A third-party logistics provider offer various outsourcing services such as warehousing, transportation, procurement, value-added services and to certain execution scope. Technology integration is also a ‘must have’ to enhance the entire service level. Outsourcing business model meeting customer’s expectation through cost –efficiency, increase productivity, flexibility, scalability, and economies of scale, meeting delivery dateline and technologies. The pictograph below shows using technologies with combination of machine learning across supply chain operations. Efficiently in optimizing the inventory turn and increase operations efficiency and achieve responsiveness to customers.
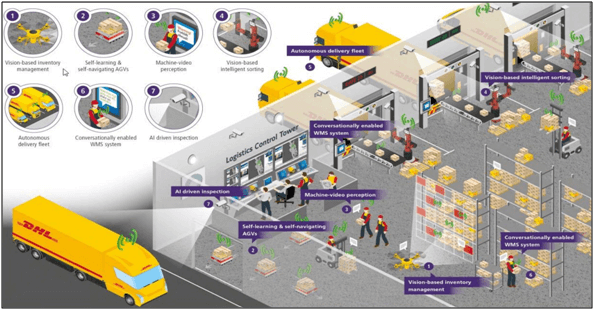
Table of Contents
Expectation on Outsourcing Benefits
A 3PL with integrated services increase their flexibility to adjust to customer’s expectation and to be cost effective. Key benefits are as follows:
• End-to-End Visibility increase connectivity throughout the entire flow with IT centralising operational data. It can helps in achieving significant increase in cross-operational visibility such as inventory health, delivery status, order status and etc.
• Flexibility helps to smooth out the day-to-day operations functions and react to unforeseen disruption. 3PL has the capability to leverage on their expertise and resources for any changes.
• Reduced Waste is another benefit on working together to cut down the effort and redundant processes such as a consoled shipment in FTL instead of 2 LTL from two different department to a same designation.
• Data Centralization improve the workflows by advanced analyse. It also helps in increasing the overall efficiency of the value chain.
• Improved Margins through increase of efficiency, reduce wastage, improved performance with satisfied customers.
Expectation on Warehouse Operations
Customers have high expectation on 3PL’s fulfilling their day-to-day operations by meeting measurable Key Performance covering important area as such receiving, organization, fulfilment, distribution, reverse logistics, value added services, cross dock, optimising storage and etc. Assisting customer on identifying key areas can make improvement, better productivities, reduce operations cost and delivery on time.
These key areas include the following:
• Receiving Efficiency can involve in accuracy, multiple new stock receive each week, customer return of good and defective unit and stock return. Tracked and measured by paying attention on the time taken receive till cargo put away.
• Picking Accuracy in a warehouse can consider a complex activities. Picking wrong parts or quantity can cause a significant impact on return items and huge costs. Creating appropriate warehousing racking and shelving will improve picker’s efficiency, productivity and reduce hassle. Picking accuracy can measure from “rate of return” KPI and “total order number”.
• Carrying Cost of Inventory tracking can help customer see the profit current stock will truly bring. It’s can also furnish a more accurate demand forecast and put in place a more suitable inventory control methods. Carrying cost of inventory consists adding the insurance, taxes, storage space, personnel equipment; all costs associated with storing inventory.
• Inventory Turnover ties closely with carrying cost of inventory. Providing this key performance data helps Customer has the visibility on how quickly their inventory sell and ship stock from the day inventory storage in warehouse. The fastest turnaround has less storage cost which customer make more profit. This can also help customer to gauge future buying practices and put in place inventory reduction strategies. 3PL’s Warehouse Management System (WMS) place an important roles to generate relevant reports.
• Rate of Return measure the end customer’s satisfaction. 3PL has assist customer on compile the reason of return and propose the strategies to resolve. It’s easier to rectify internal warehouse related issue such as wrong or damage cargo delivered.
