Lean six sigma is a process improvement methodology that uses facts, data and statistical analysis for improving quality, productivity, profitability and market competitiveness for any corporation. Lean six sigma helps to achieve supply chain efficiency and effectiveness by delivering goods and services at the lowest cost by having the right inventory processes on hand, easily accessible to customers to ensure that they leave the business premises happily.
Customer satisfaction may result in increased revenue and creates better coordination between vendors and business partners alike. Lean is about speed, flow and the elimination of waste. Six Sigma focuses on reducing variation from the process, statistically speaking, six sigma is an understanding of 3.4 defects per million opportunities. It is about to mean and specification limits, how many sigma (standard deviation) you can fit between data, mean and specification limits to determine what sigma level procedures a company operating upon.
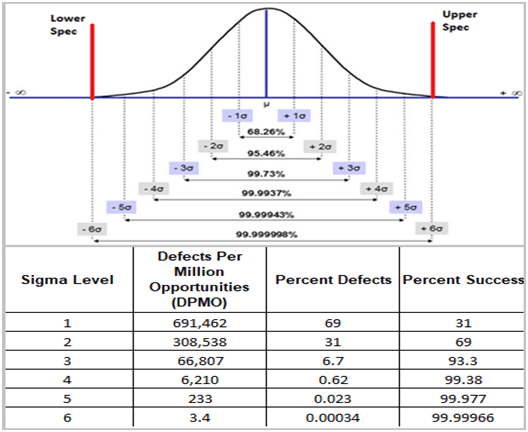
Table of Contents
Improving Supply Chain Efficiency
Companies round the world are striving to find supply chain efficiency to improve their bottom lines. Organizations can benefit from the lean supply chain principle to implement flow, pulls system and continuous replenishment. Continuous flow in the supply chain can be achieved through reducing unnecessary activities from the processes which ensure delivery of goods and services to customers at the right place and time to satisfy demand, at the lowest cost within the shortest lead time. Pull systems, being agile, faster and predictable are based on the demand such as the Just-in-Time (JIT) model, where deliverables are produced to meet actual demands and avoid overstocking. The continuous replenishment allows companies to stock facilities with the exact amount of inventory requisites to meet expected demands.
A lean supply chain focuses on value for customers while identifying and eliminating waste. The value-added activity that changes the form, function and service of the product is tailored such that a customer willingly pays for this change. The non-value added activity can be referred to as, Type I: tasks that are essential or required by process, e.g. inspection of products, though non-value added activity, are required to ensure that defective items do not pass on to customers. Type II: tasks that are not essential and customers are not willing to pay for it. This so-called waste can be categorized in 7 types and should be eliminated from the process.
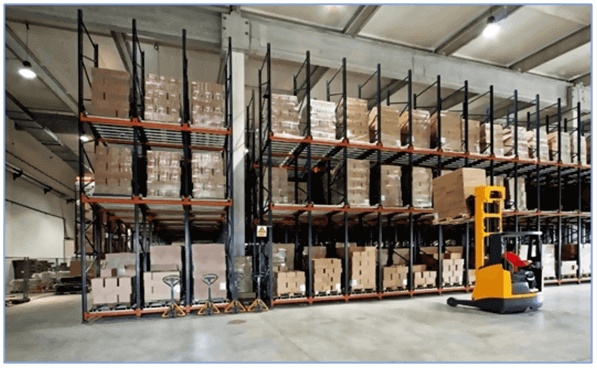
Elimination of Seven Wastes
1. Transportation
Unnecessary movement of personnel causes exhaustion, inventory and equipment could result in damage, deterioration and additional costs.
2. Inventory
Materials and information held longer than required, e.g. unread emails, overstocked raw materials and WIP, etc.
3.Motion
Excessive movements may include unnecessary office meetings and bending, stretching, walking and carrying loads at the plant.
4. Waiting
It is less visible than other wastes that cause delays or stoppages, e.g. waiting for instructions/information and waiting for forklift.
5. Overproduction
It is called the mother of all wastes as it occurs when a product, produced too fast at the wrong time or too much in quantity for the process, e.g. printing paperwork before it is required.
6. Over-processing
Unnecessary activities that use more resources such as space, energy or personnel, e.g. too many approvals or redundant work such as duplicating information.
7. Defect
Additional tasks performed on products or services caused by incomplete information or incorrect standard specifications, lacking of skills/training and error.
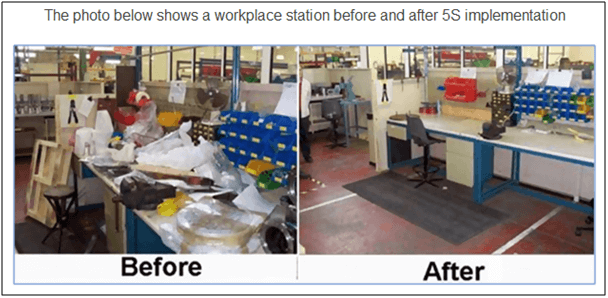
The Principles of Lean
• Kaizen
It is a continuous improvement strategy that focuses on better ideas involving every aspect of an organization.
