Supplier evaluation and selection is one of the most important factors in the purchasing function of any organization. Proper planning and organizing the list of suppliers can help to improve the efficiency of its supply chain. However, many experts agree that there is no best method to evaluate and select suppliers, and that explains why companies ended up using different approaches. Ultimately, the objective of a proper evaluation process is to mitigate risk and maximize the value to the organization. This articles discusses the key factors for consideration in suppliers selection.
Table of Contents
Supplier Financial Stability
Establishing a long-term relationship with the supplier relies on financial stability, before entering into a supplier relationship, the supplier’s financial status should be cautiously assessed. It is an important part of the financial evaluation as this might potentially affect its capability to support the customer. If a supplier’s financial status is not carefully assessed, the customer’s organisation will be at risk from delays, damage to the reputation, loss of profit and time wasted.
Financial statement analysis performs a part in the financial evaluation. In the financial statement, the information includes the management, experience and facilities of a prospective supplier. The purchasing officer can retrieve reports of a supplier’s financial statement, and the policy of pricing by implementing the analysis tools of ratio to the supplier classified balance sheet and income statements. Additionally, a supplier with a good financial status usually can provide a better rate of supplying goods. The purchasing officer can negotiate for good quality material at a lower price, exclusive material or product.
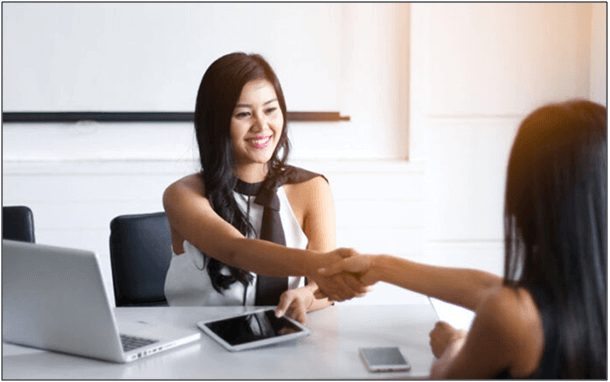
Supplier Quality Manual
Supplier quality is defined as the capability of a supplier to produce goods or services that fulfil customers’ requirements. It is the assurance of reducing risk, complying with regulations, improve the reliability of their products or services and determine their organizational process. A supplier’s service or quality must be in line with pre-established requirements. This is usually achieved through the proper implementation of supplier quality management systems. This allows companies to monitor supply chains, audit materials, conduct inspections and services regularly.
The supplier should monitor supply chains to ensure quality standards to achieve a proactive and collaborative approach. One way to ascertain a supplier’s quality is to engage a cross-functional team of representatives from different departments of the company. Those appointed representatives such as purchasing, quality control, engineering and production team will incorporate their technical knowledge or applications of the product documented in the supplier quality manual.
Considerations for Quality, Price and Delivery
Quality is one of the major considerations of procurement during supplier selection. The specified requirement is needed to produce a good quality of the final products. Achieving a good quality product, the whole operation requires labour, material and equipment. If the quality does not meet the requirements, it will affect the result of the finishing products. The supplier’s delivery reliability is also part of the consideration. For instance, should the supplier is not able to fulfil the quoted delivery time, the interruption will occur during production due to a shortage of material. In addition, when placing an order with a supplier, delivery time should be fast, simple and efficient.
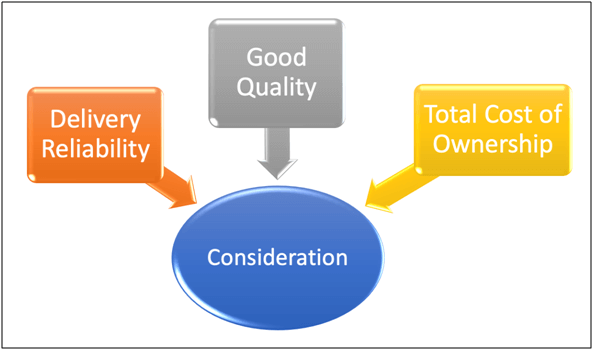
Purchasing in lesser quantity volume to meet current customer demand, allowing the supplier to expedite to meet customer timeframe or ordering less frequently to minimize inventory costs. The total cost of ownership is used to determine the total cost of procuring goods or services, evaluating the costs that are not reflected in upfront pricing. The hidden cost of the total cost of ownership including of the unit price of material, terms of payment, setup cost, holding cost, inventory carrying cost, maintenance cost and other qualitative costs that might not be easily measured.
