Cold chain logistics refers to the maintaining precise temperature bands that store and transport pharmaceutical drugs and perishable food products. Due to its rigorous temperature requirements and energy dependence, it is perhaps one of the most complex and demanding logistics segments. The handling of highly sensitive drugs, which ultimately affects a human being, has made it necessary for the pharmaceutical industry to have a robust cold chain logistics system.
Fresh produce spoils easily. Worst of all, it often shows no signs of spoilage until it is too late, causing shipments to be refused at the very end of the fresh supply chain. This usually leaves the cost of the loss to the supplier, producer or grower.
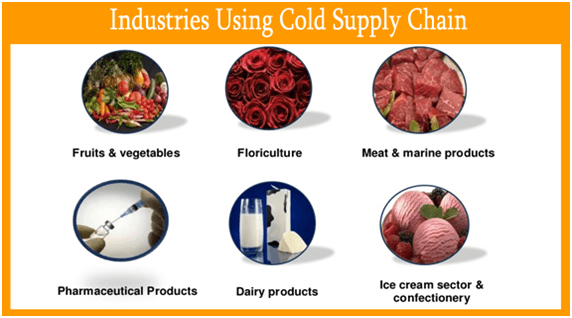
“Today, a typical item that enters Singapore, either from the port, the airport or the Causeway will probably have zipped around the island a few times before it finally reaches the hands of the final consumers”, quoted Trade and Industry Minister Chan Chun Sing, adding that it is a situation that is “highly inefficient, highly unproductive and a waste of time and money”. Trade and Industry Minister Chan Chun Sing further added that Singapore needs to test new concepts and consider it as a competitive advantage.
For Singapore to become a key player in the global supply chain, logistics firms here need to adopt new technologies and improve productivity. Singapore can thus also serve as a role model and test bed for many other countries, especially in Asia. Newer technologies presents companies with new opportunities and allow the companies to create new workforce and better jobs.
Table of Contents
The Right Technologies In Cold Chain
In order to promote agility and resilience, companies will continue to depend on solutions that connect partners and stakeholders across their ecosystems together. Cloud- powered technologies will support these investments and enhance both planning and implementation. This requires cold chain service providers to provide transparency and confidence in their customer service. The right planning tools will ensure effective response to emergencies such as supplier bankruptcy or natural disasters. Proper planning will ensure companies can adjust pricing and promote strategies to shape demand, move additional products quickly in storage or inventory and increasing revenue growth. Leveraging on cloud supply chain technologies, businesses now have the ability to see exactly where all of their inventory is.
Radio Frequency Identification (RFID)
A cold chain RFID system generally includes a sensor, a tag and a reader which communicates with each other via radio transmission. RFID tags can store an EPC for logistics management purposes and a limited number of temperature readings if equipped with the appropriate sensor and battery power.
RFID tags may be broken down into the following categories:
1. Passive RFID tags
These tags rely on the reader’s electricity. When a passive RFID tag encounters radio waves from the reader, the coiled antenna within the tag forms a magnetic field. The tag draws power from it and energizes the tag’s circuits. The tag sends the encoded information to the memory of the tag. Passive tags can be very small. Passive tags can, therefore, be inserted into sticks and other similarly flat presentations.
2. Active RFID
The reliability of active tags is typically higher than passive tags because active tags have the ability to perform a ” session” with a reader. Active tags also transmit at higher power levels than passive tags, making them more efficient in environments commonly found during the distribution of food products. Active tags can be placed in tightly packed shipping containers or trucks, or long distance transit containers.
3. Semi-passive tags:
These systems are battery powered. They use the passive RFID interface to access the device wirelessly without using the internal power source. Therefore, the battery size is smaller than the active tags.
The preferred RFID embodiments for monitoring the environment of food supply chains are semi- passive or active tags with sensors. Tags can collect a wide range of information, including temperature, moisture, shock / vibration, light, radiation and gas concentrations. The data collected by the tags is collected by a gateway or hub that often transmits the data to a server. The data collected on the server can then be saved and analysed so that alerts and events are instantly generated.
