This article highlights five key techniques for effective inventory stock control of an organisation. Maintaining safety stock is an essential part of capturing opportunistic sales, retaining business and making customers satisfied. The common reason of delay shipment is lack of proper planning for inventory stock control. The safety stock lever is essential especially for those products with long delivery lead time.
Inventory control is also important to maintaining the right balance of stock in your warehouses. You do not want to lose a sale because you did not have enough inventory to fill an order. On the other hand, over-inventory can trigger profit losses – whether a product expires, gets damaged or replace by new version.
Table of Contents
Accurate Forecasting
Forecasting is the technique of using the historical data to predict the future. As simple as it may sound, businesses find this difficult to do. This is in great part because there are way too many forecasting techniques out there and business leaders get confused about which to use. We will look into some of these techniques used across the world and how to choose them for a specific business problem. In production and inventory control, increased accuracy is likely to lead to lower safety stocks. The Purchasing manager and forecaster must weigh the cost of a more sophisticated and more expensive technique against potential savings in inventory costs.
ABC Inventory Analysis
The ABC analysis is a business term used to define an inventory categorization technique often used in material management. It is also known as “Selective Inventory Control” ABC analysis provides a mechanism for identifying items that will have a significant impact on overall inventory cost, while also providing a mechanism for identifying different categories of stock that will require different management and controls that inventories of an organization are not of equal value.
ABC Analysis allows inventory/purchasing managers to segregate and manage the overall inventory/suppliers into three major groups. This allows different inventory/supplier management techniques to be applied to different segments of the inventory/suppliers in order to increase revenue and decrease costs.
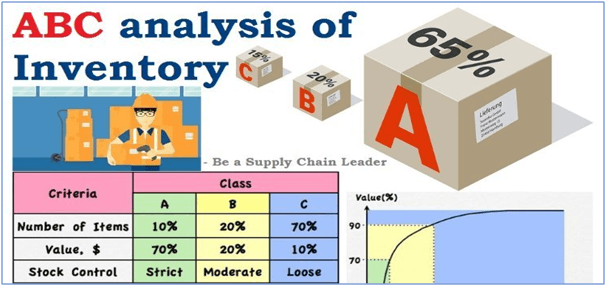
Economic Order Quantity Model
The basic decision in an economic order quantity (EOQ) procedure is to determine the amount of stock to be ordered, at a particular time so that the total of ordering and carrying costs may be reduced to a minimum point. A firm should place optimum orders and neither too large nor to small. The EOQ is the level of inventory order that minimizes the total cost associated with inventory
Economic order quantity (EOQ) is a decision tool used in cost accounting. It’s a formula that allows you to calculate the ideal quantity of inventory to order for a given product. The calculation is designed to minimize ordering and carrying costs. EOQ assumes that you order the same quantity at each reorder point.
The EOQ model is very simple one and its assumptions will be unrealistic in many applications, in practice orders are not delivered instantly. The assumption of a constant usage of inventory and known annual demand are of doubtful validity.
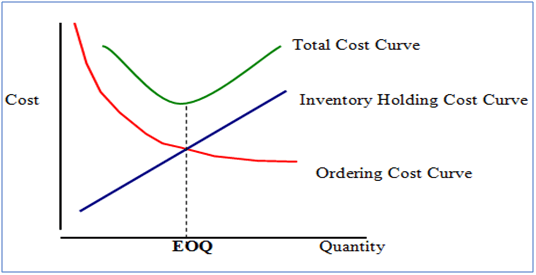
First-in-first-out (FIFO)
A simple principle, yet vitally important to mention – especially if dealing with perishable items. For most retailers, the last thing you want is to be always using the newest stock to fulfil orders. This leaves older inventory sitting in the warehouse and susceptible to damage, decay or passing best before dates. It’s worth making a rule to store new inventory from the back of shelves and then take from the front – automatically enforcing a FIFO system.
FIFO is also a popular method for calculating inventory value when it comes to getting those end-of-year accounts done. The difference between FIFO and LIFO results from the order in which changing unit costs are removed from inventory and become the cost of goods sold. When the unit costs have increased, LIFO will result in a larger cost of goods sold and a smaller ending inventory compared with FIFO. Also, note that the order in which the costs are removed from inventory is independent of the order in which the physical units are removed from inventory.
The full content is only visible to SIPMM members
Already a member? Please Login to continue reading.
References
Kalpana, R. (2018). “Methods and Techniques of Inventory Control Business Management”. Retrieved from http://www.businessmanagementideas.com/business-management/methods-and-techniques-of-inventory-control-business-management/542, accessed 23.09.2018.
Mike Glover. (2017). “Inventory Control Methods”. Retrieved from https://www.veeqo.com/blog/inventory-control-methods, accessed 21.09.2018.
Nicholson, B.T. (2018). “Managing Inventory Turnover”. Retrieved from http://www.abladvisor.com/blogs/13340/managing-inventory-turnover-a-key-operational-strategy-for-retailers, accessed 11.09.2018.
Philip Charles Loges. (2018). “Key Performance Indicators for Evaluating Purchasing Performance”. Retrieved from SIPMM: https://publication.sipmm.edu.sg/key-performance-indicators-evaluating-purchasing-performance, accessed 23.09.2018.
Terese Ong Yee Chiat. (2018). “Five key techniques for inventory management and control”. Retrieved from SIPMM: https://publication.sipmm.edu.sg/five-important-techniques-for-effective-inventory-control, accessed 02.09.2018.