The fast-moving consumer goods (FMCG) sector plays a significant role in the global economy, leading to its rapid growth. These products have varying shelf lives, packaging dimensions, storage requirements, legal regulations, and demand patterns. This diversity makes inventory management and warehousing challenging tasks for businesses. To keep up with the increasing demand for everyday products, sustainable storage solutions, and warehousing techniques are essential. Companies face challenges such as labor shortages and limited space, highlighting the importance of utilizing technology for process automation. This article explores the use of technology in FMCG warehousing as a means for businesses to optimize warehouse operations and meet customers’ needs efficiently.
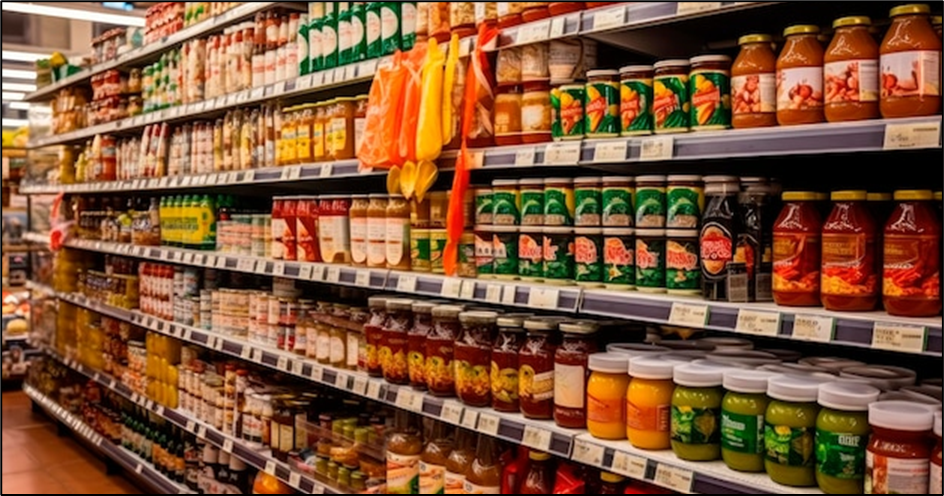
Image taken from https://www.pexels.com/search/supermarket/
Table of Contents
Warehouse Management System (WMS)
WMS assists businesses in managing and overseeing day-to-day warehouse operations, from the time goods arrive at the warehouse until they are delivered to clients. Order fulfillment is sped up, human error is decreased, and real-time inventory data is provided throughout the whole warehousing process by WMS. There are not many choices for WMS, whether it is a standalone or integrated system. The integrated WMS is connected to the current Enterprise Resource Planning (ERP) system, which oversees inventories, bills, and accounts. Through information sharing, both systems are linked to one another through this integration, improving workflow and visibility. A standalone WMS is confined to managing warehouse operations and may only include certain features that are relevant to warehouse operations.
Barcode Scanners and Radio-Frequency Identification (RFID)
Barcode and RFID scanning technologies are essential to modern warehousing and provide numerous benefits. A laser beam is used by a barcode scanner to read a barcode’s black and white lines. RFID uses radio waves to transmit information from RFID tags to the reader. Pickers can pick faster as the sensor uses the reflected light to form a signal, converts that signal into text, sending that text to the computer. Many businesses use barcode or RFID tags to easily gather and monitor goods movement. FMCG products contain barcodes and involve metal or liquid, employing RFID tags or other similar techniques is impractical, making the barcode method a superior option. Most tasks can employ a barcode scanner since barcodes are nearly universal.
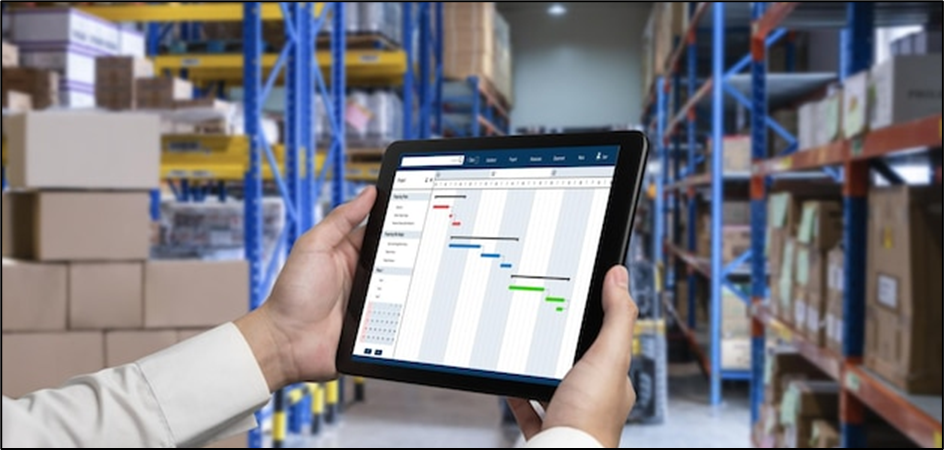
FEFO Inventory Control Technique
First Expire, First Out (FEFO) is an inventory management approach that involves selling things with the earliest expiration dates first. Stock availability is critical in the FMCG sector due to short shelf lives impacting product quality and customer satisfaction. FEFO helps ensure high-quality products are shipped and minimizes expired or obsolete stock in warehouses. This approach is crucial for FMCG warehouses with fast-moving products and high turnover rates. Success with FEFO requires a reliable inventory system for easy expiry tracking and stock allocation based on expiration dates during order fulfillment. The FEFO method facilitates high product movement and influx in the warehouse. Enhanced customer satisfaction is a result of delivering or selling goods that are in good condition and fresh.