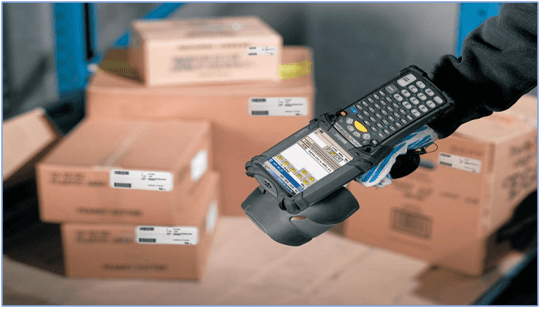
Internet of Things (IOT)
The Internet of Things (IoT) transforms the efficiency and effectiveness of food, pharmaceutical and other perishable supply chains. By implementing IoT solutions in the cold chain, companies can connect seamlessly to every step of the logistics process, offering a host of cost- effective benefits.
Companies can monitor and change temperature settings when deemed necessary, react to local climate change, products damage, unexpected delays and even human error. The level of insight provided by IoT technologies enables companies to act sooner on potential issues before they become major disasters.
IoT based solutions are being widely introduced in the industry with many advantages and opportunities. IoT technologies will continue to advance, and companies involved in the construction of a cold chain are already investing in sensor technology to make their businesses more competitive and deliver food and drugs to consumers as efficiently as possible.
Technology plays a major role in increasing the efficiency of an organization. There are number of ways you can automate the logistics process, including tracking and monitoring each delivery. Obtaining an ERP system that enables efficiency growth will help the supply chain in the short and long run by increasing revenue. Along with a planning system, locating software that is comprehensible within a team promotes overall coalition and will curtail mistakes in the future.
Mobile Racking
The analysis of storage and shelving is a step towards creating a more efficient cold storage facility, which is often overlooked, especially in refrigerated storage environments. Transitioning to a smarter storage solution can help identify waste areas, from poor product visibility to heavy congestion in aisles and help companies achieve many other storage goals at their refrigerated storage facility.

Mobile racking uses conventional selective pallet racks mounted on carriages and moving on running rails and guide rails embedded directly into concrete floor. A more efficient mobile storage system and inventory layout enables highly accessible and visible products that can speed up the time it takes for employees to place orders. Well organized storage can also reduce touches, reducing lead times significantly.
By implementing mobile racking, companies can save enough space to accommodate other value added services such as packing, labelling or high-pressure processing activities without having to renovate or add docks. Mobile racking is the storage solution with the highest density and maximizes the capacity of your high – cost cold storage to reduce waste energy. An organized warehouse leads to a safer, more enjoyable work environment that encourages employee engagement, especially in a challenging cold chain.
Conclusion
A robust cold chain includes appropriate packaging for the product, have best transport practices and visibility of temperature throughout the transit. We need to continuously improve the logistics and supply chains of Singapore and eliminate labour – intensive operations by means of automation and digitisation. This will reduce manpower costs and increase efficiency. By adding new digital technology to their cold chain to track, manage and improve their logistics in the supply chain, businesses can rest assured that clients will receive the right product in a timely and quality manner.
References
Bill Dykas. (2018).“How IoT-Enabled Monitoring is Changing Cold Chain Logistics Forever”. Retrieved from https://www.telit.com/blog/iot-enabled-monitoring-changing-cold-chain-logistics-forever, accessed 24/12/2018.
Brandon Tanoto. (2018). “Singapore logistics firms urged to automate, adopt new technology”. Retrieved from https://www.channelnewsasia.com/news/business/singapore-logistics-firms-urged-to-automate-adopt-new-technology-10541604, accessed 24/12/2018.
EDB Singapore. (2017). “Singapore, a hot bed for cold chain logistics”. Retrieved from https://www.edb.gov.sg/en/news-and-resources/insights/innovation/singapore–a-hotbed-for-cold-chain-logistics.html, accessed 24/12/2018.
McKenna. (2015). “Cold Storage – 5 Ways Mobile Racking Can Solve Your Cold Chain Challenges”. Retrieved from http://www.spacesaver.com/cold-storage-5-ways-mobile-racking-can-solve-your-cold-chain-challenges, accessed 24/12/2018.
Michelle Lee Ean Wei, DLSM. (2018).“Digital Technology for Cold Chain Distribution”. Retrieved from SIPMM: https://publication.sipmm.edu.sg/digital-technology-cold-chain-distribution/, accessed 24/12/2018.
Silvia Estrada-Flores. (2008). “RFID Technologies for Cold Chain Applications”. Retrieved from https://www.researchgate.net/publication/262010954_RFID_Technologies_for_Cold_Chain_Applications, accessed 24/12/2018.
Wong Kok Fu, DLSM. (2018).“Data Warehousing for Integrated Logistics”. Retrieved from SIPMM: https://publication.sipmm.edu.sg/data-warehousing-integrated-logistics, accessed 24/12/2018.