Modern business transformation has been greatly influenced by the advancement in modern technology. A smart warehouse is the start of the modern warehouse model and an end towards the conventional manual warehouse management. The objective of a smart warehouse was to maximize effectiveness and efficiency through automation, agility, collaborative robots, and data visibility. This article discusses key considerations for establishing a smart warehouse through technology. Modern technologies play an important part in the business world. In a fast pace world, companies need to rely on smart technologies where computers and machines are used for warehouse operation that were traditionally performed by people.
Table of Contents
Automatic Storage and Retrieval System (ASRS)
ASRS is commonly used in modern warehousing models to boost storage capacity and maximize output through systems and technology. However, any organization needs to ensure that the correct systems are selected based on the nature of the business and the company’s long-term goals. A company can use historical data and trends to simulate the estimated projections with optimal inventory holdings and SKU velocity classifications. The data will accurately point the company to the required size and throughput capability of the ASRS and provide a positive impact on the entire fulfilment process. This helps to boost both the upstream and downstream processes in the organization. Shelf-based, bin-based and robotics picking are the various type of ASRS models. Selecting the correct model of ASRS will maximize the return of investment between cost and time savings.
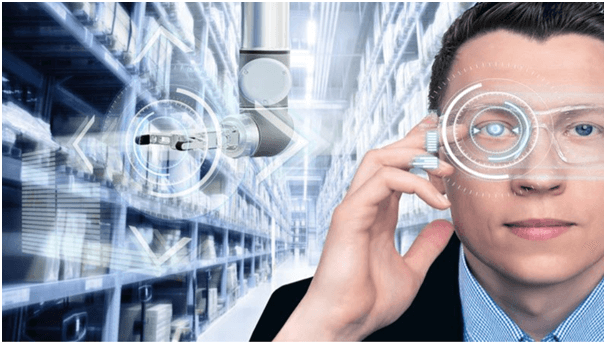
RFID Technology and Warehouse Layout Design
Radio-Frequency Identification(RFID) technology helps to identify an object through radio waves without human intervention. With an RFID identity, data collected are transferred through a communication interfaces to a system where it could be stored as data-based or to be analysed when required. RFID is often integrating with barcoding technologies to create smart labels which can be used for inventory management and personnel tracking applications.
The smart warehouse uses RFIDs to manage warehouse functions such as RFID stock count and inventory inbound/outbound tracking purposes which boost throughput maximizing efficiency in operations processes and minimizing possible warehouse challenges such as manual man-made errors. A warehouse layout must be planned in a logical process flow as it will directly impact the efficiency and productivity of any warehouse.
A well-planned layout will help in streamlining operations and reduce excess and overhead expenses to improve fulfillment throughput. Warehouse layout needs to be planned at the initial stage with the available budget as any changes to the planned layout would be costly and difficult to achieve due to the need to change the initial design. The layout also needs to follow government rules and regulation. In case of any emergencies or fire breakout, there should be an easy and nearest exit for anyone in the warehouse to exit safely and immediately.
Autonomous Mobile Robots(AMR) and Automated MHE
AMR are robots that can move through their environment without any human intervention or on a pre-determined route. AMRs use the sensor to perform the non-value-added activities in a warehouse environment. Thus, AMR allows an organization to free up laborers to perform more value-added activities within warehouse operations. The three core functions that AMR can boost efficiency are moving inventory within a facility, assist in picking processes and perform a flexible sortation solution. These functions can perform 24/7 within a warehouse operation to boost maximum fulfilment throughput once implemented.
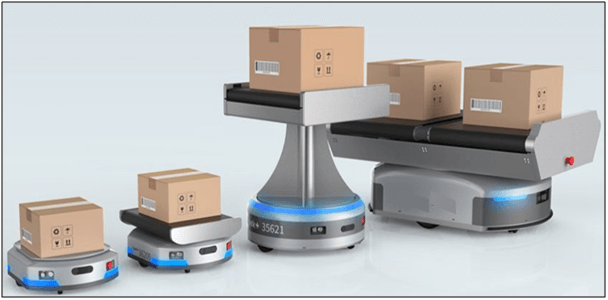
There has been a growing boom in the use of Automated Guided Vehicles (AGVs). AGV uses technology such as sensors and lasers to navigate within a designated area. The advantages of the usage of AGVs include reduction in labour cost, improve safety performance and increase accuracy and productivity in the warehouse operations. AGVs allow a company to upskill employees to more value-added activity and thus allowing the replacement of human workers on equipment such as forklifts. This will further improve manpower in other supply chain functions to reduce workload. The organization thus is only required to pay a fixed cost on the assets rather than ongoing costs such as taxes, increasing salaries, and health care coverages.
The full content is only visible to SIPMM members
Already a member? Please Login to continue reading.
References
Mohamed Aktar Bin Mohd Sapuan, DLSM. (2019). “Key Factors to Consider for a Smart Warehouse”. Retrieved from https://publication.sipmm.edu.sg/key-factors-consider-smart-warehouse/, accessed 18/09/2021.
Deng Hao David, DLSM. (2021). “Key Success Factors for Implementing an ASRS System”. Retrieved from https://publication.sipmm.edu.sg/key-success-factors-implementing-an-asrs-system/, accessed 18/09/2021.
Cheng Heng Yee, DLSM. (2021). “Key Considerations for Effective Warehouse Operations”. Retrieved from https://publication.sipmm.edu.sg/key-considerations-effective-warehouse-operations/, accessed 18/09/2021.
Ed Romaine. (2020). “Types and Applications of Autonomous Mobile Robots (AMRs)”. Retrieved fromhttps://www.conveyco.com/types-and-applications-of-amrs/, accessed 18/09/2021.
Chris Benevides. (2020). “The Advantages and Disadvantages of Automated Guided Vehicles (AGVs)”. Retrieved from https://www.conveyco.com/advantages-disadvantages-automated-guided-vehicles-agvs/, accessed 18/09/2021.
Fergal Glynn. (2018). “What is automated warehouse picking?” Retrieved from https://6river.com/what-is-automated-warehouse-picking/, accessed 18/09/2021.
Megan Nichols. (2020). “Benefits of Automated Packaging Lines.” Retrieved from https://www.packagingdigest.com/automation/5-benefits-automated-packaging-lines/, accessed 18/09/2021.