Generally, the central laboratory offers the widest selection of tests available to individuals and is organized in a number of departments, including hematology, biochemistry, parasitology, bacteriology, histology, immunology, and virology. Monitoring consumable products, reagents, lab equipment, and instruments could be a big job. But doing so efficiently creating a discipline around inventory control is definitely a highly effective way to teach workers the significance of personal responsibility in laboratory management and the necessity for systems and processes that are essential for efficient lab functions.
As one of the primary challenges, the need for effectively manage and control their inventory. Inventory control can be an essential element of proper lab administration. Having less proper planning of inventory control, inaccuracy in stock count, insufficient effectiveness, safety and security are typical reason which caused organization to under overall performance in key functional areas.
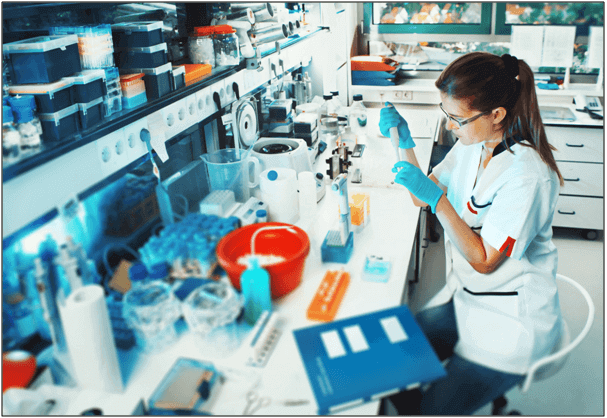
The traditional reason faced by the product manufacturer is delay shipment which insufficient proper planning inventory stock control. The safety inventory stock level is essential specifically for those items with long delivery business lead time. The safety stock level is vital for all those products with extended delivery lead time especially. Maintaining safety stock can be an essential component of capturing opportunistic product sales, retaining business and producing clients satisfied for businesses.
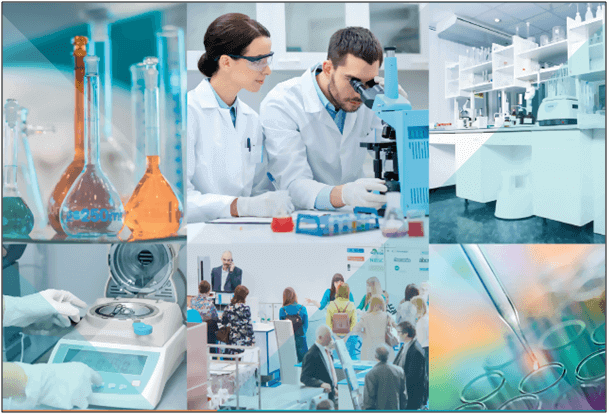
Table of Contents
Economic Order Quantity Model
The Economic Order Quantity (EOQ) may be the optimum level of goods to be purchased at single time to be able to minimize the annual total costs of ordering and carrying or keeping items in inventory. EOQ is a tool used to look for the quantity and rate of recurrence of orders had a need to meet a particular demand level whilst minimizing costs per purchase. An organization should place the very best orders, an ongoing organization should place the very best orders, not too big or too small. Level of materials which may be purchased at minimal costs. It is the size of the entire lot to be bought which is economically practical.
The benefit for a business to invest time calculating EOQ is to reduce its inventory costs and, subsequently, make strides toward being as efficient as possible. A business may use this calculation to determine precisely when an order must be placed and precisely how much should end up being ordered so that the business can continue normal production and reduce inventory costs. EOQ is a very efficient tool for managers because they are able to use it to determine what is the perfect quantity of inventory to carry on hand and then concerning calculate when to purchase more products because new sales ought to be generated.

Cycle Counting
Cycle counting as the process of counting a little and predetermined set of goods and materials frequently, instead of completing a complete physical inventory every year. The objective of routine counting is usually to determine information that are incorrect and suitable the reason for the error. Inventory in the warehouse could be classified concerning to worth monetary or motion how fast each item goes in and through the warehouse. And because of the nature of routine counting, arranged quality value items are prone to while fast-moving goods will probably get mis-picked. Many businesses find that routine counting may take time to produce benefits within the beginning stages, however sticking with this method will result in significant payoffs.
