Key performance indicators (KPIs) are frequently used in general business to evaluate the success of everything from a specific department to an entire enterprise. KPIs work with the raw data of the industry to evaluate how the industry performs. It helps unleash the hidden patterns that help the industries analyze the bottlenecks, which in turn, compels the industries to take preventive measures against such problems. Also, it helps increase the employees’ productivity and the overall industry performance because it helps them assess their current state.
The Logistics industry makes use of KPIs to make note of how poorly or how well their industry is performing in the business market. It also helps them figure out where they stand in the market. The logistics industry is responsible for the handling of products or goods in a manner that greatly satisfies customers. It is a major fragment of supply chain management.
Table of Contents
Order Accuracy
Monitors the degree of incidents from the placement of the order to the delivery of a shipment. Ideal for any freight forwarder looking to identify patterns and continuously correct errors in order to make transportation safer. Order accuracy refers to how accurately orders could be filled in a given time slot. These orders are that processed right on time, shipped and delivered without any incidents on its way.
The shipping times, as well as the delivery time, are both respected, the order is not a wrong one and the goods are not damaged. It is quite doable for the logistics industry to fulfill a large number of orders within a given slot of time but what is desirable by the managers is how well and accurately could the logistics industry get these orders filled. Hence, measuring this KPI is very important for the logistics industry to drive effective and profitable results.
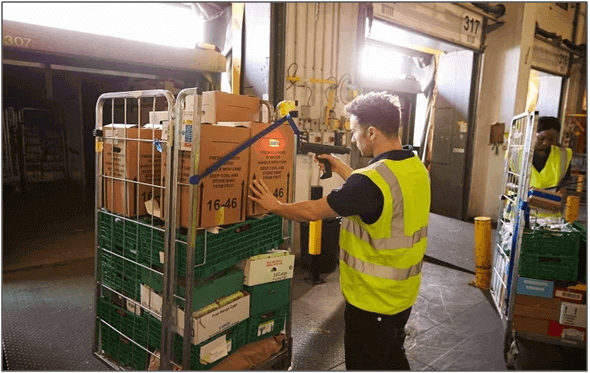
On Time Delivery
This is one of the important KPIs to gauge for the logistics industry. It is vital for the supply chain team to produce their goods right on time to the clients or consumers to avoid the load of fees related issues. By tracking the on-time delivery of the goods, logistics industry helps the consumers to consider the industry as reliable which is always good for the logistics industry. This helps enhance the performance of the logistics industry by a great amount.
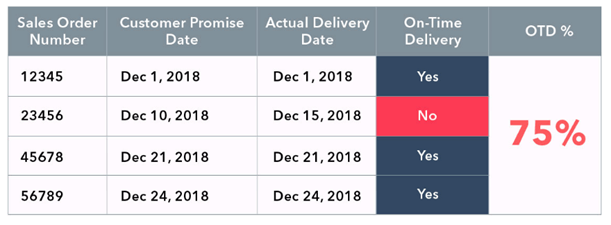
Inventory Accuracy
Inventory Accuracy is one of the important logistics KPI that can make or break your warehouse. Indeed, having a certain record of all your goods in your database that doesn’t match the actual physical inventory can harm your business considerably. If your inventory is inaccurate, that can lead to unexpected backorders but also unsatisfied customers and more generally as well as more higher in overall costs. A regular inventory checking the existing discrepancies with your electronic inventory record ensures that bookkeeping practices are in order and that your business is reliable, avoiding phantom inventory nightmares. This ratio will also help you spot issues related to receiving, shipping, or accounting.
One solution for inaccurate inventory is choosing a system that uses barcodes to track inventory. Some warehouses find that barcode systems integrate with their current warehouse management systems (WMS). These systems improve inventory control by providing a framework for managing inventory, supplies, and other warehouse materials.
Additionally, some WMS have capabilities for tracking shipments, managing purchase orders, and monitoring stock and inventory levels.
Inventory Turnover
Having a high inventory turnover is good for your warehouse. Narrowing down inventory turnover to a KPI that gives you visibility into your inventory rate is useful because it will help you gauge buying practices and product demand. Your warehouse management system (WMS) may provide a solution for gaining visibility into your inventory turnover and enabling forecasting to keep your inventory moving. Keep in mind that inventory turnover measures the number of times per year your warehouse goes through its entire inventory. You should compare this rate with industry averages to see how your warehouse is performing.
