Warehousing basically involved two types of activities, inbound and outbound operations. Inbound activities consist of sourcing, expediting, receiving and storage while outbound activates involve picking, checking, packing, and transportation. Outbound processes are more work concentrated than inbound process, particularly order picking is the most labor-intensive work because for each SKU the picker have to travel to the storage location to retrieve the goods.
Table of Contents
Transportation Sourcing
In transportation, there are different modes of transport by Air, Sea, and Land. Air transport is the fastest and most efficient method of transportation used by many companies. However, being the fastest and highest efficiency, it is also considered costlier compared to the other mode of transport.
Sea transportation has the largest carrying capacity that is suitable for carrying bulky cargo over long distances. Although sea transportation will take a longer time to reach the destination, but the cost is lower and more affordable compared to Airfreight.
Land transportation is flexible and also cheaper for small shipments regardless of distance, it is mainly used for local delivery within the country. For example, the company uses a truck to deliver products within Singapore.
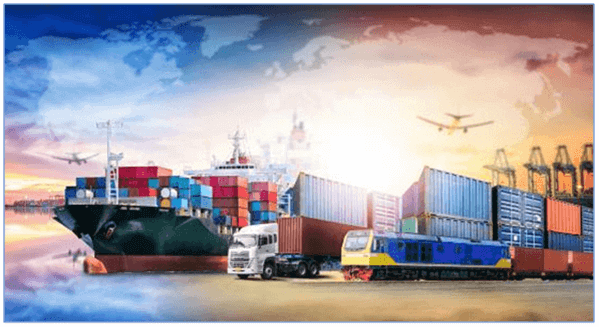
Inbound Process
The incoming process is crucial any receiving and delivery to the end-user will be delayed if there is a late delivery from the supplier. This will affect the company’s processes and reputation resulting in unnecessary costs incurred. Therefore, buyers must ensure all deliveries are made on time in order for the operation to run smoothly without any hiccups. On the other hand, the receiving personnel has the responsibility to check if all goods received are in good condition before accepting and endorsing the Delivery Note. Such as inspecting the quality, condition, and quantity of the incoming goods to match against the purchase order before entering the warehouse, and the receiving personnel must keep track of all incoming shipments into the warehouse and ensures that the right products are received and promptly stored in the warehouse.
Cross Docking Strategy
The objective of cross-docking is to reduce warehouse space and increase operational efficiency. Cross docking is often used when handling sensitive and perishable inventory. Two basic types of cross docking are pre-distribution and post-distribution. During pre-distribution goods are unloaded, sorted and repackaged in accordance with the predetermined instructions for distribution. In post-distribution sorting is delayed until the appropriate facility or customer is identified on the demand basis.
Advantages of cross-docking, streamline the supply chain from an origin location to destination location, quickens delivery of products to customers, less inventory handling means reduce labor cost and increase warehouse space. On top of that, it will reduce the amount of warehousing space required and risk of damaged inventory due to handling, and reduce transportation cost as well.
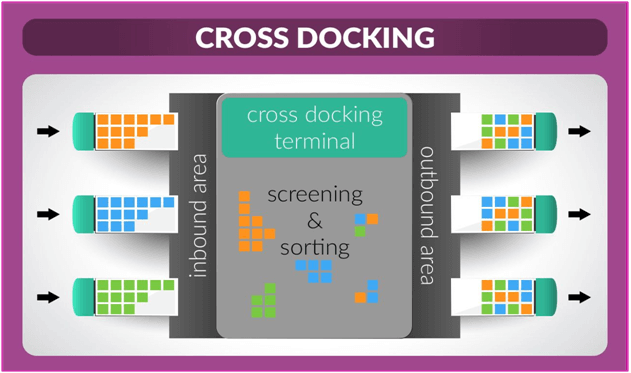
Warehouse Process
The put-away process includes the initial placement of goods, which will directly affect all subsequent warehouse processes, especially the picking process. If the put-away process that is not up to standards this may increase travel time when packaging and picking product. To avoid this, check out the following steps really to increase productivity and efficiency in the warehouse.
- Collect the correct data and analysis before putting away, such as product dimension, frequency of receipt, and current storage availability.
- Create a timeline, when items are received, receiving should be put away asap to help clear the receiving space and make fulfilling orders simpler and hassle-free.
- A modern WMS can seamlessly communicate with the ERP and expedite receiving capabilities and it will speed up the put-away process.
- Ensure items are placed correctly at the first attempt.
- Look for a system that can display real-time reports so you don’t have to search for products.
- Reducing travel time and creating a map to reduce travel time from the receiving area to the storage location of the final product is the key to optimizing the put-away process.
- Use direct put-away is a good practice to use in order to increase speed and efficiency. In this method, the goods are moved directly from the receiving area to its final destination without going through a transition phase.
- Keep warehouse clean and organized, a cluttered or disorganized warehouse will have an immediate impact on the put-away process. Even having the most modern warehouse technology and have a streamlined process, you need to keep your warehouse clean and organized to guarantee efficiency.
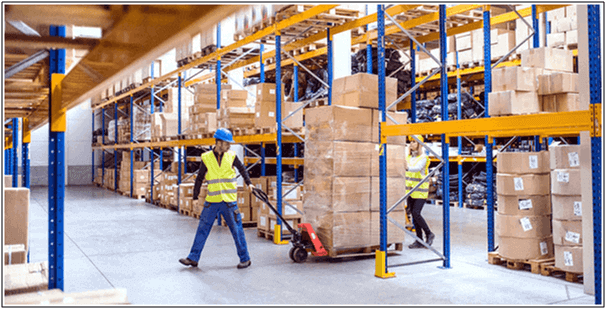
Outbound for Order from Customer
When an outbound order is received from a customer the warehouse management system (WMS) will check, identify and locate the picking surface of each SKU. The warehouse is divided into multiple picking zone where each picker will only be assigned to a specific zone. The WMS will direct warehouse associates to pick the items from the locations when it received an order. WMS is programmed to apply the most efficient picking mode to reduce walking distance and overlapping, thereby minimizing labor costs. As a 3PL third party, our goal is to minimize cost per order for fulfillment activities. Scan the pick items for each order (the system will update the inventory in the WMS) and save it for the next process packaging.
The full content is only visible to SIPMM members
Already a member? Please Login to continue reading.
References
Ho Kek Ming, DLSM. (2019). “Six Essential Areas for an Integrated Logistics System”. Retrieved from: https://publication.sipmm.edu.sg/six-essential-areas-integrated-logistics-system, accessed 05/09/2020.
Kumerendren Vijayakaranhas, DLSM. (2019). “Seven Order Picking Techniques Distribution Centers”. Retrieved from: https://publication.sipmm.edu.sg/seven-order-picking-techniques-distribution-centers, accessed 06/09/2020.
Mavis Lim Chow Yee, DLSM. (2020). “Effective Warehousing for Inbound and Outbound Operations”. Retrieved from: https://publication.sipmm.edu.sg/effective-warehousing-inbound-outbound-operations, accessed 06/09/2020.
Ng Li Hsia Alicia, DLSM. (2019). “Best Practices for Managing Warehouse Inventory”. Retrieved from: https://publication.sipmm.edu.sg/best-practices-managing-warehouse-inventory, accessed 08/09/2020.