Optimizing manufacturing inventory is essential for efficient operations and cost reduction in the manufacturing sector. By employing various techniques, businesses can streamline inventory management and meet customer demands effectively. Accurate demand forecasting helps align production and inventory levels, while just-in-time (JIT) inventory minimizes holding costs. Collaborative Planning, Forecasting, and Replenishment (CPFR) enable improved demand forecasting and supply chain visibility. Material Requirements Planning (MRP) utilizes demand forecasts and bills of materials to schedule procurement or production, reducing stockouts and excess inventory. Collaborating with suppliers ensures timely deliveries and favourable terms. Accurate inventory tracking and continuous improvement enhance efficiency. Real-time inventory tracking provides visibility into inventory levels and movements, continuous monitoring and data analysis to improve demand forecasting accuracy and lead time optimization. Implementing these techniques enables manufacturers to gain better control over inventory, optimize production planning, minimize costs, and meet customer expectations.
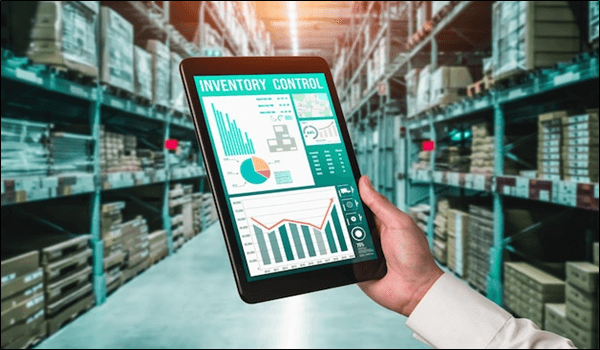
Table of Contents
Demand Forecasting with CPFR
CPFR, or Collaborative Planning, Forecasting, and Replenishment, is an optimization technique for demand forecasting in manufacturing inventory. It emphasizes collaboration and information sharing between trading partners, such as manufacturers, distributors, and retailers, to improve demand forecasting accuracy and inventory management. CPFR optimizes demand forecasting in manufacturing inventory by leveraging collective intelligence, aligning planning activities, and enhancing supply chain collaboration. This technique helps address the bullwhip effect, where small fluctuations in customer demand can lead to amplified inventory fluctuations upstream. By sharing information and jointly planning, CPFR minimizes forecast inaccuracies, reduces inventory holding costs, improves customer service levels, and enhances overall supply chain efficiency. Overall, CPFR enables manufacturers to achieve better demand forecasting accuracy and optimize inventory management through collaboration, information sharing, and coordinated replenishment, resulting in improved operational performance and customer satisfaction.
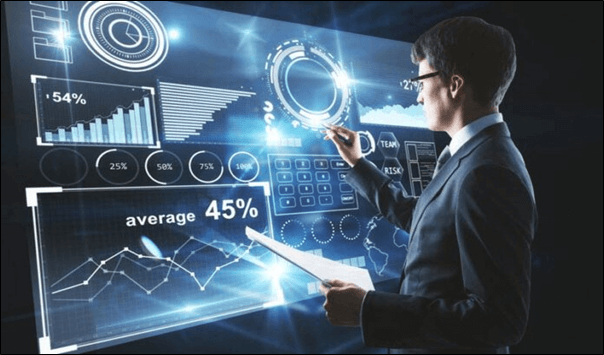
Material Requirement Planning (MRP)
The MRP system is effective for optimizing manufacturing inventory because it enables accurate demand planning, effective production scheduling, and minimization of stock-outs. By utilizing demand forecasts and customer orders, MRP ensures that suitable materials are available at the right time, avoiding overstocking and under-stocking scenarios. Considering lead times and efficient production scheduling helps minimize production delays and idle time. MRP’s ability to identify potential shortages and generate timely purchase or production orders helps prevent stock-outs and ensures smooth operations. MRP enhances inventory optimization by aligning production with demand, reducing carrying costs, and improving overall supply chain efficiency.
Just-in-Time (JIT) and Kanban systems
JIT and Kanban systems work together to optimize manufacturing inventory, minimize waste, improve productivity, and enhance overall efficiency. JIT focuses on producing and delivering goods precisely when needed, eliminating excess inventory, and reducing carrying costs. This approach aligns production with customer demand, resulting in faster turnaround times, reduced lead times, and improved responsiveness. On the other hand, Kanban is a visual signaling system that ensures smooth material flow and control throughout the production process. It utilizes visual cues like cards or electronic signals to indicate when materials or components need replenishment at each production stage. Kanban prevents overproduction, optimizes inventory levels, and supports Just-in-Time manufacturing by maintaining a pull-based system that produces only what is necessary, precisely when needed. By implementing JIT and Kanban systems, manufacturers can eliminate waste, reduce inventory, improve production flow, maintain high-quality standards, and achieve enhanced efficiency and customer satisfaction.
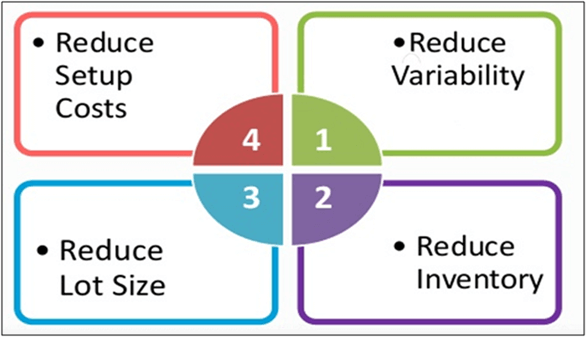
Batch Size Optimization
Batch size optimization is a critical strategy for optimizing manufacturing inventory. Manufacturers can minimize setup costs by determining the optimal production batch size while reducing inventory carrying costs. Smaller, more frequent batches help reduce setup time and resources, resulting in cost savings. Additionally, optimized batch sizes ensure inventory levels align with demand, reducing storage costs and obsolescence risks and freeing up working capital. This approach enhances production flexibility, allowing manufacturers to respond quickly to market changes and customer preferences. Ultimately, batch size optimization improves operational efficiency, minimizes inventory waste, and enhances overall inventory management in manufacturing.
Inventory Segmentation with ABC Analysis
Inventory segmentation, specifically through the ABC analysis technique, optimizes manufacturing inventory by providing a structured approach to prioritize and allocate resources effectively. Manufacturers can tailor inventory management strategies by categorizing inventory items into A, B, and C categories based on their value or importance. High-value or high-demand Category A items receive closer attention, tighter control, and faster replenishment to prevent stock outs and meet customer demands. Category B items with moderate value or demand receive intermediate management efforts. Category C items, representing lower-value or low-demand products, are managed with looser control to minimize carrying costs. This segmentation approach ensures that inventory management efforts are aligned with each item’s specific characteristics and importance, ultimately improving operational efficiency, reducing costs, and optimizing overall manufacturing inventory performance.
The full content is only visible to SIPMM members
Already a member? Please Login to continue reading.