• Backorder Rate allows in-depth deep analysis of forecasting success. Its measure the shortage of require stock and unexpected stock surge. Continually high stock out reflect the poor planning and forecasting. Constantly measure the inventory turnover will assist customer on improving their forecast ability.
• Order Lead Time is basically the average length of time the cargo takes from order release to warehouse till end customers to receive it. The lower the turnaround time (TAT) the better you have achieve on delivery KPI.
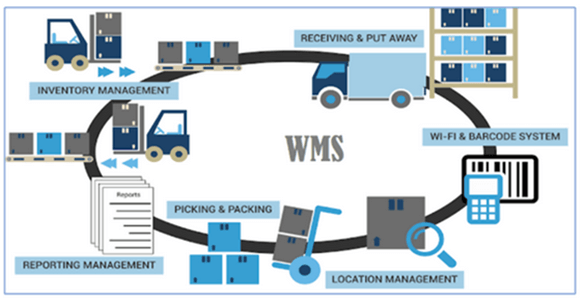
Performance Expectation on Partner Management
As a 3PL, sourcing of partners or managing on behalf are part of the Key performance expectation. Delivery is one of the activities require more focus due to the network complexity and pricing model (many hidden cost). 3PL can directly provide the services or engage or manage customer’s appointed provider. Shipping consist of local delivery, import and export.
Order visibility require connectivity between 3PL and shipper e.g Electronic Data Interchange (EDI), Electronic Air Waybill (e-AWB) and Application Programming Interface (API). Customer is expecting 3PL to provide full responsibility to control the entire shipping process. Automation through Transportation Management system (TMS) or Integrated Freight Management system can assist visibility on shipment REAL status e.g. Last Mile Delivery. Collecting and analysing freight data can help to avoid unnecessary cost, improve the TAT and end customer satisfaction.
Performance Expectation on Procurement Management
The benefit on Outsourcing procurement can bring down the overall procurement spend. Customer is expecting to see a lower cost from direct and indirect, maximizing the resources, augmented freight, better TAT performance, streamline and seamlessly integrate processes. Ultimately 3PL can help customer achieving their goal by freeing their time to focus on their own core competencies, reduce purchase cost and improve their relationship with their end customer. Procurement Analytics created a visualization dashboard through analysing the past, why, future and decision making.
Procurement 10 most important metrics and KPIs measure through Spend under Management, Spend vs budget, Total cost of ownership, Cost Savings, Cost avoidance, Average payment terms, Number of suppliers, Contract coverage, Exchange rate exposure and Vendor accountability.
The full content is only visible to SIPMM members
Already a member? Please Login to continue reading.
References
Brian Hoey (2019) “5 Benefits of Supply Chain Integration” Retrieved from https://blog.flexis.com/5-benefits-of-supply-chain-integration, accessed 29/11/2019.
Israel Pilapil, DLSM. (2019). “Crucial Technologies for Warehouse Efficiency”. Retrieved from SIPMM: https://publication.sipmm.edu.sg/crucial-technologies-warehouse-efficiency, accessed 09/12/2019.
Jasper Pickering. (2017).“Inside Alibaba Smart Warehouse”. Retrieved from https://www.businessinsider.com.au/inside-alibaba-smart-warehouse-robots-70-per-cent-work-technology-logistics-2017-9?r=UK, accessed 09/12/2019.
Michelle Lee Ean Wei, ADPSM. (2019). “New Technologies that will Impact Future Supply Chains”. Retrieved from https://publication.sipmm.edu.sg/new-technologies-impact-future-supply-chains, accessed 09/12/2019.
M0ike Glover. (2017). “7 Essential Warehouse Management KPIs”. Retrieved from https://www.veeqo.com/blog/warehouse-management-kpis, accessed 8 Dec19
Subramanian Venkatesh, DLM. (2017). “The Key Factors to Consider When Choosing Third Party Logistics Provider”. Retrieved from https://publication.sipmm.edu.sg/the-key-factors-to-consider-when-choosing-third-party-logistics-provider, accessed 29/11/2019.