Successful warehouse management depends on a well-organized structure since it has a direct impact on warehouse productivity. Given that a warehouse operation involves ongoing interaction between people, machines, and technology, the proper workflows must be closely followed. The system type and handling equipment for the warehouse storage equipment should be specified for maximum efficiency. Training is therefore essential in order to ensure that everyone is aware of the procedures. Instructors should emphasis the need of upholding safety and security during training. This article discusses several key success factors for efficient functioning of an electronics warehouse.
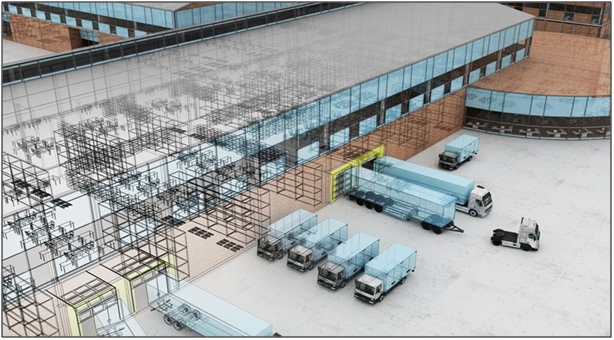
Table of Contents
Warehouse Design and Layout
A well-designed, strategically planned warehouse layout that makes it easier for operations to run smoothly is essential for effective warehouse management. Any storage or distribution facility will be designed or developed with a number of criteria in mind. It increases productivity and efficiency whether it is a large distribution centre for multi-temperature composite materials that serves a substantial market network, a spare parts warehouse, or a raw materials warehouse that supports a manufacturing operation. The functions of a warehouse will have a considerable influence on its poor layout design. Moving, unloading, and retrieving cargo may result in more extended travel. The rate of fulfilment and overall productivity of the warehouse operations will decrease when the warehousing activities slow down. The warehouse team needs to have the necessary procedures in place before they can create a layout that promotes productivity. There must be logical progressions that not only simplify operations but also cut expenses.
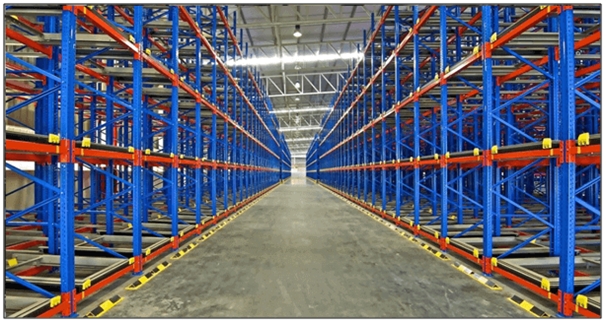
Planning for Warehouse Racking
Another essential strategy for optimizing warehouse space is the utilization of racks and pallet storage. The organization should plan and lay out its warehouse according to its demands after ensuring that the majority of relevant safety considerations will be considered. Pallets as load bearers and storage could save the organization thousands of dollars in storage space. Pallet racks make storing and retrieving items easy and quick, increasing production and labour efficiency. Efficiency is the ultimate goal of warehouse management. When errors can be reduced to a minimum, delays and interruptions are removed, and productivity is increased with a seamless flow of inbound and outbound activity, a company can perform at its best.
Implementing Warehouse Management System (WMS)
Software that manages supply chain fulfilment activities from the distribution centre to the retail shelf is known as a warehouse management system (WMS). The system makes it easier to manage everyday warehouse operations and is more likely to be able to track down items and supplies while providing visibility into the complete corporate inventory. A standard on-premises solution utilizes the company’s original network and infrastructure, and inventory management and warehouse operations are the two most essential components. In contrast, a standalone WMS manages IT needs and is only used for warehouse management functions. An ERP system promotes efficiency by collecting company information, integrating several unrelated systems, and streamlining operations. Material flows, data flows, and money flows are three crucial flows that an effective ERP solution coordinates and merges. It simplifies how their items move from the supplier to the warehouse and then to the customer’s store.
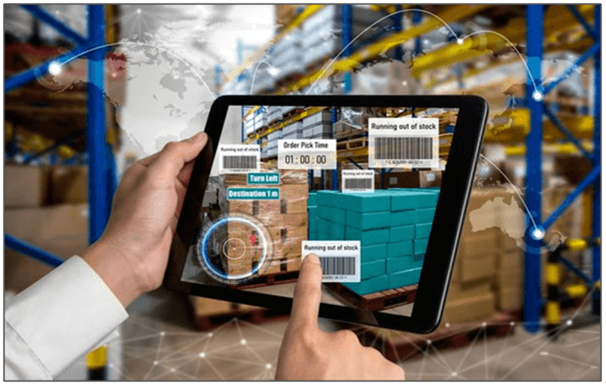
Segregating an Area for Hazardous Products
Each nation has unique standards for storing dangerous items, so compliance is necessary. As certain compounds have temperature control requirements, their safety data sheets (SDS) or labels need to check appropriately. As some chemicals are controlled substances, it requires them to separate and protect their chemicals from misuse or unauthorized access. Store only the bare minimum of chemicals on site and ensure that every chemical has a label that is intact, readable and properly written. The classification refers to the risks associated with hazards and regulatory information risks related to using and archiving product information.
Receiving and Put-Away Operations
The first and most crucial warehouse procedure is receiving. In order to carry out the receiving process correctly, the warehouse must be able to attest that it has received the pertinent product in the necessary quantity, in the ideal condition, at the proper time-series amount, in the perfect state, and at the precise moment. During the receiving process, the responsibility for the commodities is transferred to the warehouse. The warehouse shall be responsible for maintaining the products in perfect condition until delivery. The transportation of items from the receiving dock to the best warehouse storage site is known as putting away, which is the second warehouse procedure. The efficiency of a warehouse operation may be maximised if commodities are stored in their most advantageous position.
The full content is only visible to SIPMM members
Already a member? Please Login to continue reading.