Key performance indicators (KPIs) are frequently used in general business to evaluate the success of everything from a specific department to an entire enterprise. They focus on strengths and weaknesses. Many warehousing KPI’s tend to be focused on external performance, such as on-time shipments that directly impact customers. This is a good measure, but the need to go deeper and measure the factors that drive those success rates is critical.
Table of Contents
The Warehouse is a Critical Function
Companies that relentlessly measure sales, customer service, financial, and other functions sometimes treat their shipping and handling operations as an afterthought, which is unfortunate, because the warehouse is where tremendous value can be added to the process. Since it’s often the very last buffer between you and your customers, its role in customer satisfaction can’t be overstated. The product should flow in, store, process, and flow out with a minimum of “touches” by human hands and processes. To get to that state, you have to break down the processes. What can be improved? What should be revamped? Do you know what the industry standards are? What are your competitors and peers measuring?
Typically, in broad terms, we’re discussing productivity, quality, errors, time, and costs. But the specific processes that feed these measures are what’s important.
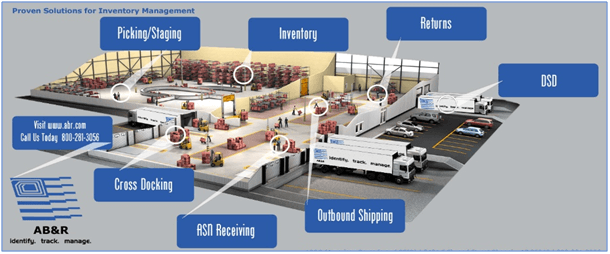
KPI for Warehouse Inventory Accuracy
Inventory is a major part of warehousing, and inventory accuracy is a critical KPI for warehouses because if your inventory tracking is incorrect, your costs will skyrocket, and your customer satisfaction levels will plummet. If you are relying on Excel or manual processes, your inventory accuracy will be far too low, and there’s a good chance you’ll end up reordering or manufacturing parts you already have due to inaccurate counts. The costs of carrying too much inventory, or of angering customers when you don’t have inventory on-hand that you indicated is in stock, will hurt not just your bottom line but also your reputation.
One solution for inaccurate inventory is choosing a system that uses barcodes to track inventory. Some warehouses find that barcoding systems integrate with their current computerized maintenance management systems (CMMS). These systems improve inventory control by providing a framework for managing inventory, supplies, and other warehouse materials. Additionally, some CMMS can have the capabilities for tracking shipments, managing purchase orders, and monitoring stock and inventory levels.
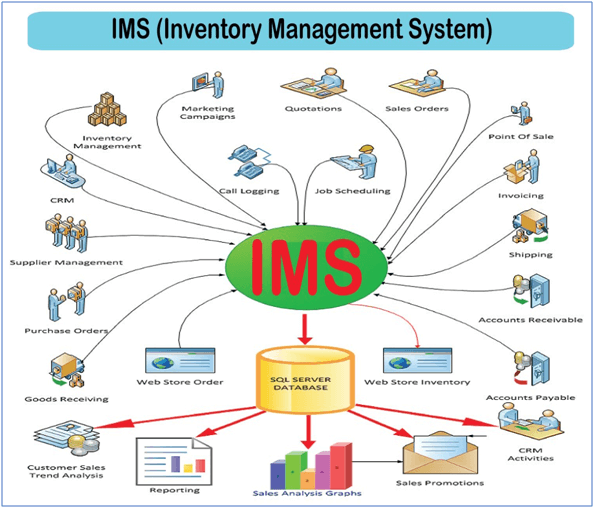
KPI for Efficiency of Receiving
One of the most critical operations of a warehouse is receiving stock; thus, the efficiency of receiving is a KPI for warehouses and should consider received volume, customer returns, missing and broken stock, and return to vendor stock. Karl Friesenbichler, an automation industry expert, reminds warehouse managers to group figures by the source and times to “identify peak times, quality issues with suppliers, and the return rate from various sales areas.”
The efficiency of your receiving area significantly impacts warehouse operations. You should know the rate at which inventory is counted and be able to identify deficiencies in receiving that you can address to eliminate a chain reaction of inefficiencies across your warehouse. Specific relevant KPIs for receiving should include the cost of receiving per receiving line, the volume received per man-hour, receiving dock door utilization percentage, accurate receipts percentage, and the time taken to process a receipt. It is easy for warehouse managers to overlook receiving for picking and shipping KPIs. But, improperly designed and poorly run receiving areas have a damaging impact across the warehouse. If you have receiving inadequacies, your entire operation will feel the effects.
KPI for Picking and Packing Costs
Most warehouse managers point to order picking as one of their most expensive and difficult processes because it requires the most labour. Picking and packing processes often are more complex than other operations, and they are crucial to an organization’s bottom line because they are directly tied to customer satisfaction. KPIs for picking and packing should include cost per line item picked, orders picked per hour, picking labour costs, consumables usage, and cycle times per order. You can measure for accuracy and speed of picking and packing, and one specific metric to consider is your percentage of perfect pick lines.
The full content is only visible to SIPMM members
Already a member? Please Login to continue reading.
References
Ben Wee Pang Aik. (2018). “Effective Warehousing and Customer Service”. Retrieved from SIPMM: https://publication.sipmm.edu.sg/key-performance-metrics-effective-warehousing-customer-service/, accessed 12/09/2018.
Legacy Supply. (2015). “Top Warehouse Performance KPIs”. Retrieved from https://legacyscs.com/warehouse-kpis-to-measure/, accessed 12/09/2018.
Philip Charles Loges. (2018). “Key Performance Indicators for Evaluating Purchasing Performance”. Retrieved from SIPMM: https://publication.sipmm.edu.sg/key-performance-indicators-evaluating-purchasing-performance/, accessed 12/09/2018.
SDC Executive. (2008). “Mitigating Risk through Best Practices”. Retrieved from https://www.sdcexec.com/home/article/10289589/mitigating-risk-through-best-practices, accessed 12/09/2018.