Warehouse management principles have existed for as long as man has sold and shipped products. It really all boils down to knowing what you have, where it is, and how much can be sold. Inventory control principles and tools were developed in response to this need, such as checking perpetual inventory balances, and having inventory tracking cards.
Early Warehouse Management System (WMS) applications were more accurate and timely than the old card type records, but there still have limitations and draw backs. These early systems required people to key in critical information. With the typical human entry error rate of 1 per 300 key strokes, a high degree of accuracy required double and triple checks. This article attempts to explore the various technologies currently in use for a typical warehouse.
Current Warehouse Technology
1. Pick by Voice
The voice picking system allows warehouse staff to concentrate on the picking process without looking at paperwork and having both hands free to perform the pick. The original voice picking systems were used where items were not bar-coded such as fresh produce, so a handheld scanner could not be used.
The voice picking system uses speech recognition and speech synthesis to allow warehouse operators who are performing the picks to communicate with the Warehouse Management System (WMS).
The staff on the warehouse floor uses a headset and microphone to receive instructions by voice, and verbally confirm their actions back to the system. The warehouse operator will normally read back the last 2 or 3 digits of the item they have picked so that the system can check the correct item has been selected.
2. Pick-by-Light or Pick-to-Light
Pick-by-Light systems, sometimes called Pick-to-Light systems, use light displays to direct operators to specific stock locations. Each product location can have an individual numeric or alphanumeric display with a light, an acknowledgement button, and a digital readout for indicating quantity.
Other configurations allow fewer or more simplified displays to reduce the total cost. In a typical Pick-by-Light system, the picking sequence starts at the beginning of a zone where the operator scans a bar coded address label attached to the shipping carton or tote. The display tells the operator which products to pick and how many of each. The operator confirms picks via acknowledgement buttons.
3. Put-by-Light or Put-to-Light
In Put-to-Light systems, sometimes called Put-by-Light systems, light displays instruct the operator where and how to allocate stock to orders, allowing efficient picking from bulk stock. The operator scans each product and flashing light displays at each location indicate which containers require that product and how many items to put.
Confirmed put results are updated to the system in real time for host system updates. Typical businesses using a put system include retailers of general merchandise, apparel, grocery, convenience foods, sporting goods, and personal care items.
4. Barcode system
To efficiently manage the supply chain, you need secure barcode systems for transporting resources and managing logistics, such as material handling, storage and warehousing, transportation, and security.
It is challenging to have the correct item in the correct place at the correct time, and delivered to the correct customer. Suppliers are usually not easily accessible. The work stations and warehouses are not centrally located, and fleets must be maintained, leaving little time to tighten distribution networks, accelerate packaging, and improve order fulfilment.
The barcode system can alleviate these problems by aiding the following functions:
• Manage inventory
• Track assets
• Manage material handling
• Streamline production
• Expedite fulfilment
In addition, there are warehouse management systems for improving security, automating warehousing, and implementing wireless networks. They use the latest technology, such as RFID and 2D, with hybrid mobile devices and advance barcode scanners to deliver the security, speed, and cost-savings you need.
5. Radio-Frequency (RF) Picking
RF picking is a popular and widely used technology in distribution centers and warehouses. The RF system has a host server that communicates directly with the higher level of WMS system in order to send and receive order information. The information is relayed to the RF terminals that warehouse operators and order pickers wear, typically on their wrists. These terminals direct the order picker to the proper pick location and provide item description and quantity to pick.
Once completed, the order picker sends a confirmation signal to the host signal either by scanning the item with the terminal or manually pressing product identification buttons on the terminal. When all lines in an order are complete, the order status in the WMS is updated by way of the host system and the next order in the queue is sent through the host to the terminal on the order picker.
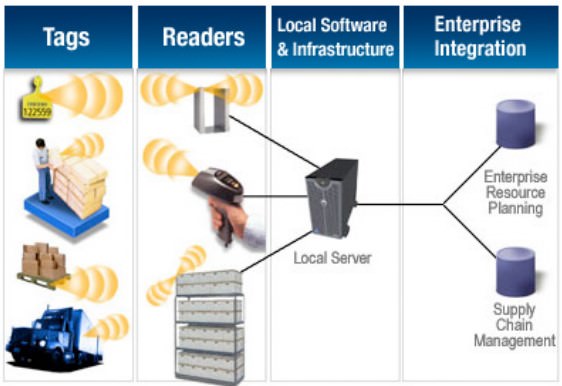
6. Radio-Frequency Identification (RFID) system
RFID system has two parts – electronic devices called readers that send out radio signals, and label-like tags with a small amount of information in them – usually just a unique serial number. When the reader’s radio signal hits the tags, the tag can reflect back a signal with its serial number. In this way the reader can identify all the tags within a short distance, usually a few meters. In addition to being able to identify and count all of the tags in the vicinity, some readers can estimate the location of the tag.
7. Electronic Data Interchange (EDI)
EDI is a system or method for exchanging business documents with external entities. Regardless of the size of companies, implementing EDI is essential for competitiveness and growth. It reduces costs and improves the operational performance across your organization.
EDI accelerates data exchange and sharpens accuracy. The company as well as customers benefit from streamlined administration, improved information flow, more accurate accounting, better inventory management, and lower costs.
The full content is only visible to SIPMM members
Already a member? Please Login to continue reading.
References:
Cooper, J.C. & Davis, Matthew. (1984) “Why have a warehouse?”, Retail and Distribution Management, Vol. 12 Issue: 5, pp.66-68, doi: 10.1108/eb018248
http://cdn2.hubspot.net/hub/190312/file-28949620-pdf/whitepaper/w109-evolution-of-wms.pdf
https://www.linkedin.com/pulse/warehousing-history-present-trends-prashant-dedhia
https://www.thebalance.com/pick-to-voice-warehouse-systems-2221457
https://www.dematic.com/en/supply-chain-solutions/by-technology/voice-and-light-systems/pick-to-light-put-to-light/
https://www.systemid.com/barcode_systems/
http://www.trifactor.com/Material-Handling-Systems/Order-Picking-Systems/RF-Picking
http://www.mojix .com/next-generation-rfid-technology-already-here/
https://www.truecommerce.com/resources/what-is-edi
https://www.barcodesinc.com/cats/barcode-scanners/2d.htm
http://searchmanufacturingerp.techtarget.com/definition/warehouse-management-system-WMS
http://www.asiaoutlookmag.com/news/industry-50-a-new-era-of-modern-manufacturing