Integrated logistics is the one-stop solution to the shipping and logistic requirements of the company. Fast and secured transportation is the key requirement of any business. The transportation of raw material, as well as the finished products, is an important part of the development of all businesses. The proper planning and arrangement of integrated logistics are therefore required to have interrupted supply chain management.
The integrated logistics ensure that you get the fully arranged logistics services like shipping, warehousing, trucking and stevedoring. To achieve effective integrated logistics operations in the food industry there are a few practices which are highly recommended in the current market.

Table of Contents
Effective Planning of Logistics Process
The initial step to achieving a task is planning. Presently, arranging exemplifies different variables. It includes securing the stock, storage facilities, and conveyance of items to the accurate area. Apart from these, other parameters are time, transportation, and costs. A supply chain operative should be able to devise the stream diagram for the entire activity. The reason for arranging is to accomplish the most extreme work at all conceivable time. In the meantime, the planning should go for boosting the benefits.
Appropriate planning is an insightful arrangement, yet an experienced manager will most likely plan for the unanticipated conditions too. These circumstances can be identified with:
- The products
- Unavailability of the transportation
- Any internal issue in the organization
- Research and pick the correct Freight class.
With a good planning process, you regularly review assumptions, track progress, and catch new developments so you can adjust. Plan vs. actual analysis is a dashboard, and adjusting the plan is steering.
Implementation of Warehouse Management System (WMS)
A WMS is an instrumental part of the supply chain. The supply chain’s primary goal is to track and control products. Such as, tracking movement of products, and controlling inventory actions. Including, receiving, adding, picking, quality control, shipping, reporting, and forecasting. Implementing a WMS can help an organization reduce labor costs, improve inventory accuracy, improve flexibility and responsiveness, decrease errors in picking and shipping goods, and improve customer service. Modern warehouse management systems operate with real-time data, allowing the organization to manage the most current information on activities like orders, shipments, receipts and any movement of goods.

Implementation of Transportation Management System (TMS)
TMS is offered as a module within enterprise resource planning (ERP) and SCM suites and helps organizations move inbound — procurement — and outbound — shipment — freight using tools such as route planning and optimization, load building, operations execution, freight audit and payment, yard management, order visibility, and carrier management. The ultimate goals of using a TMS are to improve shipment efficiency, reduce costs, gain real-time supply chain visibility and enhance customer service.
A fully deployed transportation management system can benefit organizations in the following ways:
• Transportation order planning and execution
• Supply chain visibility and better control of inventory management.
• Reduce invoice errors.
• Transport intelligence.
A key activity is to provide for the movement of materials and goods from point of origin to point of consumption. Transportation involves selection of the mode (e.g., air, rail, water, truck, or pipeline), the routing of the shipment.
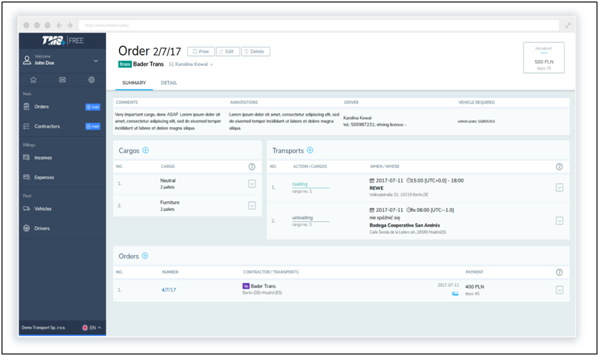
Automation technology for warehouse operations
Warehouse automation is widely touted as one of the most effective ways to boost ROI by reducing labor demands, enhancing accuracy, and improving efficiency. “One indisputable fact exists,” according to Supply Chain Management Review. Warehouse automation is one of the last areas where long-term costs can be significantly reduced.” But some think of warehouse automation as software, while others think about the idea of automating a warehouse as implementing automated storage and retrieval systems (AS/RS). In reality, complete warehouse automation entails automating a variety of aspects of operations, from automatic data capture to software systems, storage and retrieval, and more.
The full content is only visible to SIPMM members
Already a member? Please Login to continue reading.
References
Alagappan Dasarathy, DLSM. (2018). “Integrating warehousing and transport functions for EPC projects”. Retrieved from SIPMM: https://publication.sipmm.edu.sg/integrating-warehousing-transport-functions-epc-projects/, accessed 07/10/2018.
Arianna Thayer. (2017). “What is a Warehouse Management System”. Retrieved from https://www.skuvault.com/blog/what-is-a-warehouse-management-system-wms/,accessed 16/02/2017.
Liz Burton. (2018). “The Important Of Food Hygiene Training”. Retrieved from https://www.highspeedtraining.co.uk/hub/importance-of-food-hygiene-training/, accessed 10/01/2018.
Margaret Rouse. (2018). “Transportation Management System”. Retrieved from https://searcherp.techtarget.com/definition/transportation-management-system-TMS,accessed 29/03/2018.
Quick Shift (2019). “success key for effective logistics management”. Retrieved from https://yourstory.com/mystory/success-key-for-effective-logistics-management, accessed 25/04/2019.
Sazali Salleh, PDWM. (2019). “5 Best Practices for an effective warehouse”. Retrieved from SIPMM: https://publication.sipmm.edu.sg/five-best-practices-effective-warehouse/, accessed 11/04/2019.
Tan Yen Pheng, DLSM. (2019). “Best practices for chilled and frozen food storage warehouse” Retrieved from SIPMM: https://publication.sipmm.edu.sg/best-practices-chilled-frozen-food-storage-warehouses/, accessed 11/04/2019.