The food inventory plan maintains everything in order, organized, and linked. A little inventory mistake or blunder can significantly influence the company’s costs and profitability. Compared to other businesses, the food industry conducts inventory control differently. Food safety and health laws must be maintained since many food products are perishable and have a short shelf life. The best supply chain management procedures must be used to guarantee customer safety, including tracking each batch during manufacturing, packing, and delivery. Without proper inventory control systems, there is a big chance of running out of goods, having a surplus and obsolete stock, or having to cope with spoiling. Inventory is usually perishable goods in the food sector. A successful firm will manage the availability chain through good inventory management. As a result, how a company handles and manages its food inventory is critical to the goods’ safety. This article discusses some practical methods for controlling food inventory.
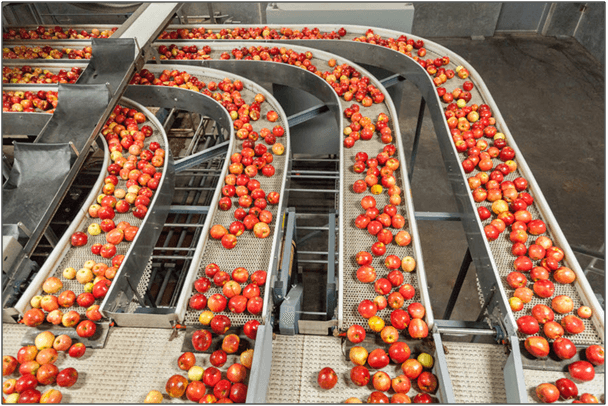
Table of Contents
Batch Number Tracking Technique
The batch number tracking technique enables users to group and monitor similar commodities to track inventory expiry or locate defective goods. There is a constant risk of contamination for food and beverage (F&B) businesses at any stage in the supply chain. For example, improper storage makes fresh and perishable items more prone to spoilage. The company must be ready to issue a recall if a product becomes contaminated or spoiled. The batch number tracking technique is the best technique that can assist F&B producers in recalling unsafe food goods. In the event of a recall, especially in the food manufacturing or wholesale industry, batch tracking skills must always remain proactive.
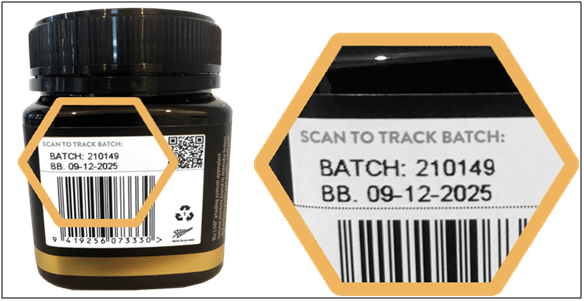
Consignment Inventory
A consignment business is a legal partnership in which a wholesaler, supplier or manufacturer delivers goods to a recipient (retailer) for sale. Consignment means placing goods in another party’s inventory but retaining title until the goods are sold. Products sold in this consignment model are most likely seasonal, fresh, or second-hand. At the start of the partnership, the sender and recipient must agree on mutually beneficial means from the outset. For example, the shipper and the consignee must state the fee the retailer will charge the supplier and how long the consignee agrees to hold the inventory before returning the remaining stock.
Economic Order Quantity Technique
Economic Order Quantity (EOQ) is designed to help businesses reduce the cost of purchasing and maintaining inventories. The EOQ technique enables firms to estimate the amount of stock they require based on factors such as total cost of production, demand growth, etc. EOQ formula is the square root (√) of 2x (the annual unit requirement multiplied by the order cost per order) divided by the yearly cost of ownership per unit. This formula selects the maximum number of units to reduce purchase, holding, and other costs. When the inventory reaches the EOQ threshold, the system will immediately notify the company to place an additional order. Organizations can use this strategy to meet demand while avoiding stockouts.
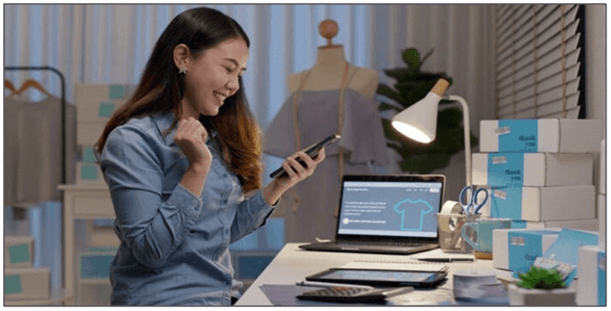
Minimum Order Quantity
The Minimum Order Quantity (MOQ) is the small number of items that must be purchased from a supplier in a single transaction. MOQs from suppliers, both large and low, will have a substantial impact on inventories. They will influence the number of days stock is kept on hand, the frequency of buy orders, and the amount of warehouse space available. If the company is unable to meet the supplier’s MOQ, it may be obliged to seek alternative suppliers or pay a premium to get less than the minimum order quantity. MOQs may help a company maintain healthy profit margins but they can also aid improve inventory control and keep purchasing prices low.
ABC Analysis Technique
ABC inventory analysis is a technique based on the Pareto principle. The 80/20 rule may be used for task prioritizing, inventory management, and treating each thing with care. The ABC analysis is used to categorize stock inventory based on its values and consumption during a specific period, such as a year. Products in category A have the highest stock values and consumption compared to those in category B, while items in category C have the lowest among the three. Most firms prefer to focus their efforts on stock management in category A to maximize their potential for cost reductions. Because categories B and C have lesser value and utilization, businesses may keep buffer inventories to avoid a stockout.
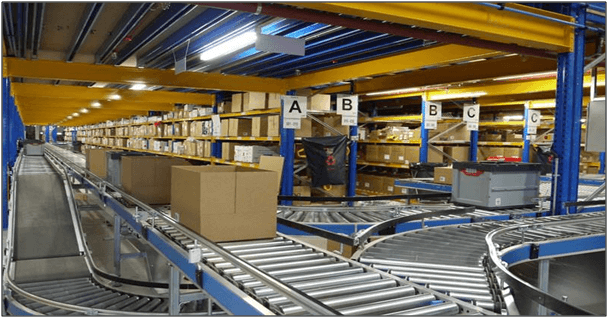
Just-In-Time Technique
Just-In-Time (JIT) is a method of inventory management in which products are obtained from suppliers just when needed. The primary goal of this strategy is to lower inventory holding costs while increasing inventory turnover. JIT inventory management necessitates close collaboration with suppliers to complete orders quickly and ensure that goods arrive on time. JIT inventory is popular among small businesses and large organizations because it improves cash flow and lowers the capital required to run the firm. JIT inventory has helped retailers, restaurants, on-demand publishing, technology production, and automobile manufacturing. JIT technique helps reduce waste and increase efficiency by reducing the chance of overstocking and being out of stock. JIT can be said to be an effective method as it reduces the effort required for inventory management.
Safety Stock Inventory Technique
One of the most fundamental inventory management methods is safety stock level. It assists businesses in avoiding stockouts and the resulting revenue, customer, and market share losses. Before implementing this inventory management strategy, the company must collect data on seasonal sales variations, consumer purchasing patterns, and sales cycles. Raw materials for manufacturing must have a range of lead times. To ensure that the company has enough inventory for replenishment, an additional stock must be ordered and stored at all times. Stockouts are likely due to inaccurate projections or unexpected changes in customer demand. Keeping a small stockpile on hand is necessary to protect against market demand fluctuations.
The full content is only visible to SIPMM members
Already a member? Please Login to continue reading.