In the construction industry, warehousing management plays a vital role. Warehouses are commercial buildings where goods, raw materials and equipment are stored by the supply chain until the time customers receive it. When involving logistical system designs, warehouses are not only storerooms but also takes roles in providing services and supporting facilities to companies. Warehousing with logistical system designs focuses more on transaction dominance from storage dominance. By consolidating the movement, an effective warehousing is able to reduce the costs of transportation.
Construction companies can take advantage of break-bulk and cross-dock especially when ordering the raw materials which are large and heavy through economical transportation. Effective warehousing will also be one of the solutions to reduce the risk of injury on site which is mostly caused by inappropriate storage and poor site management. According to Health and Safety Law, everyone working on site will be dangerous if the site is not clean and safe. Therefore, warehousing is important for construction in many aspects and this article discusses several key factors for effective construction warehousing.
Table of Contents
Well-planned Warehouse Layout
A well planned internal and external warehouse layout helps to build effective construction warehousing. It is important to maximize the efficiency of both internal and external warehouse layout to avoid the bottlenecks which will affect the warehouse productivity in the future. To have a well-planned layout, there are some factors that need to be considered.
- Future storage requirement – It is the key factor to look out for the warehouse layout. Companies have to roughly forecast the stocks which will be put inside the warehouse by checking the stocks profiles and the access requirements to reduce the unsuitability in the future.
- Adaptability – Warehouses have to be designed to accommodate changes easily in the future to avoid hassle. Although companies forecast the stock profiles and requirements, there will still be some changes especially when the sales quantity increases or the size of the products changes. At that point of time, companies may need more space or different types of storage for the changes.
- Flow of warehouse – Before building a new warehouse, companies should decide the best warehouse system which is the most suitable for the operations.
- Types of racking – The types, size and format of storage and pallet racking depends on the stored products. Thus, companies have to consider the requirements carefully. The common practice is building the warehouses from the inside-out to avoid insufficient storage spaces and other facilities in the future.
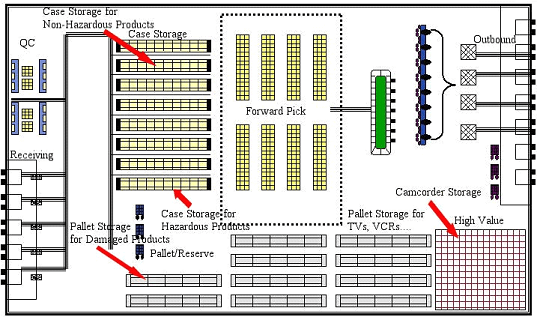
https://publication.sipmm.edu.sg/five-essential-methods-efficient-warehouse-operation/
Regular Cycle Counting
Different from the traditional physical count for the inventory, inventory cycle count is an alternate way which is able to reduce the workforces involved and the potential error. Inventory cycle counts break the counting process into different parts to carry out during different periods. Also, it will use sampling methods which means that only some samples are taken to be checked and expanded to encompass the whole. Although traditional physical count is easier, it will involve more manpower and time to carry out the inventory counting. Inventory cycle counting is a more manageable approach which can have more frequent counts to always have an updated inventory records in order to avoid the situations with products out-of-stock when required.
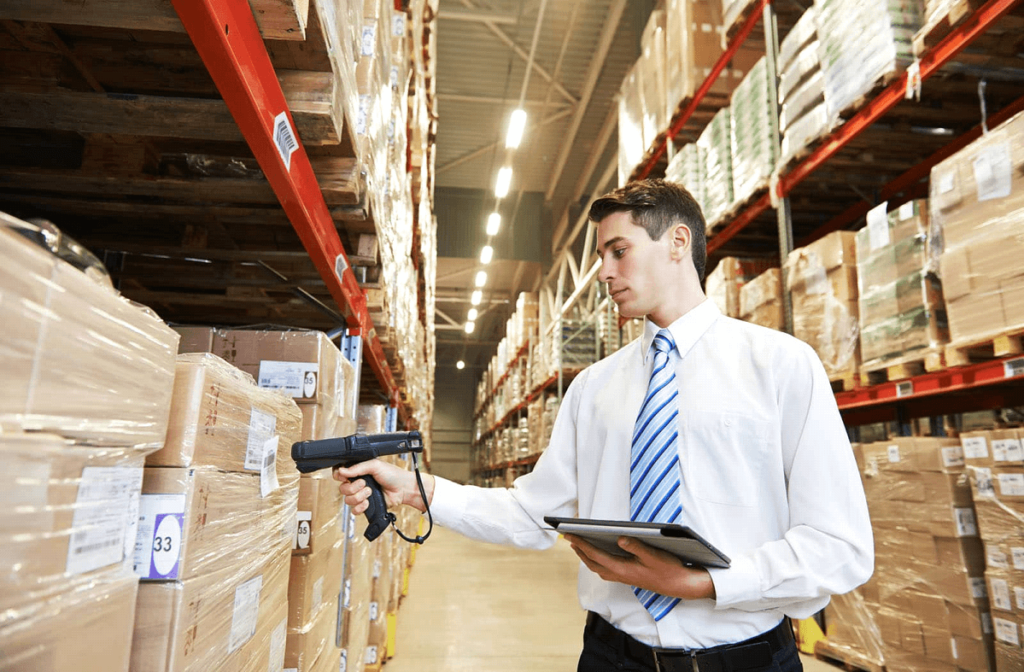
http://www.multiplast43.com/wp-content/uploads/2019/02/1_YVGdpcWPEWjK_j_p9I4gwQ.jpeg
Optimized Receiving Process
When shipments arrive, the warehouses will go through a standard receiving process to store the inventory. An optimized receiving process is able to ensure that the process is smooth and reduce the error as much as possible.
Firstly, the correct metrics should be compiled including the errors reports, total time taken to move materials from system to usability, dock utilization and supplier shipping issues. Before receiving the shipments, companies should check the packaging requirements and details for suppliers and shippers carefully to increase the efficiency. As labour is the highest warehouse cost, it is important to allocate the manpower wisely to maximize their working utility. When the delivery truck arrives, inventory clerks who are properly trained will do the shipment identification before signing the shipping notice and accept the shipment. Then, product count and inspection are important to ensure that the products received are tally with the invoice slips and in good condition. Before stocking the products in the warehouses, it is important to assign them the inventory numbers and label them correctly. When conducting the replenishment process, companies should leave room for the error in case of receiving defective products or errors of miscounting. Lastly, an optimized receiving process will end with proper inspection for outgoing products to catch the defective products before customers’ hands.
The full content is only visible to SIPMM members
Already a member? Please Login to continue reading.