Reverse logistics is the entire process from logistics planning, implementing, controlling the efficient, cost effective flow of raw materials, pre-fabricates, parts, components, integrated objects till the final products and related information from consumption back to origin. It is the activity that carried out after sold out the product in order to recover its functionality or value and refresh its shelf life. It is the opposite of the standard supply chain which allows goods from customers back to the sellers or manufacturers for maintenance, refurbishment, services and recycle. This article discusses the key factors to overcome challenges in implementing reverse logistics.
Reverse logistics can be more profitable and sustainable with proper logistics planning, implementing, controlling, management and execution. However, it is not easy to manage a good reverse logistics management system in an organization as there are many challenges need to improve and overcome in order to gain the greatest profit and reach the customer’s success.
Table of Contents
Organisation of Returns Process
Return process starts with the end customer who wishes to return the product where move backwards through across the key members in supply chain management to the distributor or from distributor to manufacturer. If customer was unhappy after received product or there is defect with the product, they might request a return or refund from supplier, distributor or manufacturer. The Supply Chain will arrange transportation to pick up the product from customer if their request has been approved by company. The warehouse or sorting facility will start to do the necessary inspection or quality check and restock the product and put pack the product in inventory once the product is ready for reuse or re-sell. Eventually the product will deliver to customer if it is ready for re-sell or can be sold to a future customer.
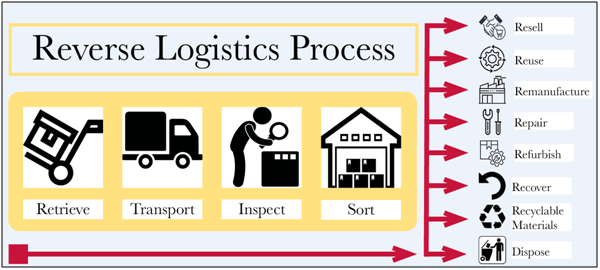
Organizations implementing the return process can reduce their waste and cost, accessible to customer, create a more sustainable supply chain, improve overall corporate citizenship and help company achieve business sustainability.
Reducing Cost of Reverse Logistics
There are number of ways to cut costs with reverse logistics, like reduce transportation cost, handling cost, inventory cost and labour cost. Here are some ways to help in reducing costs of reverse logistics. Generally, a third-party provider whose sole business is to manage reverse logistics. They can manage this process much cheaper than the organisation who try to do it internally. One of the common uses for returned products is internal use. Usually it can cost a company less to repair a product for internal use compare with recycling.
As recycling is an expensive process that requires strict compliance to ensure safety and proper disposal of recycled item. A defective product can lead to a poor experience with the company and a poor reverse logistic handling could directly affect how customers feel about the company brand. Losing customers is a significant cost for any business. Managing the reverse logistics process and providing an excellent shopping experience for customers, will increase the customer overall experiences and helps to create goodwill with the customer and ultimately prevent the loss of the customer.
Rationalising the Returns of Products
Rationalization is a process that most organizations considers. That is because it helps organization to reduce the costs, maximize profits, create the maximum number of customers with the minimum number of products in order to maximize the revenue for each product. It aimed at improving efficiency, transparency and governance, getting rid of waste, smooth standardizing processes, in order to boost the bottom line and maintain the sustainability of company. In order to have product rationalization, first of foremost is get every order right in first place. At the customer’s first buy, to make sure the correct product with an original receipt is given to customer. The correct information or product manual has been provided to customer and explain or demonstrate on how to use the products. Secondly, we must have better understanding on why customer is returning the product, allow customers to read and give honest reviews for returned products in order to decrease the percentage of returns with minimal amount. Lastly, improve and overcome. Every return process needs to be recorded for evaluation. This is due to each return will need to analysis and find the root cause with solution to prevent for the reoccurrences. This is helping the company to improve product quality and maintain the company reputation and professional image.
Poor Visibility into Products Received
Poor visibility into products received may cause difficulty in handing reverse logistic as it may lack of traceability and timing consuming in the whole process. In order to increase the visibility into product received and enhance the customer experience when dealing the reverse logistic. Here are some good practices are encouraged during the process. Firstly, maintain the purchase record in system and maintain the traceability of original purchase data. A simple way is to install a system to handle orders, pick, pack, despatch and shipping. As a result, it will deliver the high efficiency in handing poor visible products. Second, inspect the products and add return labels on the original packaging after any type of reverse logistics activities had carried out. This is helping the staffs to recognise the original product and returned product easily. Third, have clear return policies. Have a standardized regulations and policy for returned product to reduce the risk of poor visibility into products received.
Inadequate Capacity to Manage Returns
As business grows while the level of customer demand increases, there are many
organizations may find that they do not have enough capacity to manage returned
product. In this case, it’s best to use a fulfilment center. As a good fulfilment center not only understand the proper way to pack a product, use the best courier services to expedite the shipping but also can handle reverse logistics support such as product returns efficiently. They will ship the replacement products to customers and answer customer questions. They could cope with the return logistics efficiently and professionally. The other way is to outsource reverse logistics.
By outsourcing reverse logistics to a partner whose sole is to manage the reverse logistics. As they offer a lower cost compare with the organization who handle it internally. Moreover, outsourcing of logistics help to settle the warehouses spaces, technologies, employees and the safety measures. Investing in the right technology also helps to improve the capacity of manage returns. It drives work improvement such as robots are helping on heavy duties, sorting, tracking and monitoring each delivery. Robotic automation in reverse logistics with potential to reduce cost and improve efficiency and capacity in the whole reverse logistic processes.
