In a typical warehouse, order picking is the most manual, labor-intensive, and costly operation. It can account up to 60% of the operation costs. Companies tend to focus on this area first because various improvement can positively impact their customer’s experience. This means that warehouse picking involves workers picking items from cartons on warehouse shelves and placing them into boxes for shipment to customers. Picking requires great contract of coordination, organization, and thoroughness in order to move the pickers through warehouses smoothly for them to fill the maximum number of orders in the shortest time.
Warehouse managers frequently search for strategies to restructure the picking process because it can be time-consuming and costly if not done as efficiently to maximize productivity. However, they also feel pressured to enhance picking practices to meet and exceed customer expectations, as both picking speed and accuracy affect customer’s satisfactory.
There are several picking strategies for distribution center to boost their order picking performance and increase productivity. The picture below shows a typical warehouse that requires space to store products safely until they are shipped, as well as the need for an effective and accurate system to track inventory until it is finally delivered.
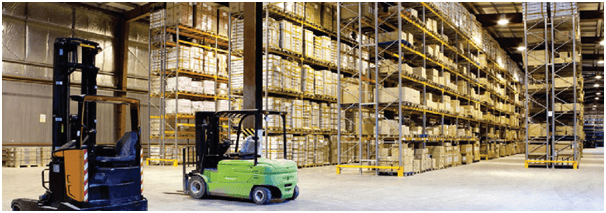
Table of Contents
Warehouse Efficiency
Warehouse efficiency is then improved when items are allocated to the correct storage media. Taking example if all operators have wet paint on their hands, then the optimized warehouse has the minimal number of fingerprints on the boxes. Taking fingerprints off the boxes means the warehouse has been set up to minimize product handling.
The first basic principle to be adhered to is to ensure items are stored in the appropriate storage media. Having slow moving SKUs in pallet racks is as wasteful as having fast moving SKUs in shelving bins. We make this decision based on a variable which is the cube movement velocity, it is used to measure the volume of movement for each SKU. The cube movement velocity = movement in units x cubic dimensions of the unit. Measuring this metric for every SKU provides a significant way to ensure that products are being handled within the most appropriate storage media. High cube movement belongs in racking and low cube movement can be assigned to smaller storage media formats.
Eliminate Walking and Fatigue for more Accurate Picks
We need to minimize movement such as reduce walking around a warehouse as high chances of mistake occur when a person is regardless physically or mentally tired. By decreasing the amount of movement will aid in faster and more accurate picking.
Warehouse layout and design is another factor which aids maximizing efficiency, order accuracy and increase productivity of a warehouse. To minimize the walking made by employees. Your storage and pick strategies will have direct effect on this. Instead of using manual picking and random storage strategy, switching to a zone-based picking system and volume or class-based storage systems can allow you to minimize trips.
The pick and pack process is highly complex, and its success eventually depends on getting a number of factors right. Factors such as the design of your warehouse, the technology and tools you use, how items in your warehouse are stored, the routes your order pickers take through the warehouse, your order picking strategy, how you pack, stage and prepare your order-along with multiple other factors-all play a role in whether your pick and pack process result in a properly fulfilled order and a happy customer.
Organize workstations
Organizing workstations improves productivity because workers do not have to search for tools or equipment. Using the “5S” method from lean manufacturing to ensure your workstations are as organized as possible. It consists of Sort, Set in order, Shine, Standardize; and Sustain. All these techniques are designed to keep clutter at bay, reduce errors, and improve safety and organization.
Adopt Enabling Technology
A warehouse management system (WMS) or an ERP system with a strong WMS module can improve efficiency by suggesting the best routes and methods for picking or put-away. In addition, the system provides automated pick lists that can be sent to mobile readers and devices to help eliminate mistakes and reduce wasted time and paper. In such case, your warehouse will be neater and greener. Using barcode or radio frequency identification (RFID) readers can improve the accuracy of transactions, and reduce picking errors.
The picture below shows the WMS is used to control and track the transfer and storage of materials in a warehouse to ensure data transparency throughout the company. This also includes inventory management, picking processes and auditing.
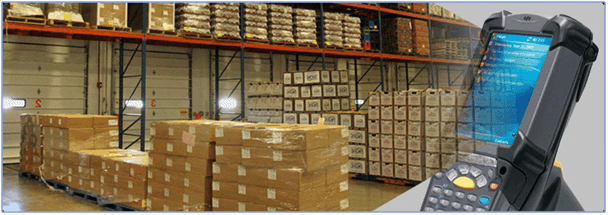
Considering a Different Picking Strategy
Most company begin with manual piece picking, however, as they grow they find that this strategy cannot accommodate high volume in the warehouse. Looking at zone, batch and wave picking, along with some level of automation is a logical progression to support future growth and efficiency.
In a pick-to-light system, an operator will scan a bar-coded label attached to a box. A digital display located in front of the pick bin will inform the operator of the item and quantity that they need to pick. Companies usually use pick-to-light systems for their top 5 to 20% selling products. This system help companies can gain significant efficiencies as it is totally paperless and eliminates the errors caused by pick tickets.
The full content is only visible to SIPMM members
Already a member? Please Login to continue reading.
References
Christine Wheeler. (2017). “7 Excellent Methods to Improve Picking and Packing Efficiencies”. Retrieved from https://www.newcastlesys.com, accessed 10/03/2018.
Ee Soon Sern. (2018). “Autonomous Mobile Robotics for Effective Warehousing”. Retrieved from SIPMM: https://publication.sipmm.edu.sg/autonomous-mobile-robotics-effective-warehousing, accessed 10/03/2018.
Monica Origo. (2016). “How to Drive more Efficiency from your Pick and Pack Process”. Retrieved from
https://www.handshake.com/blog/pick-and-pack-efficiency , accessed 10/03/2018.
Marc Wulfraat. (2013). “5 Ways to Improve Order Picking Productivity”. Retrieved from https://www.supplychain247.com/ article, accessed 10/03/2018.
Martin Murray. (2017). “5 Warehouse Best Practices to Lower Picking Time”. Retrieved from https://www.thebalance.com/warehouse-best-practices-2221401, accessed 10/03/2018.
NurahimMasruri. (2017). “Innovative Technologies for Warehouse Implementation”. Retrieved from SIPMM: https://publication.sipmm.edu.sg/innovative-technologies-warehouse-implementation, accessed 10/03/2018.
Prakaash G. (2018). “Techniques to improve the Warehouse Order-Picking Process”. Retrieved from SIPMM: https://publication.sipmm.edu.sg/techniques-to-improve-the-warehouse-order-picking-process, accessed 10/03/2018.