Turnaround time (TAT) is a measuring metrics concept to evaluate a production’s operation throughput. This concept defines the amount of time taken to fulfill a request. The goal is to deliver the final product to the customer in the shortest TAT while ensuring the proper allocation of resources and saving cost/ times and making higher profits.There are several reasons that the TAT can increase in warehouse operation for e.g.: workers are not working properly and following the process, and if the maximum efficiency could not be reached, the process would be delayed. Secondly, improper infrastructure could be an obstacle for the TAT reduction.
Table of Contents
Improving Turnaround Time
There are several techniques to improve Turnaround time for Warehousing Operation using the advancement of the current technology. Some of these include:
• Automated Goods receiving
• Customer Order & Satisfaction
• Compact Picking Systems
• Packing Systems
• Manifesting all Shipments
• Managing Product Replenishment
• Automated Storage and Retrieval Systems
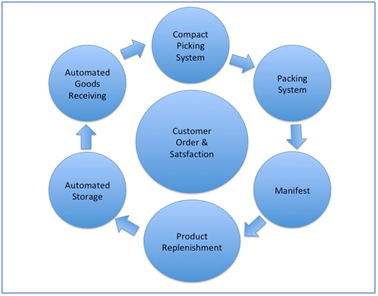
Automated Goods Receiving
Goods receiving is the basis for most of the warehouse activities. It is important to receive products correctly in order to handle them appropriately for put-away, storage, order picking or shipping. After unloading, warehouse management system drives the identification, checking and registration of products.
The functionality includes handling of returns, unexpected goods and repacking. Goods are directed to storage, order picking or directly for shipping through a cross-docking process. Depending on product velocity and specific characteristics, goods can be stored either on pallets or trays, and in cartons or totes. They can be automatically directed for storage or order picking, minimising manual handling and providing speed and efficiency in replenishment and supply.
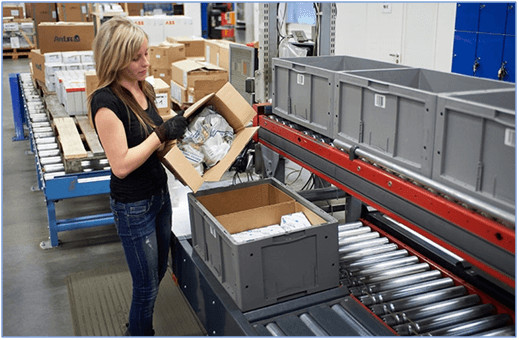
Customer Order & Satisfaction
Errors in order processing can dangerously affect customer satisfaction and put risk of losing valuable revenue. Making the process more efficient with system advancement can satisfy and meet customers’ expectations, which ultimately increases revenue. It can better meet customers’ needs, and increase revenue with a more productive staff.
Compact Picking Systems
Compact-picking system (CPS) is an ideal concept for slow-moving products in retail and wholesale distribution centres. It is also beneficial for distribution centres that handle parts and components, and manage a large product range and extremely high service-level requirements. It takes advantage of the Quickstore family of automated storage and retrieval systems. These “miniloads” and shuttle systems automatically store and retrieve product totes, and make optimal use of available floor space.
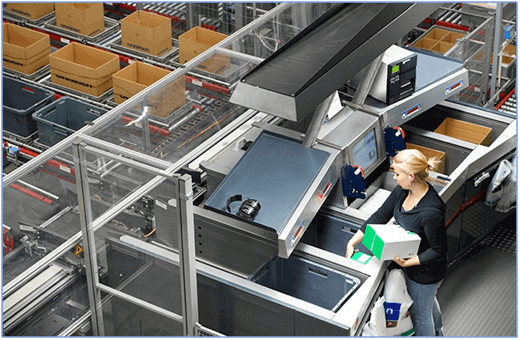
Packing Systems
Several activities come together in the packing process, such as weighing, void filling, carton closing and labelling. Requirements for packing workstations are increasing to improve efficiency and quality, while ensuring that the workstation meets the latest ergonomic standards. Packing systems can be integrated with other picking concepts or delivered as stand-alone. These solutions enable customers to organise their processes in the most efficient, cost-effective way.
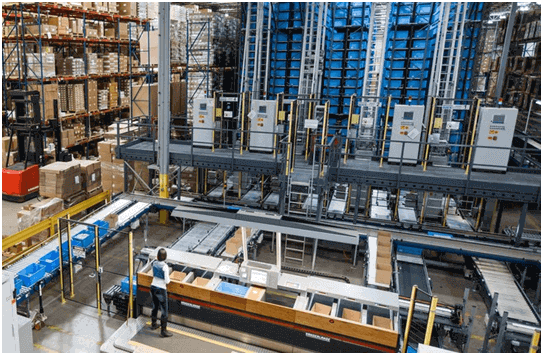
Manifesting all Shipment
The manifest is a list of all goods, listed per Bill of Lading, which was loaded onto the ship in one certain port and which has a single certain destination. Thus the number of manifest on board equals the number of different travel routes. A distinction is made between a cargo manifest, a freight manifest and a manifest of hazardous goods. The cargo manifest solely lists the details of the goods (nature, quantity, types and numbers, sender, destination, etc.) and service for customs declaration of the goods. In addition to that, the freight manifest lists details of the seaborne freight and serves to collect the sea freights payable at destination and as basis for certain commission calculations. The hazardous goods manifest solely lists hazardous goods on board the vessel. This manifest must be submitted to the port authorities prior to the vessel entering the port.
