Supplier quality is the ability of a supplier to deliver goods or services that will meet and satisfy customers’ requirements. The quality performance of suppliers will affect largely and directly to the quality performance of an organization. Ineffective procurement techniques for supplier quality can be catastrophic to business growth. It will negatively impact the reputation of organization, create legal and financial impacts that cannot be fully passed to the supply partners at fault. Thus, most of the organizations emphasizes on effectively managing and improving supplier quality.
Supplier quality is assured by having clear requirements on all aspects of product quality, logistics, legal, environmental requirements and quality requirements. To manage and improve supplier quality, organizations shall apply the procurement techniques including measuring and tracking of the cost of quality (COQ), implementing cost recovery process, alignment of supplier risk management with quality audits, supplier rationalization, standardization of supplier quality and performance metrics as well as application of collaborative approach to corrective action.
Table of Contents
Measuring and Tracking the Cost of Quality (COQ)
Cost of quality (COQ) is defined as the costs related with detecting, preventing, and remediating product quality issues. Measures of quality cost for suppliers are divided into four distinct categories including internal failure costs, external failure costs, appraisal costs and prevention costs.
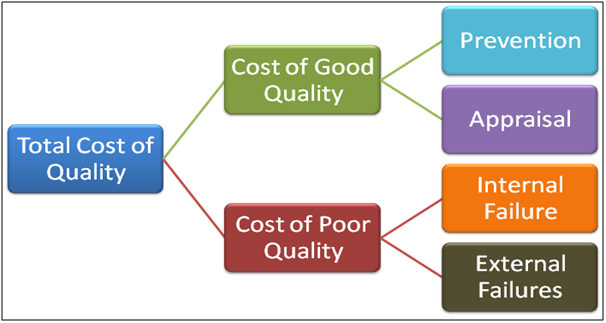
Cost of Poor Quality (COPQ) includes internal failure costs and external failure costs. Internal failures costs are incurred to rectify defects found before the product is transferred to the customers. Examples of internal failure costs are costs for re-testing, rework, expediting shipping and failure analysis. External failures costs are incurred to rectify defects that fail to meet designed quality standards are not detected until discovered by customers. Factors to consider for external failure costs are customer complaints, recalls, penalties and reputational damage.
Cost of Good Quality (COGQ) includes prevention costs and appraisal costs. Prevention costs are costs incurred to avoid or keep quality issue to a minimum level. A quality management system is designed, implemented and maintained for the prevention of poor quality. Appraisal Costs are costs incurred from activities such as quality audits, inspection of incoming products and supplier performance ratings to maintain acceptable product quality levels and ensure conformance to specifications with the evaluation of purchased products and services.
Although the fault may lie with a supplier, the organization often bears the COPQ when a product quality issue arises. When organization fails to measure and track the COPQ, it can expend large sums of revenue without knowing where or how to recover these costs. The COPQ metrics can help in identifying problems area for cost savings and calculating supplier chargebacks accurately for recovering costs. Also, organization can focus on measuring and tracking the COGQ. Organization that invests more on good quality leads to a lower cost of poor quality and fewer supplier quality issues.
Implementing Cost Recovery Process
A cost recovery system is an operative technique to introduce business accountability and discipline into the supply chain. The supplier is charged for any additional costs incurred as a result of the supplier’s failure to comply with the specified conditions such as late deliveries, non-conforming components and damaged materials during transportation. Additional costs may include premium freight, sorting cost, rework cost, production line down cost, overtime cost, customer charge-backs and so on.
A cost recovery system allows organization to recover the cost of poor quality and encourage suppliers to focus on the quality improvement. When cost recovery system is implemented, suppliers tend to react and response quickly to the quality issue and non-conformance. In addition, an effective cost recovery system can help in keeping track of all metrics related to performance of suppliers. Organization can implement and practice an end-to-end cost recovery process with following steps.
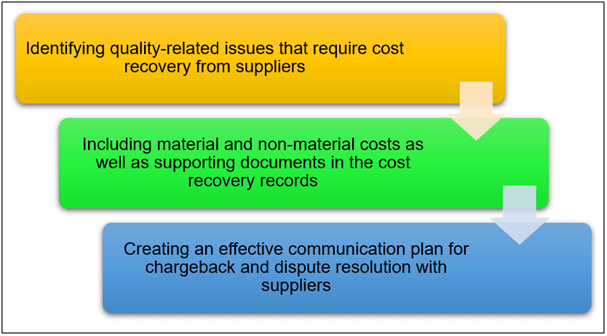
Alignment of Supplier Risk Management (SRM) with Quality Audits
Supplier quality audits play a crucial role in ensuring products of suppliers meet established quality specifications and drives continuous improvement during audit process. Instead of auditing all suppliers at once, it is much more well-organized to align supplier risk management (SRM) with quality audits.