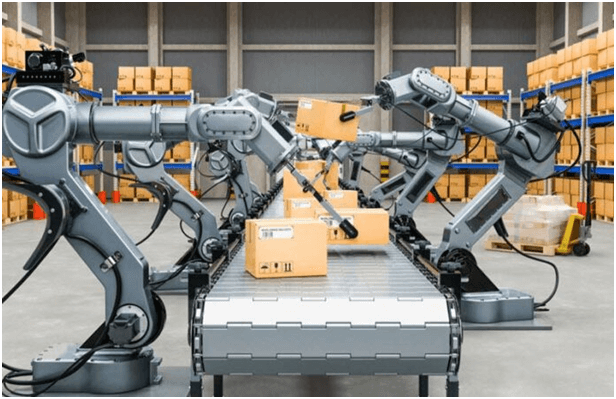
Partnership with Dealers and Contractors
Some complicated revere logistics may need to further extend to their third parties like suppliers, contractors, subcontractors or distributors which are beyond a company’s own service in their organizations. Any kind of supports need to have the contract which state clearly of the roles and responsibilities of each party. All the agreements should be available to review in digital forms at any time. These agreements define what happens when items are returned for certain reasons such as defects.
With the necessary contract agreement in place, close collaboration with suppliers, dealers and contractors is crucial as it can be the great help to ensure a smooth, integrated experience for customers as a whole, not a disjointed one they will struggle to navigate. Closed collaboration, mature relationships and partnership like every aspect of the integrated supply chain, it has grown increasingly complex. To achieve a competitive advantage for the organization, it is important that you approach suppliers, dealers and contractors proactively as a strategic, systematic, cross-functional and cross-enterprise process. By establishing the active collaborative relationship with suppliers, dealers and contractors. It will beyond pure transaction management to a networked, mutually beneficial partnership.
Efficient Repair Process
Implementing inventory software could help to improve the efficiency of repair process. As the sophisticated software could track all the items at different stage during the whole process. A fixed product still be able to sell which helps company cut down on the wastage. Some drawings or learning software are also can help in streamlining the repair process by analysing the problems and recommending the solutions. Software can provide a short video or tutorial to demonstrate on how the repair work need to be performed. Ideal software can accelerate the learning curve on repairing the item.
Partnering with logistics providers, repair services providers can be the great help to keep customers’ perspectives always at the forefront of its customer satisfaction strategy. A professional services partner always provides deep knowledge of the technologies and design methodologies, helping the organizations to implement a best-practices repair services process that carries it into the future as well as an analysis program to perform root cause analysis to make the ongoing product quality improvements. This also allows the organizations to extend its global footprint moving forward and seamlessly provide customers with prompt repairs and astute customer service.
Conclusion
It will provide liberal return policies, agreements to customers, earning their utmost trust, recurring the business with new opportunities, and a new avenue for optimizing reverse logistics. Reverse logistics plays an important role in every organization. Selecting the right technology is helping to overcome all the challenges in reverse logistic. With the right technology could help to facilitate whole process for organization and customers. A good set up of reverse logistic not only to meet customer’s expectation but also help the organization to save the operation cost, increase asset utilization, reduce the losses and unplanned revenue, improve environmental sustainability, reduce the human resources and maximum the profits for the organization.
References
Chris Lee. (2019) “45 Things You Should Know About Reverse Logistics” Retrieved from https://www.warehouseanywhere.com/resources/45-things-about- reverse-logistics/, accessed 18/09/2021.
Hadleigh Reid.(2013) “Reverse Logistics: What is it and How do you Manage it?” Retrieved from https://dclcorp.com/blog/fulfillment/common-reverse-logistics-costs/,accessed 18/09/2021
Ho Kek Ming, DLSM. (2019) “Six Essential Areas for an Integrated Logistics System”. Retrieved from SIPMM: https://publication.sipmm.edu.sg/six-essential-areas-integrated-logistics-system/, accessed 18/09/2021.
Johannes Beekman. (2019) “How to Overcome Reverse Logistics Challenges” Retrieved from https://iotmktg.com/how-to-overcome-reverse-logistics-challenges/,accessed 18/09/2021.
Robert Victor. (2017) “Reverse Logistics: Why Your Company Should Outsource” Retrieved from https://www.hollingsworthllc.com/business-units/reverse-logistics/ , accessed 18/09/2021.
Sunny Chaudhary, DPSM. (2019) “Key Considerations for Reverse Logistics of
Agricultural Products”. Retrieved from SIPMM: https://publication.sipmm.edu.sg/key-considerations-reverse-logistics-agricultural-products/, accessed 18/09/2021.
Theresa Pang Kim Lian, DLSM. (2019) “Key Considerations for Reverse Logistics
Operations”. Retrieved from SIPMM: https://publication.sipmm.edu.sg/key-considerations-reverse-logistics-operations/, accessed 18/09/2021.
Winnie Teh Cheng Hoon, DLSM. (2021) “Evaluating Lean Performance for
Reverse Logistics”. Retrieved from SIPMM: https://publication.sipmm.edu.sg/evaluating-lean-performance-reverse-logistics/, accessed 18/09/2021.