The purpose of using key performance indicators is to measure the performance of the critical suppliers’ in the company. To determine the supplier performances, the company must set the criteria of what to measure and when to measure. The setting should not be biased and not base on personal liking or preferences. It must be clear and measurable to be alight with the business objective and goals. The company can measure the suppliers’ capabilities through quality, delivery, order accuracy, and orders fulfillment with a specific timeline. Key performance indicators can produce data to allow the company, stakeholders to review the goal setting and analyze the current performances across the organization. The company must review the key performance indicator regularly to make the necessary adjustment from time to time with the right decision. This article discusses some key performance indicators for evaluating suppliers.
Table of Contents
Quality and Defect Performance Indicators
Quality is one of the key performance indicators in the evaluation process in a company. A proper checklist and supporting documents allow the company to identify the quality of the products supplied by the suppliers throughout the year. A defective and low-quality product should not be use and must place in a quarantine area upon receiving. It imposes a risk to the user and affects the company’s reputation. Reworking products is time-consuming and will incur additional indirect costs, such as transportation, packaging materials, and other handling costs. Quality products allow the company to purchase and use them with confidence without any complaints or risk. In order to calculate quality or defective products, a company can compute the ratio of the disputed invoices to the total invoices paid. The company can also use the ratio of the number of low-quality products to the totals of products tested.
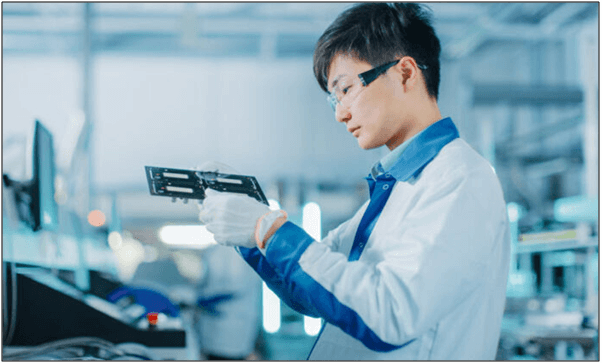
Supplier Complaint Indicator
A complaint is raised when a product is faulty or deviates from the agreed product specification. For an effective complaint, the company must first gather all the information stated on the products like the batch number, manufacturing date, the problems of the products, and the affected department. It will be good to include videos or photos of the defective products as additional support to the complaint. Supplier complaint forms are usually sent out by the purchasing department to request the suppliers to investigate and provides the CAPA (corrective action and preventive action) with the effective date. The company can provide support to the suppliers who are facing the problem. If the problem continues, the company should stop using the supplier and switch to other suppliers. To calculate the complaint – total numbers of orders / numbers of complaints to get the percentage.
The full content is only visible to SIPMM members
Already a member? Please Login to continue reading.