Warehousing is the act of storing goods that will be sold or distributed later. To have an effective warehouse in the current world of business and due to overwhelming challenges from competitors, we must keep with current warehouse practices and bring in new practices which will make warehouse objective targets and customer demands move faster and more efficient. The needs of all your customers must be considered in all warehouse-planning activities. Otherwise, rather than meeting their needs, you probably are reacting to their demands. Each problem can have multiple solutions. Such factors as available space, equipment, personnel, and investment capital, as well as a willingness to change, help determine which solutions are available to us. To achieve effective warehouse operations, there are five best practices which are highly recommended in the current market.
Table of Contents
Deploy Dock Scheduling Software with Your WMS
When your dock is in high demand in these situations, it makes sense to think of it as a popular, limited quantity asset in the same manner as a restaurant, a dentist’s office or a salon. In other words, it should require an appointment. A Dock Scheduling Software can integrate with your existing systems and provide an interactive interface.
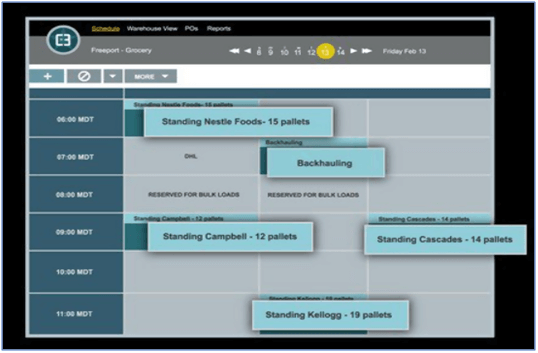
A good dock scheduling software product can integrate with your Warehouse Management System (WMS), Transportation Management System (TMS) or ERP. Taking a good inventory of the different events and transactions described in the list above can allow you to automate a lot of the scheduling and create an interactive portal where late arrivals, no-shows, etc. are tracked 24/7 and creates visibility to all your managers.
Pick by Voice – Technology of the Future
Development of picking/ commissioning systems based on voice command technology is a logical step in optimizing these applications. The clear goal is the use of new technologies to improve and increase the productivity of the process of commissioning. The technology presented as the Pick by Voice completely replaces the outdated system based on printed documents. Moreover, Pick by Voice can be easily combined with standard barcode technology.
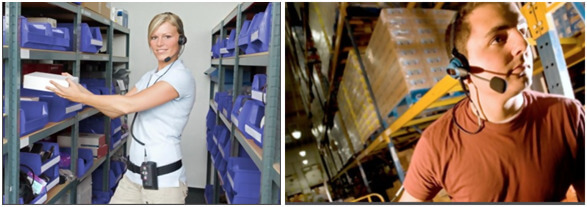
Increasing Work Productivity
In contrast to the standard solutions for picking/commissioning, Pick by Voice offers an additional advantage by significantly reducing the steps needed in the process of commissioning. The operator receives tasks via headphones and confirmed by voice response performance in microphone. This saves time by eliminating paper documents and barcode devices. The operator can fully concentrate on the process of picking and thus increase the accuracy of the tasks.
Standard Systems and Components
Communication system with voice recognition is accomplished by a small mobile computer that is attached to the operator belt. As standard equipment and device specially designed for harsh environments can be used. Pick-by-Voice can be easily connected to existing systems for warehouse management or ERP systems through a common database or file interface allowing integration of voice-based system simply as an additional module to the existing system for logistics management. Experience shows that after the introduction of Pick-by-Voice system quality and productivity increased sharply, leading to frequent ROI in less than a year.
Receiving Operation
Handle it once. The more times an item is handled and the more individuals involved in the handling, the more time and money you are wasting. Materials must be received and stored with total accuracy. Your database for inventory must be updated as goods are received. Having one person in receiving checking off received materials from a list, then sending the materials for stocking, then sending the list for database updating is not efficient. Inbound processing and the right Enterprise Resource Planning (ERP) software can allow one individual to check in materials and record the inventory in one step. Those materials can then be routed to the correct location in your warehouse.
Select a system of barcode scanning or RFID and take the extra handling out of your receiving operations. This system will also allow the data from incoming shipments to be sent directly to the purchasing and AP departments to update the information for timely payments of invoices. Just-in-time (JIT) delivery is a method for keeping excess inventory from building up in your facility. The more material you have just sitting on shelves, the more money you have tied up in that inventory.
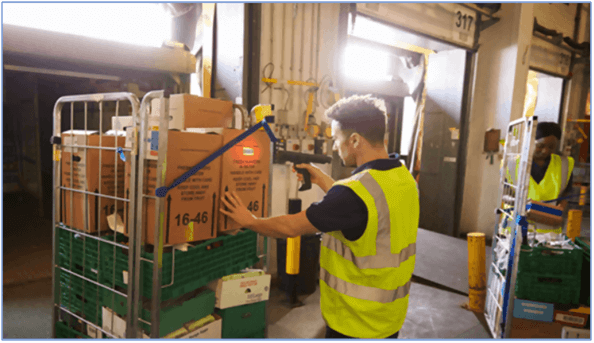
ABC Inventory Analysis
The ABC analysis is a popular inventory categorization method/technique that often used in material management and Inventory control. ABC analysis provides a mechanism for identifying items that will have a significant impact on an overall inventory cost and it also helps to identify different categories of stock that will require different management and controls.
ABC analysis divides the inventory into three categories. “A” item is very important or being the most valuable items for an organization, “B” item is important but of course less important than “A” or being the intergroup item, “C” marginal important or the least valuables item. By knowing the importance and values it helps warehouse to reduce the time to allocate and put-away.
The full content is only visible to SIPMM members
Already a member? Please Login to continue reading.
References
Balaguru Patmanathan, DLSM (2018). “The Five Essential techniques for effective warehousing”. Retrieved from SIPMM: https://publication.sipmm.edu.sg/the-five-essential-techniques-for-effective-warehousing/, accessed 13/03/2019.
Lee Yi Xian, DLSM (2019). “Inventory Control Techniques for Effective Warehousing”. Retrieved from SIPMM https://publication.sipmm.edu.sg/inventory-control-techniques-effective-warehousing/, accessed 13/03/2019.
Newcastle Systems. (2018). “Managing Dock Traffic”. Retrieved from: https://www.newcastlesys.com/blog/managing-dock-traffic, accessed 13/03/2019.
SICK. (2019). “Smart, Digitized Sorting and Tracking Ensures Success of Your Operations”. Retrieved from https://www.supplychain247.com/article/smart_digitized_sorting_and_tracking_ensures_success_of_your_operations/best_practices, accessed 13/03/2019.
Storact Log. (2019).“Technology picked by Voice”. Retrieved from: http://wms-bg.com/en/Products/Pick-by-Voice/, accessed 13/03/2019.