Logistics are often part of the value chain in the steel industry, as storage and cooling processes contribute significantly to product quality. The entire industry is under cost pressure, which significantly impacts logistics processes. Warehouse management is critical to the efficiency of a steel supply chain. Warehouse management is complex and requires a lot of time and effort. An efficient warehouse should optimize space, simplifies processes, and increases worker productivity. When warehouses function well, customers receive their products on time, and the company’s bottom line is protected. Even as warehouses keep satisfying customers with on-time and accurate shipments, there are always operational changes that can improve warehouse performance. A typical warehouse has much activity at any given moment, so there is always room to enhance efficiency. This article examines some efficient strategies for enhancing warehouse operations.
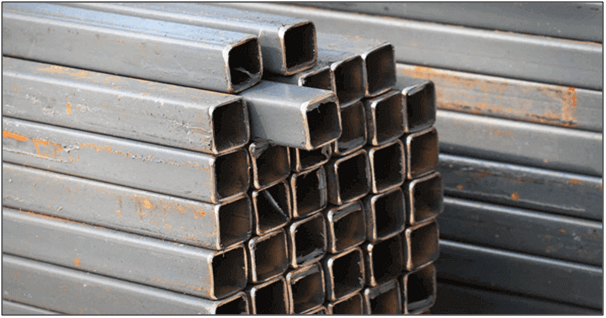
Table of Contents
Managing Warehouse Returns
A return is a return after the order has been delivered to the recipient. Returns may be due to repairs, cancellations, claims, or wrong delivery. Returns management impacts the customer experience and impacts a business’s bottom line. Improving the convenience and speed of returns service can provide a better customer experience and improve a business’s bottom line. The ideal returns management process is cost-effective for the retailer and hassle-free for the customer. As consumerism narrows the competitive gap in global markets, a streamlined returns management process is essential for businesses to reduce associated costs and differentiate themselves from their brands in shoppers’ minds. Proper merchandise management can significantly reduce losses by replenishing resale inventory with the undamaged returned merchandise. By working closely with suppliers to properly sort or sort returned products, reverse logistics can turn a liability into an asset and generate a solid return on inventory. This has a beneficial effect on the profit maximization process.
Managing Receiving Function
Receiving is the first phase in the fulfillment process and refers to delivering, unloading, and storing products at a warehouse or fulfillment center. A poor warehouse receiving procedure can lead to stock control concerns and increased operating expenses. A well-established warehouse receiving procedure may make inventory management and fulfillment easier, more cost-effective, and more efficient. The reception room should be despite accepting and transporting things. Avoid shelving that promotes goods to be kept in the space. The space must be able to support the circulation of commodities that come in various forms of packaging. During receiving, all arriving products must be thoroughly inspected, tagged, and recorded as received. When these data are correct, it is easier to fulfill client orders or manage production processes efficiently.
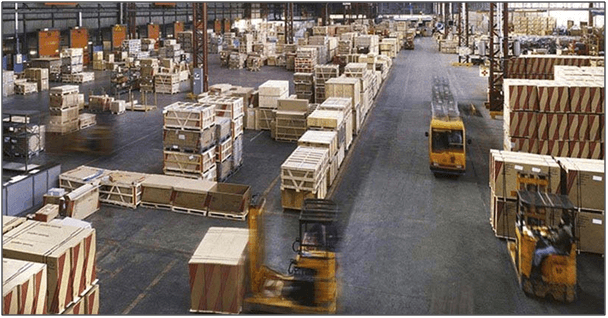
Managing Put-Away Function
Put-away refers to all the operations in a warehouse between receiving items from suppliers and having them all put away in their designated locations. Warehouse put-away is an essential part of warehouse management that entails various operations beginning with warehouse receiving and ending with ensuring that goods are kept in the correct warehouse locations. Warehouse put-away decreases the requirement for warehouse audits while also increasing product availability. Here are some typical procedures warehouse personnel perform during put-away: First, transfer items are received, then items are identified and inspected, then products are moved to the appropriate storage area, and finally, they are labeled and placed on the appropriate shelves.A systematic put-away process can store goods without losing any SKUs. This makes the process much more efficient and straightforward. Correct warehouse put-away may enhance picking, storage, and inventory tracking, among other facets of SKU management.
Implementing WMS
Because of the expanding importance of warehousing in the supply chain function, many corporations or enterprises are imposing WMS to optimize and support good warehousing procedures. Firms can minimize initial investment costs and prevent expensive conservation expenditures by engaging with a proper WMS. The focus of warehouse procedures is on product movement, including, but not limited to, receipt planning, receiving, storage, order picking, labelling, shipping, cross-docking, drop shipping, and other processes. Opting for the right WMS can help control and support a warehouse’s routine operations. Other advantages of using a WMS include reduced operating costs, visibility of inventory, efficient labour, traceable materials, better customer service and improved supply chain efficiency. WMS can be a stage-alone system or integrated within a system that may support robotization, radio-frequency identification (RFID), or voice recognition. A good and well-suited WMS is suitable for giving real-time records and reports as needed.
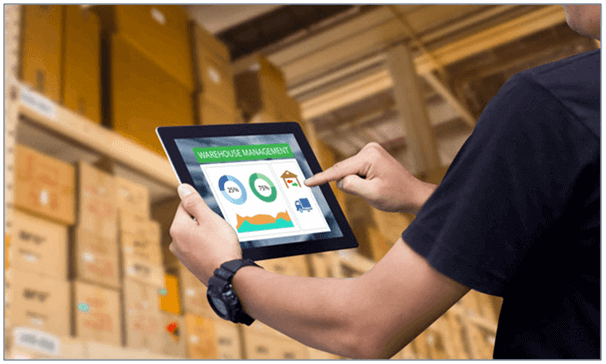
Planning Warehouse Layout
Warehouse layout can be between a seamless and efficient space and a messy and inefficient space. Ideally, a warehouse design should be based on the needs, which will require identifying a company’s unique goals. A practical warehouse layout should be able to draw a straight line from receiving area to inventory management to the pick, pack, and ship departments. If that line intersects or overlaps at any point, it could indicate that the current layout requires better space utilization. The fundamental elements can be easily recalled using the acronym FAST, which stands for F-Flow, A-Accessibility, S-Space and T-Throughput. There is no ranking of importance and each is equally essential, as its goal is to find the optimal balance of these sometimes-opposing elements. When one element is reviewed and changed, the others should be revisited to determine the influence of that modification on the whole process.
Organizing Warehouse Resources
Warehouse organization may sometimes feel like a never-ending battle. Warehouse organization is the process of organizing the warehouse to improve inventory control, time management, and workforce efficiency. However, clean and well-organized warehouses speed up receiving, storing, picking, packaging and shipping them to clients. Organized storage space is a great way to reduce waste, increase productivity, improve inventory management, and reduce maintenance or service costs. Additionally, a well-organized warehouse can help businesses reduce health and safety issues by minimizing accidents and injuries caused by falling objects, slippery surfaces, and other risks.
The full content is only visible to SIPMM members
Already a member? Please Login to continue reading.