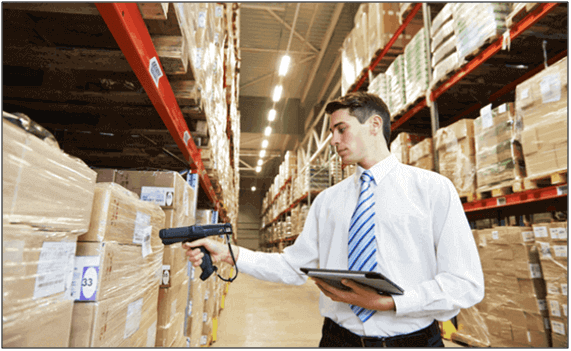
Transportation Cost
Measures all costs related to each logistics operation developed by your company, from order placement to final delivery. This KPI can be helpful for forwarders to know the average spent on each shipment and send accurate quotations to their customers/partners. It will break down all the costs related to this logistics KPI according to distinct categories: the order processing, the administrative, the inventory carrying, the warehousing and finally the actual transportation costs. After calculating all these, you can evaluate the percentage each stage of the process represents and see if that is excessive or in the norms. You can also calculate the transportation costs relative to a product and see how much one item costs compared to how much revenue it brings you.
Warehousing Cost
It is also ideal for the freight forwarders that offer warehousing services, this KPI monitors the expenses involved in the management of your logistics company’s warehouse facilities. Warehousing is the management of space and time.
The warehousing costs refer to the money allocated to the goods moved into or outside the warehouse. These expenses cover equipment and energy costs like ordering, storing and loading the goods, as well as more human costs like labor, shipment, or delivery. The warehousing costs are a component of another logistics KPI, the total transportation costs. Measuring them is not an easy task, but once it is done it will facilitate your overall management and add a lot of value, something that senior management or investors will appreciate. The table below shows the KPIs that can be used internally, for suppliers, as well as for customers.
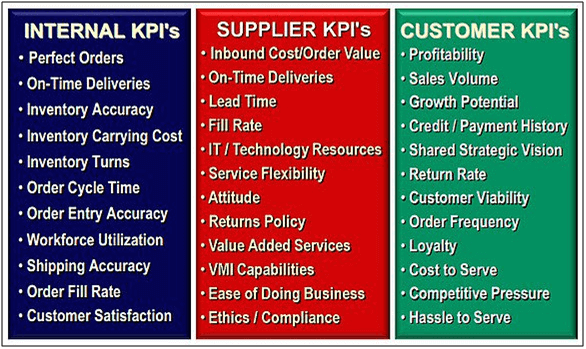
What Makes An Effective KPI
What makes Key Performance Indicators so effective? Following are 5 factors that can be the difference between mediocre data recording and a truly effective business improvement exercise:
1. Keep Aligned.
KPIs should track the performance of a specific business objective to help achieve the larger goals of the company. Being closely aligned to key measurements will ultimately help to focus on influencing factors to reach these goals.
2. Less is more.
In a world full of data is far too easy to track too much and too often. It’s a common mistake to measure everything connected to the business. Starting with a small number of specific KPIs will not only be easier to implement but will help with the adoption of KPIs with the organization.
3. Actionable and accountable.
KPIs without clear and relevant targets are simply measurements that are limited in how you can influence their performance. Short and long-term targets should be set for KPIs, along with owners who are responsible and able to influence business processes.
4. Attainable.
Can we realistically achieve this objective? Do we have the capacity to change or amend processes that will influence the performance? KPIs should be realistic and proportionate to the resource of a business. Nothing will stop a well-intentioned performance improvement process that an over-ambitious and unattainable objective.
5. Review and tweak.
As with any business process, KPIs also need timely scrutiny or maintenance to keep them performing at their best. Setting regular review periods will keep them relevant and providing optimum benefit.
Conclusion
There is no one-size-fits-all formula for every company. Goals, as well as KPIs, are most usual custom. Several studies have been carried out on logistics performance and the results are that there is no single KPI that will cover every logistics department. However common key performance indicator that is found to be common in evaluating performance. Namely, cost-saving, services quality, delivery KPI and inventory control. In addition, the importance of these KPIs to the overall effectiveness of a logistics department will change over time and therefore need to be assessed and modified periodically.
References
Ben Wee Pang Aik, DLSM. (2018). “Key Performance Metrics Effective Warehousing Customer Services”. Retrieved from SIPMM: https://publication.sipmm.edu.sg/key-performance-metrics-effective-warehousing-customer-service/, accessed on 12/06/2018.
Data Pine. (2017). “Logistics Key Performance Indicators And Metrics”. Retrieved from https://www.datapine.com/kpi-examples-and-templates/logistics#warehousing-costs, accessed on 12/06/2018.
Jeff Tan Ai Keong, DLSM. (2018). “Key Performance Indicators Minimizing Warehouse Risks”. Retrieved from SIPMM: https://publication.sipmm.edu.sg/key-performance-indicators-minimising-warehouse-risks/, accessed on 12/06/2018.
Think Layer. (2017). “KPI For Logistics Industry”. Retrieved from https://thinklayer.com/kpi-logistics-industry/, accessed on 12/06/2018.
Weber Logistics. (2015). “6 Essential Logistics Key Performance Indicator(KPIs)”. Retrieved from https://www.weberlogistics.com/blog/california-logistics-blog/key-performance-indicator, accessed on 12/06/2018.