Warehousing is the act of storing goods that will be sold or distributed later. Warehousing and all that goes along with it is part of a sophisticated industry known as inventory management. Inventory systems help a business monitor, track and controlling inventory orders, raw materials, finished goods usage and storage along with management of finished goods that ready to sales. The picture below shows the physical inventory count in a warehouse.
The process typically involves a retail staff member (or team of workers) going through the stock room and counting. The data is then recorded either manually, using pen and paper or electronically using a mobile device. The cycle counting can be done daily or weekly (usually before the store opens) and can free you from having to do full inventory counts.
Table of Contents
ABC Inventory Analysis Technique
The ABC analysis is a business term used to define a listing categorization technique often utilized in material management. It is also referred to as “Selective Inventory Control” ABC evaluation provides a system for identifying items which will have a substantial effect on overall inventory cost, while also offering a system for identifying different types of stock which will require different administration and configurations that inventories of a business aren’t of equal value.
ABC evaluation allows inventory/purchasing managers to segregate and manage the entire inventory/suppliers into three main groups. It will help in maintaining inventory turnover rate at a comparatively more impressive range through scientific control of inventories. This allows different inventory/supplier management ways to be applied to different segments of the inventory/supplier to be able to increase revenue and decrease costs. Here inventory items are classified into three categories namely A (highly expensive) B (moderately expensive) and C (least expensive)
Vital, Essential and Desirable (VED) Analysis Technique
VED stands for vital, essential and desirable. This analysis relates to the classification of maintenance spare parts and denotes the essentiality of stocking spares. The spares are split into three categories in order of importance. From the view-points of functional utility, the effects of non-availability at the time of requirement or the operation, process, production, plant or equipment and the urgency of replacement in case of breakdown. Some spares are so important that their non-availability renders the equipment or a number of equipment in a process line completely inoperative, or even causes extreme damage to the plant, equipment or human life.
On the other hand, some spares are non-functional, serving relatively unimportant purposes and their replacement can be postponed or alternative methods of repair found. All these factors will have direct effects on the stocks of spares to be maintained. Therefore, it is necessary to classify the spares in the following categories:
• Vital items that render the equipment or the whole line operation in a process totally and immediately inoperative or unsafe; and if these items go out of stock or are not readily available, there is loss of production for the whole period.
• Essential items that reduce the equipment’s performance but do not render it inoperative or unsafe; non-availability of these items may result in temporary loss of production or dislocation of production work; replacement can be delayed without affecting the equipment’s performance seriously; temporary repairs are sometimes possible.
• Desirable items which are mostly non-functional and do not affect the performance of the equipment.
As the common saying goes “Vital Few — trivial many”, the number of vital spares in a plant or a particular equipment will only be a few while most of the spares will fall in ‘the desirable and essential’ category. However, the decision regarding the stock of spares to be maintained will depend not only on how critical the spares are from the functional point of view (VED analysis) but also on the annual consumption (user) cost of spares (ABC — analysis) and, therefore, for control of spare parts both VED and ABC analyses are to be combined.
FSN Technique
Here the items are classified into fast-moving (F), slow-moving (S) and Non-moving (N) items on the basis of quantity and rate of consumption. The non-moving items (usually, not consumed over a period of two years) are of great importance. It is found that many companies maintain huge stocks of non-moving items blocking quite a lot of capital. Moreover, there are thousands of such items. Scrutiny of these items is made to determine whether they could be used or to be disposed of. The classification of fast and slow-moving items helps in the arrangement of stocks in stores and their distribution and handling methods.
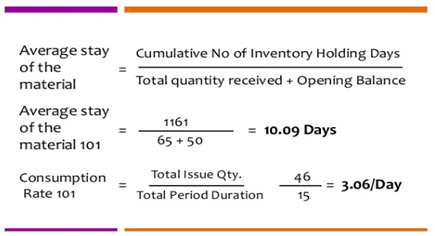
Just-In-Time Technique
Just in time inventory, also known as JIT inventory, is the reduced amount of inventory owned by a business after it installs a just-in-time manufacturing system. This type of system is called a “pull” system. The intent of a JIT system is to ensure that the components and sub-assemblies used to create finished goods are delivered to the production area exactly on time. Doing so eliminates a considerable amount of investment in inventory, thereby reducing the working capital needs of a business. In this method, the company keeps only that much of inventory which needed during production. This saves insurance and storage cost.
Material Requirement Planning (MRP) Technique
Material Requirements Planning (MRP) is a computer-based production planning and inventory control system. MRP is concerned with both production scheduling and inventory control. It is a material control system that attempts to keep adequate inventory levels to assure that required materials are available when needed. MRP is applicable in situations of multiple items with complex bills of materials. MRP is not useful for job shops or for continuous processes that are tightly linked. The major objectives of an MRP system are to simultaneously:
(1) Ensure the availability of materials, components, and products for planned production and for customer delivery.
(2) Maintain the lowest possible level of inventory.
(3) Plan manufacturing activities, delivery schedules, and purchasing activities.
Material requirement planning (MRP) is a technique in which order is placed after considering sale forecast
Economic Order Quantity Model
Economic order quantity (EOQ) is a procedure to determine the ideal order quantity level for stock to be ordered at a particular time. It also a formula that used to determine the most efficient amount of goods that should be order and carrying cost may be reduced to a minimum point. A firm should place optimum orders and neither too large nor to small. The EOQ is level of inventory order that avoid stock-out and overstock and minimizes the total holding costs and ordering costs.
The full content is only visible to SIPMM members
Already a member? Please Login to continue reading.
References
Chong Yaw Wen, DPSM. (2019). “Essential Techniques for Inventory Control of Laboratory Equipment”. Retrieved from SIPMM: https://publication.sipmm.edu.sg/essential-techniques-inventory-control-laboratory-equipment/#ABC_Inventory_Analysis, accessed 07/12/2019.
Joffrey Collignon, JoannesVermorel, (2012) Prioritization of the management attention https://www.lokad.com/abc-analysis-(inventory)-definition, accessed 16/12/2019.
Lee Yi Xian, DLSM. (2019). “Inventory Control Techniques for Effective Warehousing”. Retrieved from SIPMM: https://publication.sipmm.edu.sg/inventory-control-techniques-effective-warehousing,accessed 07/12/2019.
Malik Shawal. (2019) “VED Analysis /FSN Method”. Retrieved from http://www.yourarticlelibrary.com/business-management/marketing-management-business-management/ved-analysis-sde-analysis-and-fsn-analysis/69363, accessed 14/12/2019.
NidaulHasanati. (2019). “Implementation of Material Requirement Planning (MRP) on Raw Material Order Planning System for Garment Industry”. Retrieved from https://iopscience.iop.org/article/10.1088/1757-899X/528/1/012064/pdf,accessed 16/12/2019.
Steven Bragg. (2019). “Just in Time”. Retrieved from https://www.accountingtools.com/articles/what-is-just-in-time-jit-inventory.html, accessed 07/12/2019.