Fundamentally, setting up and operating a warehouse might not be a difficult task but operate the warehouse at an optimal level of efficiency and effectiveness will not be as simple as it may be. The challenges that pose to numerous organizations are to display the right attitude by regularly seeking continual improvements that are known as “Kaizen” (change for the better).
In order to measure the efficiency and effectiveness levels of the warehouse management, Key Performance Indicator (KPIs) system is a tool to be employed. By using the existing collected data as the yardstick against the further collected data to determine the success made at each measured operational area. Therefore, to definitively, the key performance indicators for warehouse performance measurement must be objectively driven and aligned back to the business objective.
Table of Contents
Key Performance Indictors (KPIs)
Key Performance Indicator for warehousing is a tool used to measure the goals set by the company and its achievement of warehouse management. The goal setting at the KPIs would require the past evaluated performance of the warehouse performance.
The focus of the goal setting at the KPIs can be to seek optimization over the inter-organizational achievement by comparing the gap between the internal operations and the perception of warehouse management. Another focus can be at the strategic level for performance evaluation or at the highest operational level for planning and control.
The widely used performance goal setting for KPIs is S.M.A.R.T as it brings structure and trackability into the goals and objectives. The acronym of S.M.A.R.T stands for Specific, Measurable, Attainable, Relevant, and Timely. This is a push method that provides a sense of direction to reach out towards the target goal.
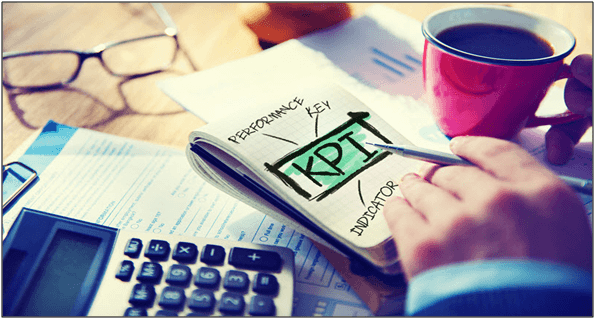
Receiving and Put-Away KPIs
Receiving a stock into the warehouse is a pivotal operation as it involves the cost of labour, productivity, and timeliness. Tracking of incoming freight will be made based on the volume put away per employee per hour. The warehouse manager should also track the item, costs, accuracy and the timeliness for the inbound shipment together with the labour cost upon receiving. These arecheck and balance KPIs to provide a clearer view of the potential inefficiencies in the process flow to streamline the processors.
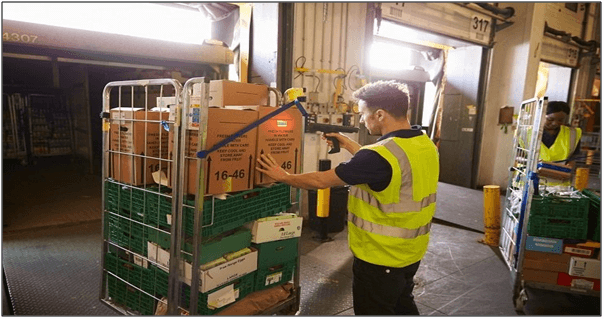
Storage KPIs
This is one of the fundamental KPIs when evaluating the efficiency of the storage space and inventory cost. These are direct measurements of each other, and an impact made if both are not well-balanced. The formula of the dependent values in these KPIs are taken from Inventory Turnover and the Carrying Cost of Inventory.
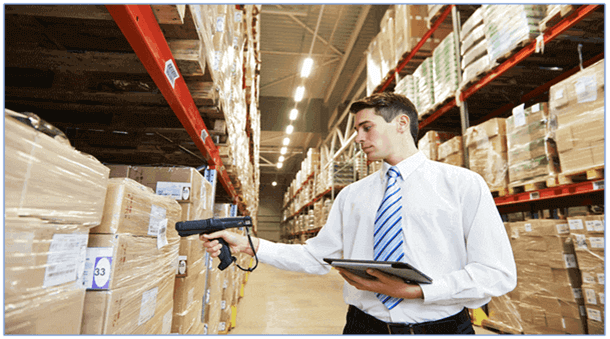
KPIs for Picking, Packing and Shipping
These KPIs have a direct impact over the lead time. It included the quantity of items picked, the value of the items, labour costs and the cost of packaging. There is also an impact on customer satisfaction by decreasing the order return by picking the right order. Shipping KPIs are like picking and packing KPIs.
The focal point is on the total number of items shipped versus the projected number of items shipped. For example, if 200 items are shipped, and there are 250 items scheduled to be the shipped, this may lead to delays and possible problems within the warehouses, and this is a deficit KPI.
Shipping KPIs are computed by dividing the total number of shipped orders by the number of planned shipments. The measurement is subject to results as a higher result shows an increase in operations. If there is a decrease in the result, it shows signs of problems and decreased productivity.
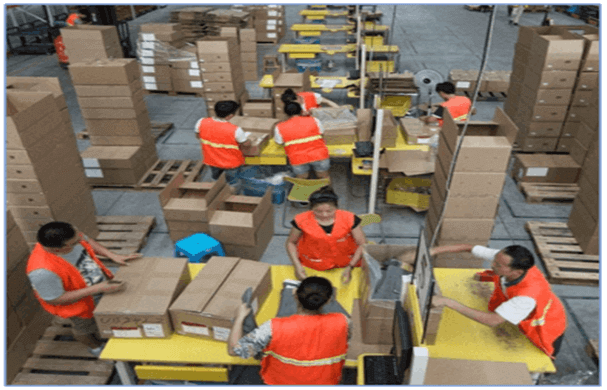
Reverse Logistics KPIs
Reverse logistics KPIs are circling the recycled products and return products coming back from consumers. Although there are several reverse KPIs exist, however, the most important one is the rate of return. It is based on dividing the number of units returned by the total number of units sold. As a result, increases, it alludes to a possible problem with a product.
Inventory Accuracy
The inventory accuracy is a measurement of the database inventory versus actual inventory. The calculation is by dividing the database inventory count by physical inventory count. The result will be shown as one if the count is accurate and identical. If capturing inventory data is inaccurate, there will incur unnecessarily high costs and a decrease in customer satisfaction levels.
The full content is only visible to SIPMM members
Already a member? Please Login to continue reading.
References
Hector Sunol. (2020). “Top 24 Warehouse KPIs You Must Be Tracking”. Retrieved from: https://articles.cyzerg.com/warehouse-kpi-tracking-top-24#, accessed on 14/9/2020.
Jeff Tan Ai Keong, DLSM. (2018). “Key Performance Indicators Minimizing Warehouse Risks”. Retrieved from SIPMM: https://publication.sipmm.edu.sg/key-performance-indicators-minimising-warehouse-risks/, accessed on 14/9/2020.
Prakaash Gunasengaran, DLSM. (2017). “Technique to Improve the Warehouse Order Picking Process”. Retrieved from SIPMM: https://publication.sipmm.edu.sg/techniques-to-improve-the-warehouse-order-picking process/, accessed 14/9/2020.
Sam Leong Kim Foong, DLSM. (2019). “Key Performance Indicators (KPIs) for the Logistics Sector”. Retrieved from SIPMM: https://publication.sipmm.edu.sg/key-performance-indicators-kpis-logistics-sector, accessed on 14/9/2020.
Voodoo robotics. (2016). How to Measure Warehouse Efficiency: Detailed KPIs. Retrieved from https://info.voodoorobotics.com/blog/how-to-measure-warehouse-efficiency-detailed-kpis-to-watch/, accessed on 14/9/2020.