Managing Product Replenishment
The secret to making all of these possible is by an effective warehouse management software program that provides an accurate read on where your areas of opportunity are for improving overall efficiency. Your replenishment efficiency lives and dies by your warehouse management system and how easy it is for your workers to integrate with that system on the warehouse floor. You need a system and devices that allow your workers to accurately track inventory movement as it arrives at intake and when it rolls out for delivery. Your picking team will be the group that is most impacted by your warehouse management system, so be sure to listen to their feedback and commentary when you are deciding on whether or not your system needs to be improved. Trusting your experienced professionals who are your boots on the ground personnel is essential for staying up to date on what is and isn’t working. Moreover, it’s just smart business to depend on the opinion of the people who make your warehouse run every day, all day. Working with your picking team to get the right system in place to track metrics and improve performance should be your starting point for improving replenishment efficiency.
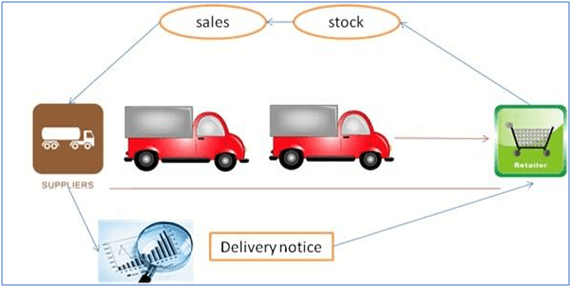
Automated storage and retrieval systems
ADAPTO is a unique 3D, shuttle-based automated storage and retrieval system (AS/RS) with built-in sorting and sequencing capabilities. It offers unrivalled flexibility and helps you to adapt to changing market dynamics.Through multidirectional movement and sequencing, ADAPTO delivers goods in the appropriate order to the correct picking station. Therefore, the order fulfilment is fast and accurate. This facilitates same-day deliveries, which is ideal for the e-commerce market.
ADAPTO requires a limited initial investment. As and when a DC needs to change in the future, its adaptive and scalable configuration makes it possible to expand on a ‘step-by-step’ basis. Additional aisles can be added while the system is operational. If order volumes grow, more shuttles can be deployed to cope with extra demand.
In addition, storage capacity and throughput can be scaled independently, which helps you to keep any future investments in line with your individual requirements. The modular design makes optimal use of all existing space within your DC, regardless of shape or size.
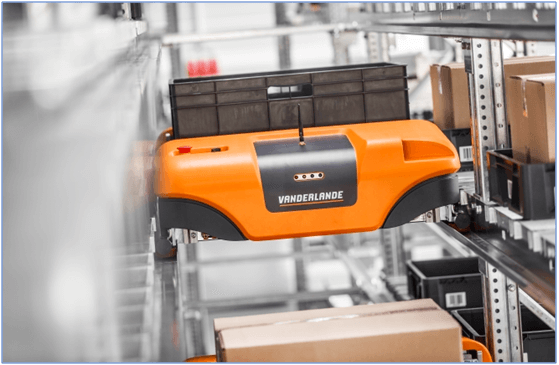
Conclusion
We understand how critical improving TAT can affect the warehouse operation and by using the various solutions that we have recommended can lead to faster performance and computing speeds. These solutions not only enable companies to organise their processes in the most and cost-effective way and can increase sustainable productivity and value-added services to the organisation.
References
Balaguru Patmanathan. (2018). “The Five Essential Techniques for Effective Warehousing”. Retrieved from SIPMM: https://publication.sipmm.edu.sg/the-five-essential-techniques-for-effective-warehousing/, accessed 26/09/2018.
Ee Soon Sern. (2018). “Autonomous Mobile Robotics for Effective Warehousing”. Retrieved from SIPMM: https://publication.sipmm.edu.sg/autonomous-mobile-robotics-effective-warehousing, accessed 26/09/2018.
Ken Jacobsen. (2012). “Improve Customer Service and Order Processing to Accelerate Customer Growth”. Retrieved from https://www.erpsoftwareblog.com/2012/04/improve-customer-service-and-order-processing-to-accelerate-customer-growth/, accessed 26/09/2018.
Logistics Glossary. “Manifest”. Retrieved from https://www.logisticsglossary.com/term/manifest/, accessed 26/09/2018.
Newcastle Systems. (2017). “How to Improve Your Warehouse Replenishment Efficiency”. Retrieved from https://www.newcastlesys.com/blog/how-to-improve-your-warehouse-replenishment-efficiency, accessed 26/09/2018.
Vanderland. (2018). “Automated goods receiving / Compact Picking Systems / Packing Systems / Automated and Retrieval Systems”. Retrieved from https://www.vanderlande.com, accessed 26/09/2018.
Wikipedia. (2018). “Turnaround Time (TAT)”. Retrieved from https://en.wikipedia.org/wiki/Turnaround_time, accessed 26/09/2018.