The rapid proliferation of digital technology has led to ongoing improvements in the automation of equipment and practices around the world. Deployment of modern smart technology that integrates machine-to-machine communication and the internet of things (IOT) which diagnoses issues without the need for human intervention is getting prevalent. One key trend we have noticed in recent years is the application of an Automated Storage and Retrieval Systems (ASRS), which are computer-controlled systems that automatically place and retrieve loads from set storage locations in a facility with accuracy, precision, and speed.
This alleviates constraints such as manpower deficiency, human errors, and space capacity. This article discusses the key factors that lead to a successful ASRS implementation.
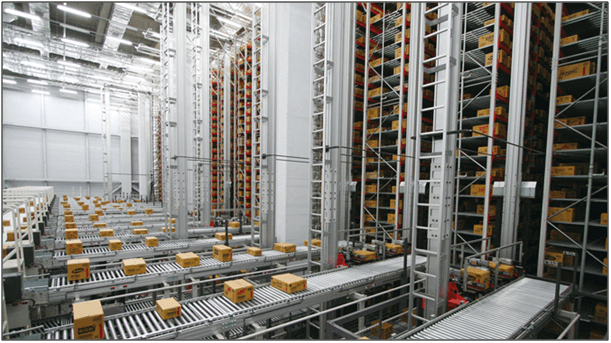
Table of Contents
Choosing the Right ASRS
Choosing the right ASRS system is critical to the business. The type of ASRS model chosen depends on the nature of the business, the type of customers or products and the company’s long-term goals in business growth. The model of the ASRS varies by Shelf-based picking, Bin-based picking, or Robotic picking. Selecting the right ASRS model and type will have better returns on investment (ROI) in the long run. It is extremely important to retrieve physical data that consists of both historical and required projections, including inventory levels and SKU velocity classification.
All these data collected can be modelled via simulations to predict the required size and throughput capabilities of the system in the future. The right model must ensure that system configurations such as electrical, software setup, physical and output points of the system can function and keep up with the high demand of all storage and retrieval requests. This helps to determine how the system will impact the entire fulfillment process, including upstream manufacturing processes and downstream shipping operations.
Other considerations are to pre-determine the use of materials such as pallets, slip sheets, totes, carrier boards etc. on whether they are captive in the system or will be induced at some other point in the process. All the above is not possible without the engagement of the internal stakeholders to ensure the required information is successfully delivered.
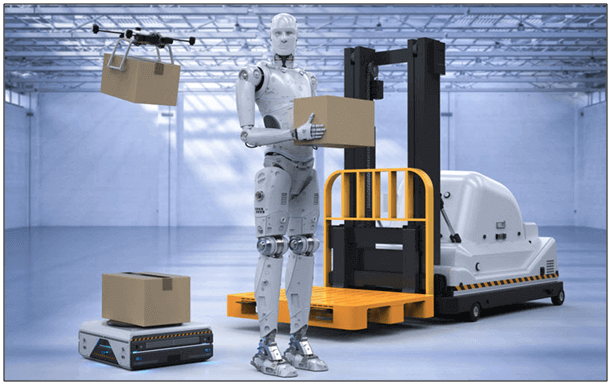
Facility Evaluation and Risk Assessment
To construct a new ASRS system or facility, it is critical to have the knowledge and experience with various regulations influencing the project. This can be done by engaging a third-party consultancy firm who possessed relevant experience consulting the relevant authorities to ensure that the facility is suitable or meets the local regulations requirements before proceeding to kick-off the project. Risk assessments are usually conducted to find out the risk classifications of building works, to establish the risk level of the building project and to provide necessary supervision corresponding to the risk level. All potential risk metrics can be incorporated into the business’s risk assessment index. This provides better awareness and preparedness to existing employees in the event of an unforeseen situation.