• 5S System
5S (Sort, Set in order, Shine, Standardize and Sustain) is a strategy to improve the overall function of a business. By improving housekeeping, organizing and ensuring cleanliness at the workplace.
• Poka-yoke (Mistake Proofing)
Poka-yoke is a mistake-proofing approach, using automatic devices or methods to avoid simple human errors and defects.
• Value Stream Mapping
It helps to understand the steps taken during the process, from product manufacturing to delivery to end customers. The aim is to understand what the opportunities are to enhance process flow by eliminating waste.
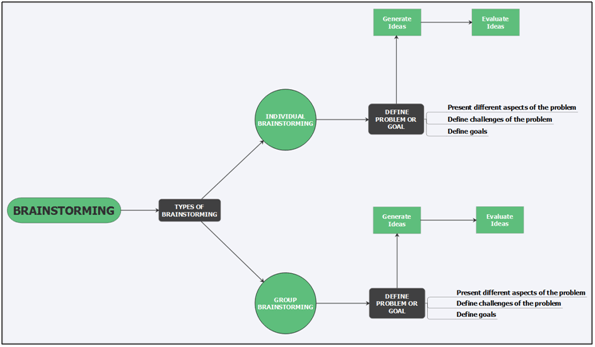
The Six Sigma Techniques
• Brainstorming
A problem-solving technique in which an individual or a group generates new ideas as a potential solution for a problem and implementation after total evaluation of the input of such ideas.
• Root Cause Analysis &The 5 Why’s
The aim of this step is to identify the root causes of such problems by constantly questioning, “Why” repeatedly, e.g. we must question why a part is broken, not just be satisfied knowing a part is broken.
• Voice of the Customer (VOC)
It is a technique of addressing customer expectations, needs and preferences. We use their feedback, market research, surveys, data reports, etc to gain customer trust, satisfaction and loyalty for improving the efficiency of all processes.
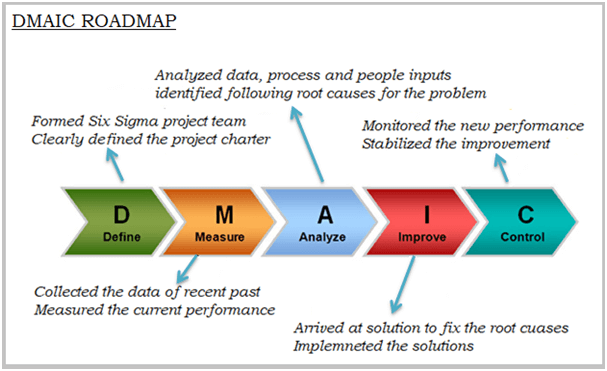
DMAIC, Five Phase Process
1. Define
In this phase, the project team outlines the project objective and the understanding of the process to be improved, also responsible to identify resources available to achieve the project’s goals.
The full content is only visible to SIPMM members
Already a member? Please Login to continue reading.
References
Balagura Patmanathan, DLSM. (2018). “The Five Essential Techniques for Effective Warehousing”. Retrieved from SIPMM: https://publication.sipmm.edu.sg/the-five-essential-techniques-for-effective-warehousing/, accessed 06/09/2019.
iMind. (2019). “Defining Brainstorming”. Retrieved from https://www.imindq.com/uses/brainstorming, accessed 10/09/2019.
Kai Nexus. (2019). “The 7 Wastes of Lean”. Retrieved from https://www.kainexus.com/improvement-disciplines/lean/7-wastes-of-lean, accessed 06/09/2019.
Kumerendren Vijayakaran, DLSM. (2019). “Seven Order Picking Techniques for Distribution Centers”. Retrieved from SIPMM: https://publication.sipmm.edu.sg/seven-order-picking-techniques-distribution-centers/, accessed 10/09/2019.
Pankaj Kumar. (2019). “The Six Sigma Process of Business Transformation”. Retrieved from https://www.simplilearn.com/what-is-six-sigma-a-complete-overview-article, accessed 03/09/2019.
Selby Jennings. (2017).“Using Six Sigma to Maximize Supply Chain Efficiency Through S&OP Processes”. Retrieved from https://www.phaidoninternational.com/industryinsights/using-six-sigma-to-maximize-supply-chain-efficiency-through-s-and-op-85221152536, accessed 05/09/2019.
Six Sigma Institute. (2019).“Six Sigma DMAIC Process”. Retrieved from https://www.sixsigma-institute.org/What_Is_Six_Sigma.php, accessed 10/09/2019.