Demand Forecasting
FMCGs are popular customer products that individuals need consistently. They typically have a high sales volume but a moderately low-profit margin. Turnover rates for products are high, and stockroom tasks from requesting to conveyance are happening at a quick speed. The warehousing business relies on understanding consumer interest and anticipating market trends and consumer behaviour. Request estimating includes the utilization of innovation and the examination of review information, for example, stock development, deals, market interest, and conceivable occasional examples. Exact estimating lessens the gamble of overloading, forestalls unavailable circumstances, and guarantees adequate stock to fulfill clients’ needs and fulfillment. Goods need to be assessed to ensure suppliers have enough time to prepare for the goods, taking into consideration the availability of warehouse capacity.
Buffer Stock Inventory Technique
Buffer inventory is extra stock held by companies to mitigate unexpected events like transportation delays or supply chain disruptions and meet customer demands. It acts as a cushion against stockouts and can be maintained at different supply chain stages. Benefits include protection against demand and supply fluctuations, improved customer satisfaction, revenue stability, and seizing opportunities for immediate product availability. Buffer inventory also helps companies respond quickly to demand surges and prevents revenue losses by ensuring uninterrupted operations during supply chain disruptions. Overall, maintaining buffer inventory is crucial for businesses to protect against uncertainties, stabilize revenue flow, and capitalize on opportunities for growth and customer retention.
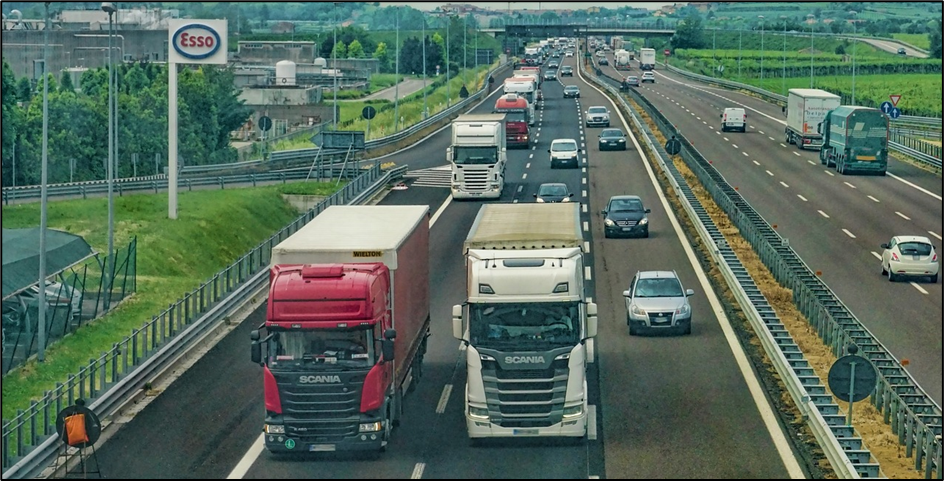
Image taken from https://pixabay.com/photos/highway-road-trucks-vehicles-3392100/
Transport Management System (TMS)
TMS is a strategic stage that assists organizations with overseeing operations-related issues, i.e., the development of actual products. It can deal with both the approaching and active stock, including load and route arranging. The system provides dashboards, announcements, and examination data regarding the transportation cycle. FMCG organizations utilize TMS for cost-effective and timely delivery. The WMS and TMS framework enables the system to efficiently distribute stock to the conveyance truck, reducing the need for physical sorting and burdening the network. The conveyance driver will then allude to their cell phone, continue with the conveyance for the afternoon, and accomplish streamlined directing. With this framework, the stockroom interaction is automated, diminishing human mistakes and the carbon footprint.
