Warehousing and transportation have never been more complicated. The digitalization of warehouses, rising customer expectations for delivery and customer service, and market competition put pressure on overall operations. This article discusses the common warehousing mistakes made by many organizations and how to avoid them to make the business better.
Table of Contents
Holding Excess Inventory
In spite of numerous researches and techniques in the warehousing field, excessive inventory is still one of the most common warehousing errors in global supply chains. Wholesalers especially seem to find it easy to fall into this trap, usually because of buying large quantities of individual products to take advantage of volume discounts.
Lowering inventory levels as much as possible can make your supply chain more streamlined and reduce the consumption of funds in inventory. Therefore, when there is an “irresistible discount”, it is necessary to try to arrange with the supplier to deliver large orders in small batches when needed.
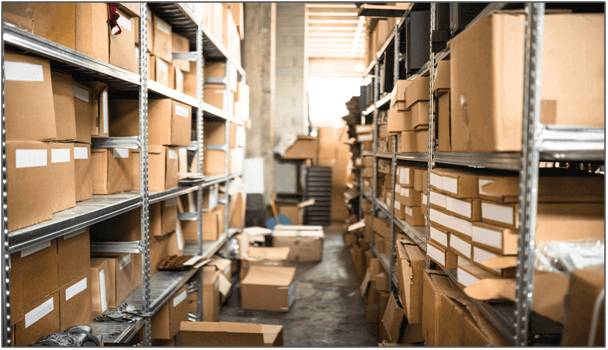
Using Outdated Technology
Digital technologies have greatly promoted logistics and supply management. Innovative technology has enabled products to be easily picked from the warehouse, as well as goods to be tracked whilst in transit in the warehouse. In contrast, the use of outdated technology means that companies cannot communicate properly with customers, nor can they provide information about the status of orders. Companies that implement and adapt to technology in their logistics strategy will get more revenue and a higher return on investment. Ensure that your business is integrated with the latest technology trends and implement the latest supply chain management software.
Congestion in Busy Receiving Area
The receiving area is the starting point of any warehouse, and if something goes wrong there, they will also enter the later stage. One of the biggest mistakes here is that the receiving area is too small or cannot overlap with the shipping area. Ensure that there is enough space to perform all tasks, including quality control activities, staging projects and labels.Starting from the previous point, even if the receiving area is large enough, it will still become very messy and disorganized.
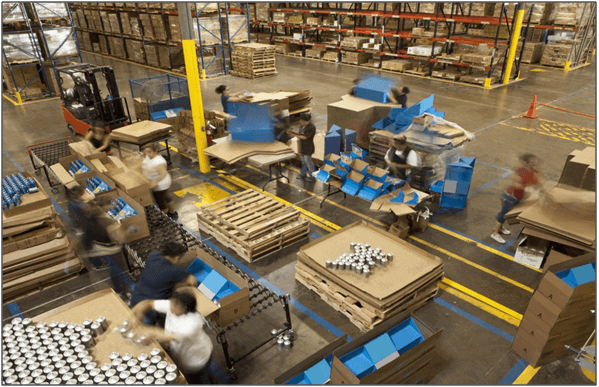
Grouping many pallet trucks, materials, workers, and boxes in one place can cause confusion and injury. Besides, this will greatly increase the processing time of goods due to congestion. First, you need to use marker tapes and potential obstacles to subdivide large areas into different colored paths and squares. This will inform workers where to walk, drive trucks or store pallets. This is easy to color but requires a small amount of preparation first. As we have mentioned many times before, proper training for forklift drivers is irreplaceable. Experience and good training can ensure safety. It is especially important to avoid many hazards in busy reception areas. Unless you have ever worked in this environment, you may not know how much waste packaging will be generated from the purchase. Be sure to use manual removal or garbage conveyor to remove waste as soon as possible. The easiest way to keep the area clean is to install an abundance of large garbage bins near the unpacking area. At this point, the tipper lorry will come in handy.
Failure to Optimize Picking Paths
Another common mistake made by organizations is poor optimization of the order picking path in the warehouse. The biggest change in the warehouse is labor costs, which affect your profitability. You need to ensure that your warehouse workers operate as efficiently as possible. To make the most of their time and energy, you should carefully study the location of the item concerning the pick-up speed. You should place products that are often picked together as close to each other as possible. Achieving this type of analysis can be overly complicated but using the right software package can solve this problem.