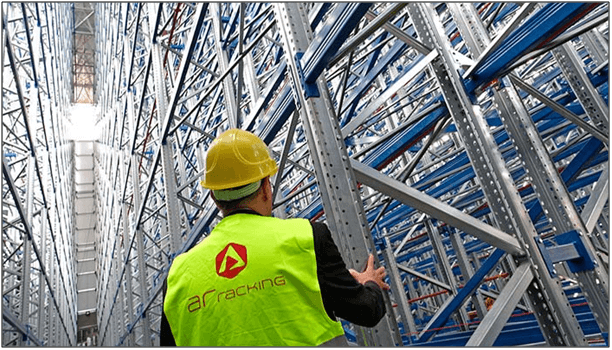
Selecting the Right Supplier
This is one of the most important business decisions because it will have a direct impact on the success of the project. A good supplier can lead to an effective configuration of the ASRS, which results in a successful implementation. It is necessary to weigh all options, including costs, quality, terms and conditionsbefore deciding which supplier is the best. Regular communication is essential to ensure full clarify on the details stated in the contract agreement.
One method of supplier evaluation is to get references from existing or past clients who have worked with them to get an honest account of their good and bad points. The construction of an ASRS system is a huge investment, hence the reliability and past experiences is extremely crucial. Questions asked by the supplier can be used to gauge whether the culture or expectations are similar and will give the business an idea whether the relationship will work between both parties.
The presence of the supplier in preferred locations will determine how the support will come by especially if the business is looking to expand internationally. In this case, an international supplier might be the preferred choice since they have the overseas expertise on business regulations, which can assist to ship products more efficiently.
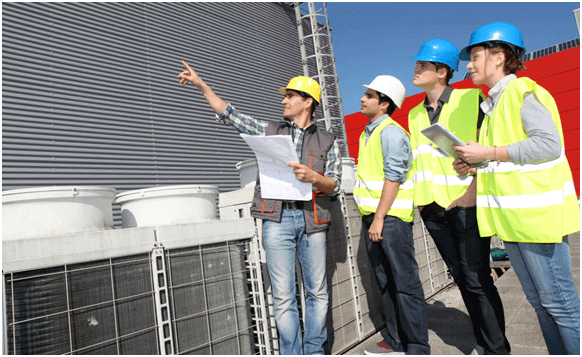
Integration of Digital Technologies
The successful integration of Warehouse Management Software (WMS) and IOT helps in efficient planning and better ASRS execution. This allows visibility on real-time data in tracking movements of goods, shipments, orders, deliveries, and receipts with the synchronization of all information into one network.
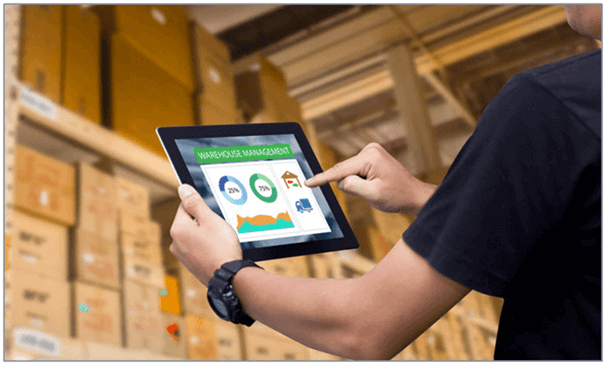
Having an ASRS helps to enhance the level of accountability and security, thus reducing the amount of goods that must be scrapped due to damage. Processes such as First-In-First-Out (FIFO), Last-In-First-Out (LIFO) picking principles can also be configured for better inventory turn in the long run.
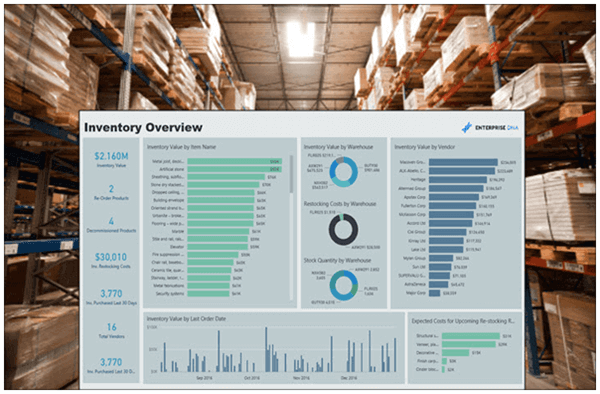
Planning and Designing the ASRS
The structural design and capacity utilization are critical during the early planning stages for ASRS. A list of all possible activities that will take place in the ASRS system should be provided so that it can be included in the design of the facility. The company needs to list down the products and their characteristics to ensure thorough coverage of the business’s requirements. Examples are product types, shelf life, temperature storage conditions and control, and whether products should be stored individually, on cartons, pallets, or trays.
