Materials handling in the past would have been very simple, starting off people carrying items unassisted, eventually graduating to basic modes of transport such as horse and cart to carry larger items. In the early years, Hyster was a major contributor to the design and manufacturing of the first forklift trucks. The company was a pioneer in developing specialist machinery for materials handling in the logging and metal works industries respectively.
Material Handling and Logistics as defined by the Material Handling Industry of America is the movement, protection, storage and control of materials and products throughout the process of their manufacture and distribution, consumption and disposal. The most stunning technology of material handling must be the invention of universal forklifts. Till today, people never stop using innovative material handling technology to handle normal or anomaly materials, such as container, stone, timber, prefabricated concrete units, steel and glass.
Table of Contents
Revolution of Material Handling Equipment (MHE)
Material handling equipment are not only used on smooth and solid roads, but also operated on the muddy ground, climbing up the stairs or entering mining area which needs to be explosion-proofed.
Autonomous machines must be able to work in environments alongside people, and assist them in their work, without the risk of accidents. They ought to be able to communicate with other facilities in the infrastructure in real time, in order to ensure a smooth workflow. In addition, in many industries the production and logistics processes change just as dynamically as the products and goods themselves.
All of this tells us that the innovation of material handling equipment around the world is various while applicable. People will comply with one rule when inventing and innovating as using high-efficient handling to reduce logistics cost while taking the concept of human-oriented. Moreover, high-efficient handling shall rely on high technology, which again refers to invention and innovation.
Designed according to Spark Proof for Chemical and Gas Industry
During the design of spark proof warehouse handling trucks, engineers use technologies designed for defined explosion groups and temperature classes. Depending on how sensitive an explosive substance is, it is classified into a particular explosion group. Substances in higher explosion groups, such as hydrogen or acetylene gas, require more extensive protective measures on the trucks.
Explosion Protection Measures on Electro Trucks
In order to prevent sparking from electric material handling equipment, all electrical components, such as drive, lift, pump, steering motor and electronic control units such as relays, operating hour counters or battery capacity display are encapsulated in pressure-resistant housings.
Autonomous Guided MHE (AGM)
AGMs are programmed by CAD-based software that routes available paths and also indicates locations that vehicles are to pick or deposit a load. AGMs are often guided by humans on their initial tour through a facility before their paths can be guided and updated by the CAD system.
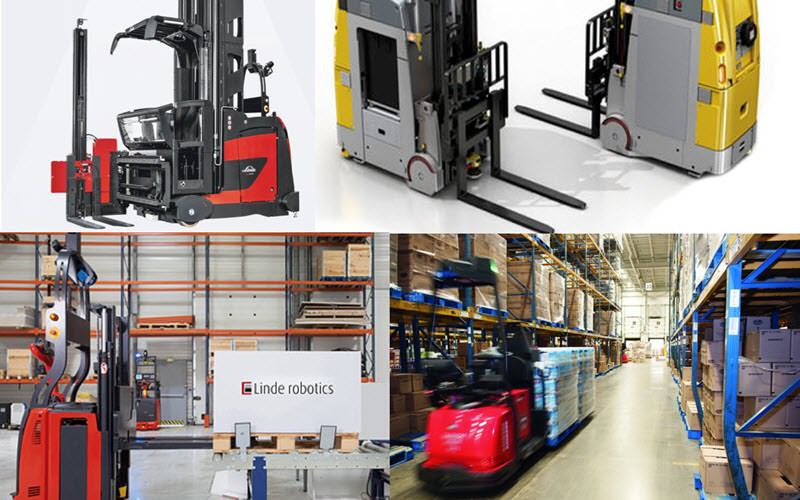
Traffic controllers are responsible for load movement requests and task assignments to each of the vehicles. Finally, AGMs are left to determine best possible routes for efficient movement of loads.
1. Installing an AGM:
Easy and fast installation – Aside from making sure the path is defined in the CAD programs used to manage the process, with this technology, permanently installed infrastructures – for example with reflectors or rails – are no longer required: The safety laser scans and registers all obstacles. The robot vehicles react immediately and, for example, stop when a worker or vehicle blocks or crosses their path and only start again when the way ahead is clear.
2. Powering an AGM:
When using a high-efficiency, permanent batteries – no routine battery changing is required. While there are some recommended charging maintenance procedures to insure a ten-year operating life on batteries is achieved, most are automatically performed by the system during non-work periods. This ultimately means no battery changing, no special operators for changing or charging batteries, no degassing facility and no need to handle hazardous fuel for disposal.
AGMs often employ automatic opportunity battery charging stations throughout the path so vehicles need not be removed from service. Each time the vehicle interfaces a drop off position, opportunity charge connectors can be used to “give the vehicle a drink” before it moves to the next task. In some cases, a special area is setup for the vehicles to use when parking that can also serve as charging positions. In most cases, a 2-minute charge will provide 20-30 minutes of capacity.
3. AGM Maintenance:
The support and service thru of onboard smart controller. This controller continuously updates and records the vehicle’s operational status thus displaying the probable cause of any issue that might occur. The Maintenance Operating Systems offered by Bastian Solutions also assist with the automated tracking of usage, and the scheduling of PM Service routines per the manufacturer’s recommendations – relieving the shop staff of the need to monitor and schedule these procedures.
4. AGM Safety:
Safety is the overriding priority for the entire range of products, and above all, in mixed deployment scenarios with automated and manually operated vehicles. For instance, in addition to safety scanners, a computer module with a 7-inch LCD monitor and a 3D camera, the comprehensive route monitoring system also features vehicle-mounted warning flashers, horns and BlueSpot safety lights.
The full content is only visible to SIPMM members
Already a member? Please Login to continue reading.
References:
Aalhysterforklifts, (2017). “Logistics & Materials Handling Blog”. Retrieved from http://www.aalhysterforklifts.com.au, accessed 09/09/2017.
Bastian Solutions, (2017). “Automated Guided Vehicles”. Retrieved from https://www.bastiansolutions.com, accessed 09/09/ 2017.
Forklift Net, (2017). “Introduction of Innovation in Global Material”. Retrieved from http://www.forkliftnet.com, accessed 09/09/ 2017.
Linde Material Handling, (2017). “Flexible automation for intralogistics”. Retrieved from http://www.linde-mh.com/en/Solutions/Automation, accessed 09/09/2017.
Linde Material Handling, (2017) ‘Safe logistics service thanks to explosion protection Explosion-proof forklifts’ Retrieved from http://www.linde-mh.com/en/Products/Explosion-Proof-Trucks, accessed 09/09/2017.
MHEDA, (2004). “The History of the Material Handling Industry”. Retrieved from https://www.mheda.org/, accessed 09/09/2017.