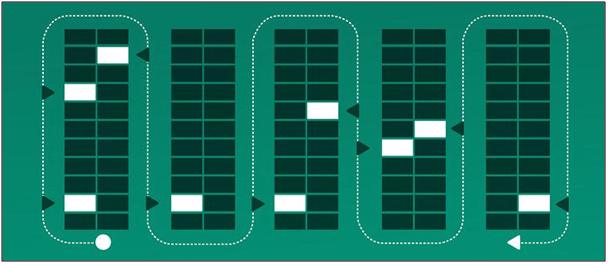
Material Handling Equipment (MHE)
MHE accessories, such as carton clamps, drum clamps, paper roll clamps, rotators, and push-pull elements, can affect the capacity of MHE in many ways, including accessories that can change the operating gap by extending the length and width of the MHE. The accessories can change the capacity of the MHE by increasing the weight. For example, if the accessory weighs 1,000 pounds, the amount of load that can be carried will be reduced by 1,000 pounds. Accessories usually change the stability and center of gravity of MHE.
Most MHE accidents involve pedestrians. The most obvious reason for accidents involving pedestrians is the blocked view in which the operator cannot see pedestrians due to loads of obstacles on the road. Turn the MHE towards pedestrians in front of or beside the MHE. Speeding to ensure that MHE cannot stop in time to avoid pedestrians, or not being aware of pedestrians in the area, or uploading passengers on MHE. Certain MHE hazards are caused by conditions existing in the MHE operating environment. For example, MHE operated with combustible fuel in poorly ventilated areas may accumulate carbon monoxide or carbon dioxide produced in MHE.
Operating in an environment with slopes will increase the chance of MHE accidents. Crossing the rails, you can balance the MHE, as well as operating and braking on slippery floors, operating in dirt and gravel, and poor lighting. Other possible hazards in a specific working environment may cause MHE accidents. These include pits or openings in the floor, crowded or cramped workspaces, and the presence of flammable and combustible materials.
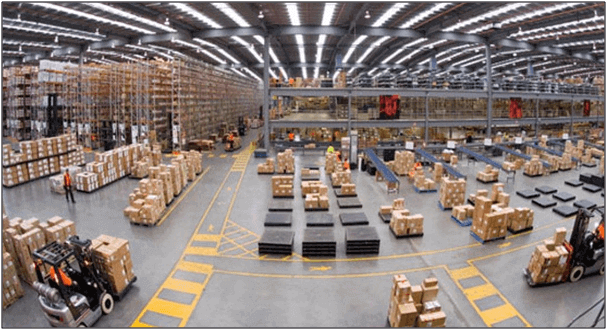
Lack of Proper Staff Development and Training
Another big challenge for warehouses is staff turnover. When workers leave the organization, huge costs are incurred. Employees leave for various reasons, but a common reason is that they believe that they have not received the training and development opportunities they deserve, exceeding expectations and growth. Employees who have not received training and development opportunities will also affect you. Without proper training, they are more likely to make mistakes, thereby reducing quality and increasing the efficiency of the supply chain. You should ensure that each position has a detailed training plan and that each employee has a career development plan for their goals
Lack of Safety Policies
If your employees keep getting hurt, they will need to spend more time off work or work slow to prevent their injuries from getting worse. If you try to cut corners or look at it from another angle on workplace safety issues, you are making a serious mistake. Workers’ compensation claims can cost you a lot of money. Do not wait for an apology after such an incident but be proactive by optimizing safety practices. Do your best to ensure that your workers are in a safe environment when they go to work and take some time to keep them up to date with current safety procedures.
Conclusion
Warehousing plays an important role in the operation of the supply chain to make positive contributions. To realize the smooth operation of WMS, it is necessary to plan first while the above factors must be considered to organize the warehouse to improve WMS.
References
Amran Hossain, DSLM.(2019). “Key Considerations for Warehouse Safety and Health”. Retrieved from SIPMM: https://publication.sipmm.edu.sg/key-considerations-warehouse-safety-health,accessed 10/09/2020.
David Chew Kian Peng, DSLM.(2018). “Four Key Areas for Mitigating Warehouse Risks”. Retrieved from SIPMM: https://publication.sipmm.edu.sg/four-key-areas-mitigating-warehouse-risks, accessed 05/09/2020.
Material Handling Hub. (2018). “Avoid Common Warehouse Mistake In The Receiving Area”. Retrieved fromhttps://www.materialhandlinghub.com/2017/07/21/warehouse-mistakes-receiving-area,accessed 05/09/2020.
Rob O’Byrne. (2015). “8 Common Warehousing Mistakes and How to Avoid Them”. Retrieved from https://www.logisticsbureau.com/7-common-warehousing-mistakes-and-how-to-avoid-them, accessed 05/09/2020.
Tom K.(2019). “Top 10 Warehousing Mistake to Avoid”. Retrieved fromhttp://www.leansupplysolutions.com/blog/top-10-warehousing-mistakes-avoid, accessed 10/09/2020.