When planning out the design layout for ASRS, we should be able to locate all the activities happening within the ASRS facility so that the flow of the operations is smooth with minimum amount of movement and disruption. There should be an alternative way for contingency accessibility in case the technology breaks down that requires immediate troubleshooting. Designing it efficiently will allow for flexibility and scalability in the long run. The speed of the product movement will determine the volume that moves through the ASRS every day. Availability of throughput data will help in terms of the design outcome and future forecast.
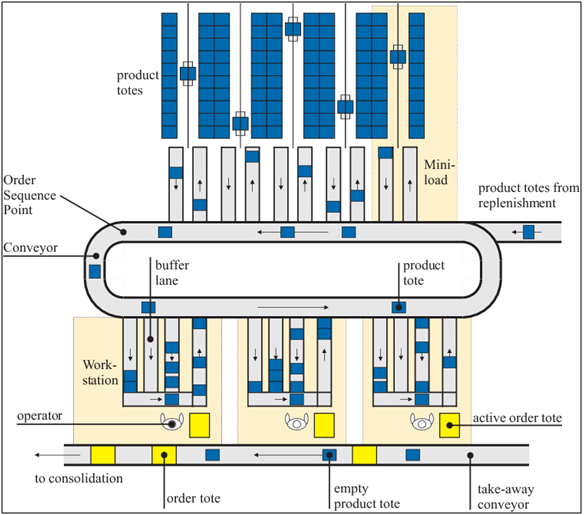
Factory Acceptance Tests (FAT)
This is usually conducted to assess any discrepancies and non-conformities. Deviations observed during testing are documented in a report and corrected prior to receiving Temporary Occupation Permit (TOP). Both parties can be reassured that the equipment or facility meets all the contractual specifications. This keeps the project on track and within budget if the issues are rectified while the system is under possession of the manufacturer.
The tests include attaining individual proof of functionality, quality, and integrity with comprehensive checking process by verifying all important documents, such as manuals, instructions, plans, drawings, piping, and instrumentation diagrams (P&IDs). This ensures that the equipment or facility performs as expected under the testable range of likely conditions, including mishandling and error.
The full content is only visible to SIPMM members
Already a member? Please Login to continue reading.
References
Building and Construction Authority. (2019). “Framework for Risk-based Inspection”. Retrieved from https://www1.bca.gov.sg/regulatory-info/building-control/construction/framework-for-risk-based-inspection, accessed 28/03/2021.
CareLabs. (2021).“What is Factory Acceptance Testing, and how is FAT Done”. Retrieved from https://carelabz.com/what-factory-acceptance-testing-how-fat-done/, accessed 28/03/2021.
Jon Goh Woon Keong, DLSM. (2019). “Nine Technologies to Boost Warehouse Productivity”. Retrieved from SIPMM: https://publication.sipmm.edu.sg/nine-technologies-boost-warehouse-productivity/, accessed on 28/03/2021.
Keane Ng, DPSM. (2020). “Key Considerations for Digital Warehousing”. Retrieved from SIPMM: https://publication.sipmm.edu.sg/key-considerations-for-digital-warehousing/, accessed on 28/03/2021.
Khaos Marketing. (2020). “5 Things to Consider When Choosing a New Supplier”. Retrieved from https://www.khaoscontrol.com/business-tips/5-things-to-consider-when-choosing-a-new-supplier/, accessed 28/03/2021.
Mohamed Farouk Bin Jailabdeen, ADLSM. (2021). “Digital Technologies for a Smart Warehouse”. Retrieved from SIPMM: https://publication.sipmm.edu.sg/digital-technologies-smart-warehouse/, accessed on 28/03/2021.
Rob O’ Byrne. (2020). “Key Factors to consider when planning and designing warehouses”. Retrieved from https://trans.info/en/key-factors-to-consider-when-planning-and-designing-warehouses-172055, accessed 28/03/2021.
Surbhi Aggarwal, (2020). “Pre-requisites to be done before implementing an ASRS system”. Retrieved from https://addverb.com/implementing-an-asrs-system/, accessed 28/03/2021.