Cycle counting offers several benefits:
o Reduced Disruption in Operations
Every company that performs cycle counts regularly does not need to shut down to perform the physical counts. It can be very costly for an organisation to shut down its processes for a day or two.
o Reduced Errors
With cycle counting, time taken between the counts is decreased, thus providing plenty of time to repair any errors that may have taken place. If by any chance the inventory is not accounted for correctly, it is simpler to catch the mistake by approach of cycle counting. Cycle counting also raises the accuracy of inventory counting, Cycle counting enhances the accuracy of inventory counting also, as it is less likely to make any mistake while counting a comparatively less of inventory.
o More Confident Buying Decisions
In the cycle counting technique, the inventory counts regularly are done. With this continuous evaluation, it is possible to concentrate better on the subset of the inventory. As a result of this, the buying decision you take is a lot more targeted and prepared. The buying decision you take is a lot more informed and targeted. Hence, routine cycle counting avoids stock outs way in advance and therefore creates a much better report for the purchasers in your team.
o Savings on Time and Resources
Annual inventory counts could be a messy process. It needs considerable time to check on the inventory counts. It could need a complete large amount of time to check on the inventory counts. Moreover, when there is any feasible discrepancy, locating the error just becomes an extended and time-consuming process. To prevent wastage of period and resources, cycle counting is a good idea.
o Improved Customer Service
If you have well-maintained information, you understand where your items are and just how many items you have in inventory. So, when the clients make requests, facilitating an instant delivery could be easy. When clients get an early on delivery, they’ll normally be more satisfied.
o Sales Increases
Your happy and satisfied customers are more likely to recommend you to others. So, this can indirectly lead to a rise in sales.
ABC Inventory Analysis
The ABC analysis is a business term used to define a listing categorization technique often utilized in material management. It is also referred to as “Selective Inventory Control” ABC evaluation provides a system for identifying items which will have a substantial effect on overall inventory cost, while also offering a system for identifying different types of stock which will require different administration and configurations that inventories of a business aren’t of equal value.
ABC evaluation allows inventory/purchasing managers to segregate and manage the entire inventory/suppliers into three main groups. It will help in maintaining inventory turnover rate at comparatively more impressive range through scientific control of inventories. This allows different inventory/supplier management ways to be applied to different segments of the inventory/supplier to be able to increase revenue and decrease costs.
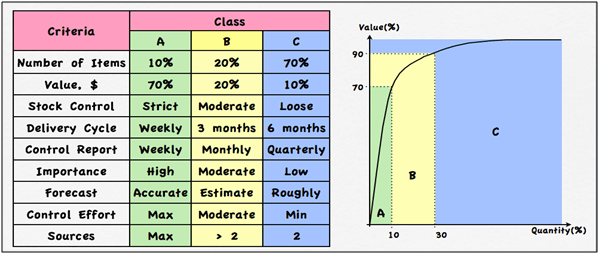
Determination of Stock Levels
Carrying of an excessive amount of and insufficient of inventories is detrimental to the company. If the inventory level is usually insufficient, the firm will encounter frequent stock-outs involving large ordering price and if the inventory level is certainly too high it will probably be unnecessary tie-up of capital. Therefore, a competent inventory management requires a good firm should maintain an optimum amount of inventory where inventory costs would be the minimum and at exactly the same time there isn’t stock-out which may lead to loss in sale or stoppage of production.
The client service level raises as the risk of inventory stock out decreases. Reordering level is fixed between optimum and minimum level. The rate of consumption, number of days necessary to replenish the stock and maximum quantity of materials needed on any period are taken into consideration while adjusting reordering level. It really is helpful in managing sudden upswings most desirable or simply making sure raw materials and supplies readily available to keep production going.
The full content is only visible to SIPMM members
Already a member? Please Login to continue reading.
References
Terese Ong Yee Chiat, DLSM. (2017). “Five Important Techniques for Effective Inventory Control”. Retrieved from SIPMM: https://publication.sipmm.edu.sg/five-important-techniques-for-effective-inventory-control/, accessed on 07/09/2019.
Veron Wong Sook Wei. DPSM (2018). “Five key techniques for inventory management and control”. Retrieved from SIPMM: https://publication.sipmm.edu.sg/effective-techniques-inventory-stock-control/, accessed 08.09.2019.
Puneet Bhalla (2019). “Top 6 Benefits of Cycle Counting vs Annual Inventory Counts”. Retrieved from https://www.shiprocket.in/blog/top-6-benefits-cycle-counting-vs-annual-inventory-counts/, accessed 10.09.2019.
Mike Glover. (2017). “Inventory Control Methods”. Retrieved from https://www.veeqo.com/blog/inventory-control-methods, accessed 11.09.2019.
Saumya Singh. (2014). “Economic order quantity (eoq)”. Retrieved from https://pt.slideshare.net/saumyasingh7921/economic-order-quantity-eoq, accessed 10.09.2019.
Matin. (2016). “A Complete Guide to ABC Analysis in Customer Segmentation and Inventory”. Retrieved from https://www.cleverism.com/complete-guide-abc-analysis-customer-segmentation-inventory/, accessed 08.09.2019.
Inventory Turnover Ratio. (2019). Retrieved from https://www.myaccountingcourse.com/financial-ratios/inventory-turnover-ratio, accessed 12.09.2019.
Smriti Chawla. (2019). “Financial Management”. Retrieved from https://sol.du.ac.in/mod/book/view.php?id=829&chapterid=495, accessed 11.09.2019.