Suppliers can be assessed and classified based on risk, so organization can prioritize audit activities accordingly to identify quality issues and opportunities for improvement and optimization. High risk suppliers, which are critical to availability and quality of products, will require more frequent audits. In contrast, lower risk suppliers that have no direct product impact only require fewer audits. After assessment and classification based on risk, audit can be planned and scheduled to identify non-conformance and create positive experience for suppliers to understand the importance of audit. The audit frequency can be varied based on the changing risk profile of the supplier.
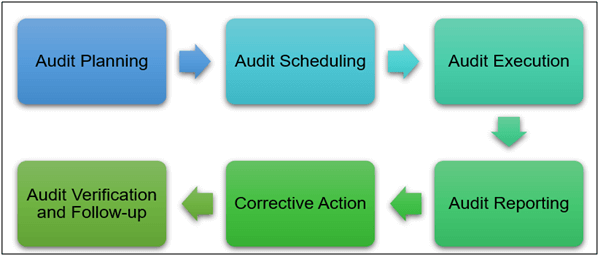
Supplier Rationalization
Supplier rationalization is the process of determining the ideal number of suppliers with right capabilities and refining the supplier base for effectiveness of supply chain. This involves reducing and expanding number of suppliers to support the changes of organization in requirements, objectives and priorities.
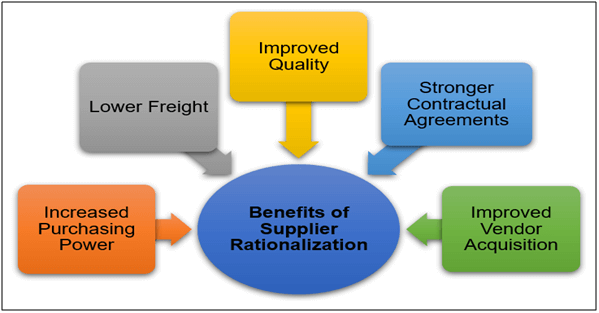
In common, the more complex the supply chain, the more challenging and costly for organization to maintain and manage supplier quality. Supplier rationalization brings greater control and efficiency to improve supplier quality. Supplier rationalization can utilize hurdle method and set higher standards for quality requirements to eliminate potential suppliers that are ineligible for supply chain. In a meanwhile, organization cannot reply on sole source and should look for more sources as backups to avoid production disruption due to supplier quality issue. The expansion of right suppliers can raise the competition and increase the competences among suppliers.
The full content is only visible to SIPMM members
Already a member? Please Login to continue reading.
References
ASQ Quality Press (2020). “Supplier Quality”. Retrieved from https://asq.org/quality-resources/supplier-quality, accessed 13/06/2020.
Bragg, S. (2020). “Quality Costs”. Retrieved from https://www.accountingtools.com/articles/what-are-quality-costs.html, accessed 13/06/2020.
Earnest Lim Joon Kiong, DPSM. (2019). “Six Essential Strategies for Sustainable Procurement”. Retrieved from SIPMM: https://publication.sipmm.edu.sg/six-essential-strategies-sustainable-procurement/#Supplier_Optimization, accessed 15/06/2020.
Finn, T. (2017). “Supplier Rationalization — Revisited.” Retrieved from https://spendmatters.com/2017/11/08/supplier-rationalization-revisited, accessed 20/06/2020.
Metric Stream (2020). “Best Practices in Supplier Quality Management”. Retrieved from https://www.metricstream.com/insights/bestPractices_supqltymgmt.htm, accessed 13/06/2020.
Schade, M.B. (2020). “Supplier Quality Management Defined”. Retrieved from https://www.business-online-learning.com/supplier-quality-management-defined.html, accessed 13/06/2020.
Stoop, E. (2017). “Critical Strategies for Improving Supplier Quality Management”. Retrieved from https://www.ease.io/critical-strategies-for-improving-supplier-quality-management, accessed 13/06/2020.
Teddy Oh Sing Yie, DPSM. (2018). “Techniques for an Effective Global Sourcing Strategy”. Retrieved from SIPMM: https://publication.sipmm.edu.sg/techniques-effective-global-sourcing-strategy/, accessed 15/06/2020.
Teli, S.N., Majali, V.S., Bhushi, U.M. & Deshapande, A.S. (2012). “Knowledge based Supplier Quality Management System for Automobile Industry”, International Journal of Engineering Innovation & Research. Volume 1, Issue 4, ISSN: 2277-5668, accessed 13/06/2020.