Supplier Operational and Technical Capability
Operational capacity is one of the main considerations when selecting a supplier. Ensuring that suppliers can schedule the orders by monitor the ongoing production of the operations. For example, If a supplier has difficulties when scheduling due to capacity constraints and clashes with other jobs, they will not be able to comply with customer requirements. The whole process of operational capacity analysis is to recognize the available capacity for the organization which consist of available inventory holding capacity, labour capacity and machinery capacity. Other important key factors when evaluating supplier is their technology and technical capability. To achieve higher efficiency in an organization, implementation of the related technical function is important, which involve the capability to execute new product development, procedure and technological advancement. The prospective supplier must have all the required equipment, tools and ability to meet the requirements. Evaluating supplier technical capability is based on standards for compliance, invention, innovation, technical equipment and scientific capabilities. Purchasing officers can also asses through documented past performance records and active participation in industry events.
Supplier Prequalification
Supplier prequalification is a process of pre-auditing with a pre-determination set of criteria. The term for Prequalification is used in procurement and supply chain management. This is to ensure that suppliers have the standard capacity and capability to supply goods or services before an invitation to bid for a specific project or request. If a supplier has accomplished the prequalification criteria, they are generally kept on a database that is supported by the procurement organization. A prequalified status doesn’t mean a supplier has secured the contract.
When the offers submitted by prequalified suppliers arise, the purchasing officer is required to evaluate the offer progressively. A good prequalification system can help to reduce the purchasing process and cost of tendering for both client and supplier, as well as mitigate the risk of contract failure, for example, substandard or non-compliant suppliers that have already been disqualified or barred from entry.
The full content is only visible to SIPMM members
Already a member? Please Login to continue reading.
References
Chris Feldsine. (2021) “5 Key Factors to Consider When Conducting a Supplier Evaluation”. Retrieved from: https://www.thomasnet.com/articles/procurement/conducting-a-supplier-evaluation/ accessed on 16/9/2021.
Coleman Sr., Lance B (2016) “Beyond Tried and True”. Retrieved from: https://asq.org/quality-resources/supplier-quality, accessed on 16/9/2021.
Jakob Eisele, (2021). “The Fundamentals of Vendor Prequalification: Definition, Process & Enablers”. Retrieved from https://procurementandsupply.com/2021/02/the-fundamentals-of-vendor-prequalification-definition-process-enablers/, accessed on 16/9/2021.
Jason Goh Yeow Loong, PDPM (2017) “Five Effective Methods for Selecting Suppliers in the Oil and Gas Industry”. Retrieved from SIPMM:
https://publication.sipmm.edu.sg/five-effective-methods-selecting-suppliers-oil-gas-industry/, accessed on 16/9/2021.
Linda Zhang, DPSM (2020). “Essential Factors for Successful Supplier Selection”. Retrieved from SIPMM: https://publication.sipmm.edu.sg/essential-factors-successful-supplier-selection/, accessed on 16/9/2021.
Ng Shi Yun, PDPM (2020). “5 Key Criteria for Supplier Evaluation in the Construction Sector”. Retrieved from SIPMM:https://publication.sipmm.edu.sg/5-key-criteria-supplier-evaluation-construction-sector/, accessed on 16/9/2021.
Precoro (2019). “Four Basic Stages of Supplier Selection”. Retrieved from https://precoro.com/blog/four-basic-stages-of-supplier-selection/, accessed on 16/09/2021.
Wawasan Open University (2009). “Supplier Selection and Evaluation”. Retrieved from https://procurementmanagement.pressbooks.com/chapter/supplier-selection-and-evaluation/, accessed on 16/09/2021.