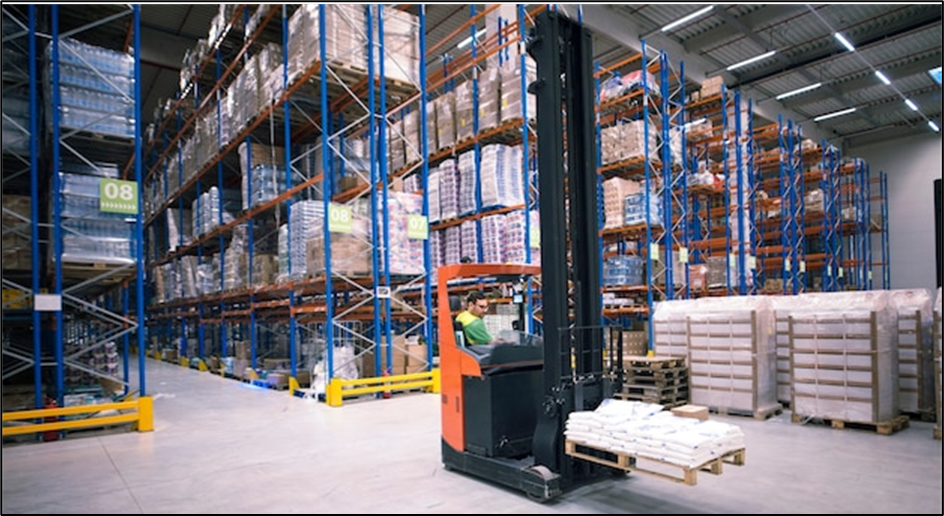
Image taken from https://www.freepik.com/free-photo/worker-operating-forklift-machine-relocating-goods-large-warehouse-center_11030561.htm
Good Warehouse Layout and Storage System
One significant procedure of productive practice for FMCG is to guarantee a very arranged distribution center design and capacity framework are carried out. Appropriate distribution center design reduces setup, picking, and transportation time. The distribution center should zero in on four significant cycles: inbound, outbound, stockpiling, and worth-added administration. Organizations need to adjust a practical stockpiling framework relying upon the activity and products the distribution center is taking care of. To accommodate high stock turnover rates and increase storage space in a distribution center, a combination of capacity frameworks may be beneficial. The use of a storage racking system is also an important consideration depending on the operation framework.
Inventory Cycle Counting
Stock cycle counting is utilized to count a limited quantity of your stock to guarantee your organization’s actual stock lines up with stock records. This strategy is to guarantee that your stock is exact and fully informed regarding insignificant errors by resetting any mistakes. There are a few strategies utilized for cycle counting, for example, ABC cycle counting, irregular example cycle counting, and control bunch cycle counting. ABC cycle counting technique is to count things with a higher worth more habitually than things with a lower value by utilizing the 80/20 rule. Irregular cycle counting is done when a few things are decided indiscriminately for counting; this happens when a stockroom has numerous comparable items. Then again, the control cycle counting procedure counts a little arrangement of things more than once inside a brief timeframe to track down any blunders. This technique is normally utilized related to other counting strategies to uncover any blunders that may be forgotten about.
Conclusion
In the fast-moving consumer goods (FMCG) industry, warehousing techniques are critical to the efficient receipt and delivery of products in the least amount of time. The FMCG industry requires items to be moved quickly, which accounts for the quick turnaround in warehousing. Achieving high-volume movement and full, on-time delivery of goods is crucial. Proper warehousing techniques are not implemented correctly, the company risks facing problems with picking efficiency and fulfillment rates. In addition, storage, stock tracking, out-of-stock, and overstock issues might arise as a result. There will be inefficiencies in the business, which will cause downtime and eventually impact profit margins. Customers’ confidence and contentment with the warehouse will be impacted, leading them to choose other options.
References
Andrew Tan Howe. (2018). Effective Inventory Management Practices for Fast Moving Consumer Goods (FMCG). Available at SIPMM: https://publication.sipmm.edu.sg/effective-inventory-management-practices-fast-moving-consumer-goods. (Accessed: 29 February 2024).
Bradyid. (2024). RDI vs. barcode for asset tracking. Retrieve from https://www.bradyid.com/intelligent-manufacturing/rfid-vs-barcode. (Accessed: 29 February 2024).
Foo Chuan Yang. (2022). Practical Techniques to Control Warehouse Inventory. SIPMM Publications. Available at SIPMM: https://publication.sipmm.edu.sg/practical-techniques-control-warehouse-inventory. (Accessed: 29 February 2024).
Schwarz, L. (2021). Inventory Cycle Counting 101: Best Practices & Benefit. Retrieved from https://www.netsuite.com.sg/portal/sg/resource/articles/inventory-management/using-inventory-control-software-for-cycle-counting.shtml. (Accessed: 29 February 2024).
SAP. (2024). What is a warehouse management system(WMS). Retrieved from https://www.sap.com/sea/products/scm/extended-warehouse-management/what-is-a-wms.html( Accessed: 29 February 2024).
Sky Tan Poh Suh. (2022). Important Techniques for Effective Warehouse Practices. SIPMM Publications. Available at SIPMM:https://publication.sipmm.edu.sg/important-techniques-effective-warehouse-practices. (Accessed: 29 February 2024).
Venus Chong Wei Feng. (2022). Essential Techniques for Warehouse Efficiency. SIPMM Publications. Available at SIPMM: https://publication.sipmm.edu.sg/essential-techniques-warehouse-efficiency( Accessed: 29 February 2024).