Knowing the right warehouse metrics to track to improve profitability and operations is keys to the success of your organization. Unfortunately, successful metric tracking benchmarking procedures, including identifying areas that need to be assessed, monitored, researched, compared and acted upon, are essential to setting up a metric system. In addition, your organization needs to know what factors impact metrics and which metrics can have the greatest impact.
Table of Contents
On-Time Shipment to Customer
It must accurately and efficiently distribute goods that are coming in and out of the warehouse. In other words, the correct product must be placed on the correct transportation method at the appropriate time. In order to complete this task, you must monitor late shipping departures to the warehouse and early completion of freight loading time. The percentage of items ordered by customers that arrive on, or before, the requested ship date is the on-time shipping rate.
Happy customers are more likely to return and tell others of your prompt services. The rate is calculated by dividing the number of on-time items by total items, then multiplying the result by 100 for a percentage.
Inventory Accuracy
Inventory accuracy is a comparison of the items in stock and the items recorded in the database. If the two counts do not match, there are issues with bookkeeping and data management, which can be fixed by implementing an automated inventory control solution, such as barcode or RFID systems.
Fill Rate
The fill rate is the percentage of an order that is filled on the first shipment. This metric is important for two reasons: It relates to customer satisfaction (do a large percentage of items take more than one shipment to be filled?) and to transportation efficiency, which can be affected if multiple shipments are often needed to fill orders.
As an example, a customer orders 20 units of SKU 2677, but the seller ships the 15 units it possesses. The fill rate equals 15/20 = .75. An out-of-stock situation occurred, but demand was partially filled. From this simple definition, a large number of combinations exist in how to craft fill rate measures.
Demand Forecast
The demand forecast is the estimation of how much product consumers will purchase, using both educated guesses and historical sales data. These estimations can be used to determine future capacity requirements, pricing or even opportunities in new markets. The accuracy of these estimations can be assessed afterwards by using actual sales as a base.
The figure below shows the planning and forecasting demand of warehouse
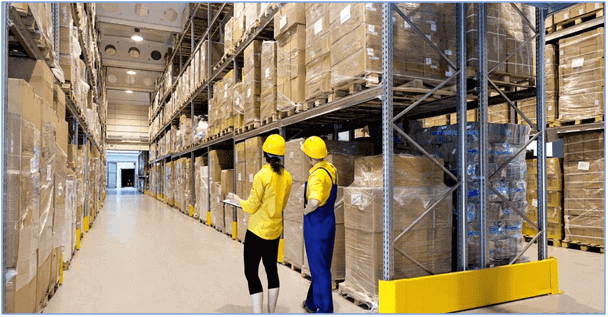
Customer Order Cycle Time
This cycle measures how long it takes for a customer to receive a product after placing an order. This is a key component for measuring customer satisfaction. Companies with shorter Order Cycle Times are more responsive to customer orders. Longer lead times may ultimately result in customer dissatisfaction and competitive disadvantage. Order Cycle Time is considered less relevant to Make-to-Stock supply chains, these generally put more emphasis on improving Fill Rates. The formula is actual delivery date minus the purchase order creation date.
Customer service
Repeated business requires complete customer satisfaction. Direct customers expect merchants to ship their orders the same day that an order is placed, or at least the next day, they expect to receive the order in good condition, and they do not tolerate a negative performance (see service level metrics in the table Fulfilment Operations Metrics).
As noted earlier, Q4 holiday customers are ordering later each year. This pattern of delayed purchase is a trend for which merchants must plan in order to secure repeat business. Everyone in the company needs to understand service level metrics, which should be reported just like productivity metrics. Fulfillment delivers on your company’s marketing and merchandising promises. Promise realistically and over-deliver.
Employee turnover
Employee turnover is expensive. Employers need to tell employees what is expected and give them feedback and to create a work culture that makes people want to stay. Most people want to know how they are doing and to be part of a team.
There are two main categories of turnover: voluntary and involuntary. Each of them has different causes.
The full content is only visible to SIPMM members
Already a member? Please Login to continue reading.
References
Brian Barry(2017). “15 Ways to Improve Warehouse Space Utilization”. Retrieved from http://multichannelmerchant.com/blog/15-ways-improve-warehouse-space-utilization/, accessed on 17/03/2018.
F.Curtis Barry & Company(2016). “Trends, Best Practices, and Metrics in Fulfilment”. Retrieved from https://www.fcbco.com/articles-and-whitepapers/articles/bid/129442/trends-best-practices-and-metrics-in-fulfillment, accessed on 17/03/2018.
Guest contributor (2017). “Top 10 Logistics Metrics to Measure Supply Chain Efficiency in Your Warehouse”. Retrieved from https://www.fronetics.com/top-10-logistics-metrics-to-measure-supply-chain-efficiency-in-your-warehouse/, accessed on 17/03/2018.
Jay Schofield (2015). “The 15 Supply Chain Metrics that Make or Break Warehouse Efficiency.” Retrieved from http://www.systemid.com/learn/warehouse-efficiency-metrics/, accessed on 17/03/2018.
Nurahim Masruri, SIPMM. (2017). “Innovative Technologies for Warehouse Implementation”. Retrieved from https://publication.sipmm.edu.sg/innovative-technologies-warehouse-implementation, accessed 10/03/2018.
Prakaash G., SIPMM. (2018). “Techniques to improve the Warehouse Order-Picking Process”. Retrieved from https://publication.sipmm.edu.sg/techniques-to-improve-the-warehouse-order-picking-process, accessed 10/03/2018.
Tan Kwang Hong, SIPMM. (2018). “IoT Devices that transform Current Warehouse Technology”. Retrieved from https://publication.sipmm.edu.sg/iot-devices-that-transform-current-warehouse-technology, accessed 10/03/2018.