The role of storage installations has evolved over time and they have become strategic factors in the success of many businesses. Warehouses are no longer merely places for storing products; they are now focused on providing service and support facilities to companies of all kinds. To fulfil this new role, they must be properly designed, with a design project that compiles as much information as possible, so that the installation fulfils its function and can even adapt to any future needs that may arise.
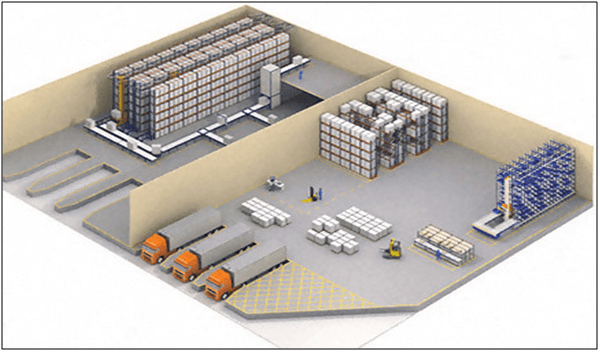
Few factors should be considered when designing or laying out any storage or distribution facility. Be it a large multi temperature composite distribution centre servicing a high market network, a spare parts store in mobile service centre, or raw materials store supporting a manufacturing operation.
The basic factors can be easily remembered using the pneumonic FAST or fast standing for F-Flow, A-Accessibility, S-space, and T- Throughput. These are not in any order of priority. Each is as important as the other and your aim is to obtain the best compromise of these often-conflicting influences. As one factor is considered and altered, each of the other should be revisited to see what is the impact of that change on the whole process.
Table of Contents
Flow Consideration
What we’re looking for here is a logical sequence of operations within the warehouse where each activities located as close as possible to that which precedes it and also the function that follows it. We are concerned with the controlled and uninterrupted movement of materials, people and traffic with, if possible, no cross-flow clashes or areas of high traffic or work density. It is also concerned with the awareness of where material is located within the system, and the status and location in the storage and handling equipment and medium. Our aim is to site and position the various warehouse activities in order to contribute to a smooth flow of operations with a minimum amount of movement and disruption.
Accessibility Consideration
In order for your operation to be as efficient as possible, your new facility must take accessibility of product into consideration. Specifically, how will product be accessed, handled, and transported? Certain questions to keep in mind that will help you frame your thinking around this include:
o Is inventory stored on a short-term or long-term basis, or a combination thereof?
o Is product handled primarily by pallet, case, tote, or individual units?
o Is it necessary to segregate inventory into individual lots and batches?
o How product is currently picked and processed into orders?
Questions around accessibility are important because it will impact the storage/inventory strategies you ultimately choose to implement as well as the specific technologies that you leverage.
Space Consideration
When considering how to use the available space, the maximum should be allocated to operational storage and stock processing purposes. And the minimum space given up for associated functions such as offices, working areas, empty pallets storage, battery charging, etc.
Today’s wide range of storage media available on the market allows us to make optimum use of a cubic capacity of the available space, not just the floor area. As most of this equipment is free-standing and requires no structural support from the building itself, it means that the building can be of the simplest and cheapest big box design. It also allows us to build in flexibility to the operation by selecting the storage media to meet the current stock profile and then change it as the operation evolves to meet future requirements.
This can be done without expensive and disruptive changes to the actual building. But remember, you still have to consider flow accessibility.
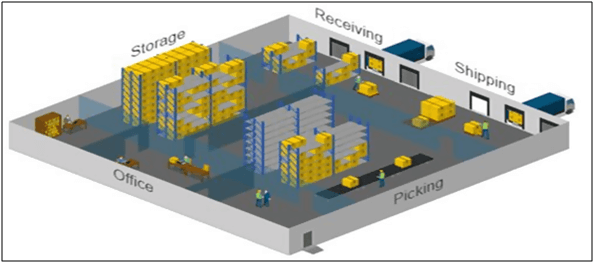
Throughput Consideration
When we look at throughput, where not only looking at the categories of product parting through the warehouse but also the nature of the product and its velocity through the flow. By nature, we mean the handling characteristics, dimensions and any other factors that will impact on how it is moved through the flow such as hazard, bulk, fragility, security requirements and compatibility with other products.
The velocity of the product will consider the volumes moving through the warehouse on a daily basis. Pick period activities need to be determined as do minimum activity levels. A high degree of availability of accurate throughput data will assist greatly in the outcome of the design or layout exercise. The better the data and the longest spent on collecting and analysing it, the less the risk, however it is still possible to come up with an acceptable solution when one does not have the luxury of accurate data going back into history.
