Storage and inventory control processes include the activities related to holding material and the processes of counting and transacting the material as it moved through the warehouse. The layout of a warehouse that supports an adjoining manufacturing facility will have different requirements than a facility supporting product distribution to stores or a facility that supports end-user fulfillment.
Best-practice companies have designed storage systems to meet the needs of the current and planned mix of storage types. By optimizing the storage locations and layouts to fit product without the need to restack it once received.
The WMS will track storage location and properly assign product to the best storage location. As a result, best-practice companies have excellent cube-fill rates. In addition, to optimize the cubic fill of storage locations, best practice is to minimize travel time. If a product is in high demand it should be placed closer to its next point of use.
The picture below shows the layout of a typical warehouse
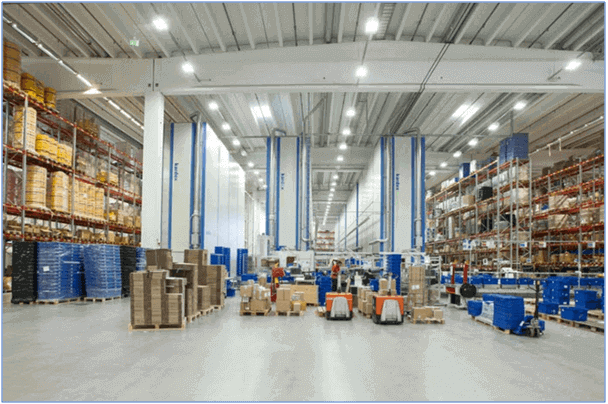
The difficulty of retrieval should also be considered in travel time. Higher-demand product should be placed on the most easily accessed storage space, typically floor level for racking and between waist and shoulder level in pick racks. Most companies put a lot of effort into the initial layout of the warehouse.
Reviewing how storage areas are configured and having processes in place to reconfigure storage areas as product mix changes is considered best practice and is critical to maintaining high levels of space utilization and efficiency. Making continuous small adjustments to racks, shelving, or other storage equipment can greatly improve space utilization.
The picture below shows the optimal storage using shelves in a warehouse
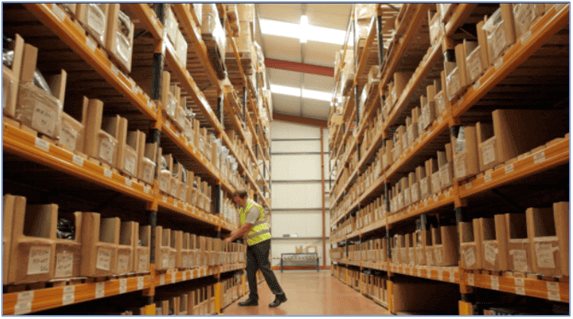
As a company’s retail sales steadily grow, so does the need for modern storage capacity for its products. At the same time, the requirements demanded of storage systems also grow, because the efficient processing of incoming orders is now an acritical competitive factor for suppliers.
This is also an area in which there is a huge amount of dormant potential when it comes to increasing productivity. According to studies, the order picking process alone accounts for up to 55 percent of the total cost of storage. The main reason for this is the time taken by employees to locate the stored items and bring them to the picking station. It is the distances covered alone which devour almost two thirds of the total time warehouse employees spend working.
Efficiently organizing the incoming goods section of a warehouse is just as important for its productivity as ensuring that it has effective shelf storage systems. After all, if the incoming goods section is not set up correctly, this almost automatically leads to severe disruption in the entire subsequent storage process.
Table of Contents
Designing the incoming goods section
In the incoming goods section the goods are identified, checked, and prepared for storage in a multi-stage process. Due to the close link between warehouse logistics specialists and suppliers, information on the incoming goods is generally available beforehand, making it possible to identify them by matching up bar codes or performing a similar task. One essential requirement for simplifying the checking process with a scanner is the establishment of a numbering or bar coding system which can be clearly understood by both parties. If this does not exist, the checks must be performed manually.
