commencement on site, earlier price certainty, and a single point of responsibility for the design and build.
Purchasing for General Contracting
With this general contracting approach, the contractor agrees to build the design that is provided by the employer. The contractor is only responsible for the construction work and not for the design. There are three types of general contracting, namely lump sum contract; measurement contract; and cost reimbursement contract. Under a lump sum contract, the contractor agrees to complete the project for a predetermined price. In this agreement, the contractor submits a total project price instead of bidding on each individual item. In a measurement contract, the contractor provides the client with a price estimation for each work, rather than an estimation for the project as a whole. While on the other hand, for cost reimbursement contract, the client pays the contractor the costs incurred during the project plus a set amount of money for profit, which can be worked out by a percentage of the total price of the project.
Managing Construction Timelines
A construction timeline is a schedule created to manage tasks and events smoothly in the construction project. This is a significant aspect of the construction process as it helps to ensure that the project can be completed on time. Managing construction timelines is an important approach as on-time-delivered projects can help to control costs and it helps the company to schedule the project and tasks. A few factors that can impact the construction timelines are project size and overall difficulty, weather and time of year, availability of construction workers and materials, permit approvals, and type of construction. The benefits of managing construction timelines include it allows all members to set expectations within the team, enabling better communication between contractor and client, and helping to create a helpful action plan.
The full content is only visible to SIPMM members
Already a member? Please Login to continue reading.