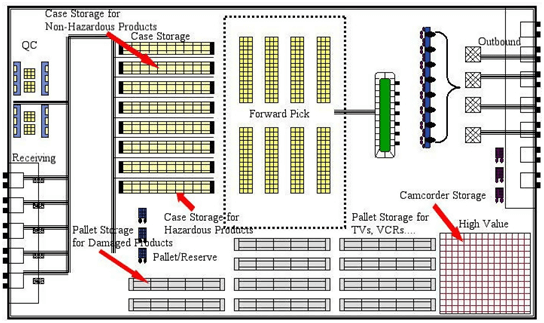
Product Specification Consideration
To determine the most appropriate technologies and processes to implement in your new facility, it is critical to have a firm understanding of your products’ specifications. What, exactly, needs to be handled? What characteristics of that product might impact how it gets handled?
Size, fragility, weight, weight distribution, and other factors are all important considerations, especially when it comes time to select inventory solutions and handling systems.
Questions to be answered with regard to inventory and handling include:
o How will product be stored?
o How might product specifications limit or impact inventory options?
o Do different products have different storage requirements?
o Where is the product’s centre of gravity, and how might this impact the conveyors, sorters, and gap generation technologies used?
o How much does a typical tote/case/pallet of product weigh, and how will this impact the technologies selected?
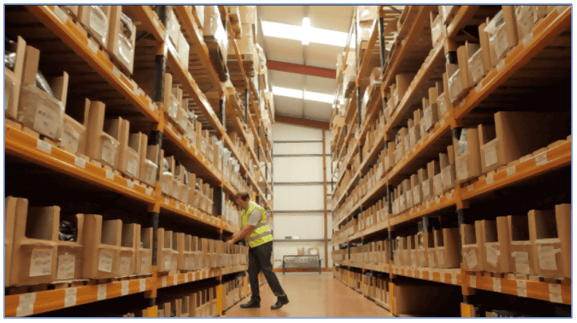
Financial and Other Considerations
The main step is to consider the amount of money before you start with the warehouse design. Once the budget is made you can do the planning of the construction. Some of the designs are more expensive than others so you have to consider several factors.
It is important that you comply with state regulations and the guaranteed safety in the work environment.The site details must be according to the characteristics of the place and will define the final design of warehouse. Including other factors such as topography, drainage and soil condition as it should be designed with a raised floor to protect the materials
There is also the need to minimize movement such as reduce walking around a warehouse as high chances of mistake occur when a person is regardless physically or mentally tired. By decreasing the amount of movement will aid in faster and more accurate picking.
Warehouse layout and design is another factor which aids maximizing efficiency, order accuracy and increase productivity of a warehouse. To minimize the walking made by employees. Your storage and pick strategies will have direct effect on this. Instead of using manual picking and random storage strategy, switching to a zone-based picking system and volume or class-based storage systems can allow you to minimize trips.
Conclusion
Warehouse plays a crucial rule in integrated supply chain operation and make a positive contribution. The appropriate operations function in a warehouse not only improve customer service, but also bring profit as well. To ensure perfect operation of a warehouse, a good layout planning and work flow should be implement.
References
Ed Romaine. (2018) “Top 5 Considerations When Building a New Warehouse or DC”. Retrieved from https://www.conveyco.com/considerations-for-building-new-warehouse, accessed 15/09/2019.
Jatnnapr. (2017). “FACTORS TO CONSIDER IN WAREHOUSE LAYOUT DESIGN”. Retrieved from https://logisticsmgepsupv.wordpress.com/2017/05/15/factors-to-consider-in-warehouse-layout-design, accessed 15/09/2019.
Lim Yoon Chin, DLSM. (2018). “Techniques of Order Picking for Warehouse Productivity”. Retrieved from SIPMM: https://publication.sipmm.edu.sg/techniques-order-picking-warehouse-productivity/, accessed 15/09/2019
Mecalux. (2019). “Warehouse design and layout: 6 basic factors”. Retrieved from https://www.mecalux.com/logistics-items/warehouse-design-and-layout-6-basic-factors, accessed 15/09/2019.
Prashant Dedhia. (2017). “Warehouse Design – Key Factors to Consider and the 7 Principles of Warehouse and Distribution Centre Design”. Retrieved from https://www.linkedin.com/pulse/warehouse-design-key-factors-consider-7-principles-centre-dedhia, accessed 15/09/2019.
Syed Muhamad Faizal, DLSM. (2018). “The Five Essential Methods for an Efficient Warehouse Operation”. Retrieved from SIPMM: https://publication.sipmm.edu.sg/five-essential-methods-efficient-warehouse-operation, accessed 15/09/2019.