The picture below shows temporary storage of incoming goods for inspection
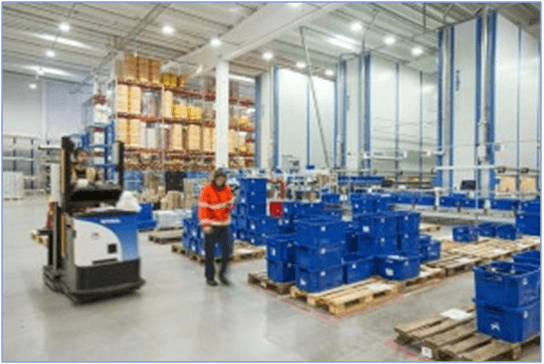
Once the nature and quantity of the incoming goods have been checked, they continue to quality control. This process sometimes varies considerably – depending on the type of goods delivered – and can range from a cursory check to a detailed analysis of individual goods or the entire delivery. After the incoming goods have been successfully checked, they are passed on for storage.
The aim of an efficient incoming goods system is to prepare the items for subsequent storage. If mistakes are made in the incoming goods section, this can have costly consequences when the goods are stored and later relocated or retrieved. It is worth considering the sheer impossibility of the task of finding individual goods which have been stored in the wrong place in a warehouse. Poor utilization of the space due to bad planning in the first place can also lead to a lack of waste of storage space.
Errors made while storing goods have an impact on the entire subsequent storage process. Consequently, it is essential that storage logistics specialists have a precise strategy for the efficient storage of goods.
Classifying the inventory
How precisely the inventory should be classified depends on a whole range of factors. The key features to consider are the size and weight of the stored goods and the frequency with which they are retrieved. In doing so, it proves to be especially efficient to review ALL stored goods and not just concentrate on optimizing fast-moving goods. The 80/20 rule often used by companies as a criterion, which states that 20 percent of goods account for 80 percent of sales, falls short here, because conversely this would mean that the company fails to take into consideration 80 percent of its goods – and thus the greater part of the total storage space – in the optimization process. After all, it is the less frequently retrieved goods which compel the warehouse employees to cover especially long distances and are thus the cause of added costs since they are stored a long way away from the picking stations. As such, it is advisable for the company to find a total solution for all goods in the warehouse.
Identifying the optimal storage location for goods
The better the way in which the various goods are stored, the more efficiently their retrieval can be managed. This also brings about improvements in terms of:
- Retrieval times
- Picking accuracy
- Work processes
- Search times
To find the optimal position for each individual product within the warehouse, further data is required in addition to information about the goods (size, weight, etc.):
- Retrieval frequency
- Number of retrieved units in each case
- Number of units to be stored
- Product-specific storage requirements
- Turnaround frequency
WMS then allocates the optimal location to the goods based on this data.
The full content is only visible to SIPMM members
Already a member? Please Login to continue reading.
References
Andrew Tan Howe, MSIPMM. (2017) “Effective Inventory Management Practices for Fast Moving Consumer Goods”. Retrieved from https://publication.sipmm.edu.sg/effective-inventory-management-practices-fast-moving-consumer-goods, accessed 20/03/2018.
Intralogistics. (2015). “Efficient storage in six steps – How companies can better manage their inventories”. Retrieved from https://intralogistics.tips/efficient-storage-in-six-steps-how-companies-can-better-manage-their-inventories, accessed 20/03/2018.
Intralogistics. (2015). “Effective storage strategies – The basis for successful warehouse management”. Retrieved from https://intralogistics.tips/effective-storage-strategies-the-basis-for-successful-warehouse-management, accessed 20/03/2018.
Kate Vitasek. (2007). “Storage and Inventory Control Best Practices”. Retrieved from http://multichannelmerchant.com/operations/storage-and-inventory-control-best-practices, accessed 20/03/2018.
Newcastle system. (2016). “How to Improve Warehouse Receiving Process”. Retrieved from https://www.newcastlesys.com/blog/how-to-improve-warehouse-receiving-process, accessed 20/03/2018.