The success of a warehouse is reflected in the efficiency of its daily operations that promotes productivity among its workers. A well-organized warehouse layout is fundamental in achieving successful warehouse management as it directly impacts warehouse productivity. As a warehouse operation requires frequent interaction between people, machinery, and technologies, it is imperative that workflows are strictly adhered to. Hence, there is a need to conduct trainings to ensure awareness of the processes. Trainings should include the importance of adhering to safety and security. This article discusses the factors that are crucial to the successful operations of a warehouse.
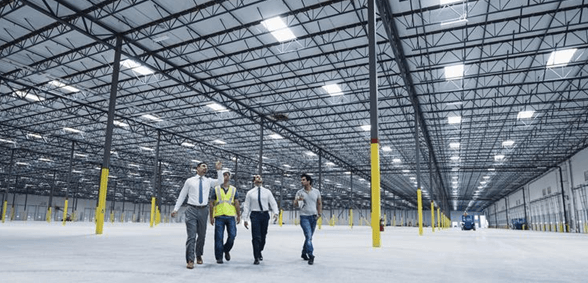
Table of Contents
Proper Warehouse Layout
A proper warehouse layout that is planned strategically to facilitate the smooth functioning of operations is crucial for successful warehouse management. It not only increases efficiency but productivity as well. A warehouse that has a poor layout design will have a great impact on operations. It can lead to increased travel times in the shifting, unloading and retrieval of goods. This will slow down the warehouse operations. Thereby decreasing the fulfilment rate and the overall productivity of the warehouse operations.
In order to plan a layout that promotes efficiency, the warehousing team would need to ensure that the necessary processes are in place. There should be logical sequences that not only streamlines operations but at the same time minimizes costs. The warehousing team should be able to access the goods they requires, easily within a short period of time.
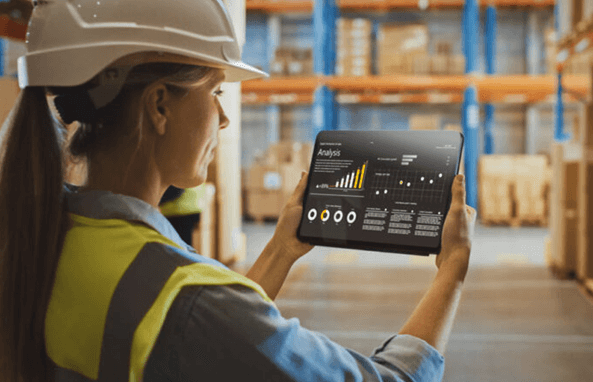
Efficient Warehouse Process
The absence of an efficient process can result in i.e. incorrect placement of goods by the warehouse personnel and shipments retrieved. It causes unnecessary wastes of time in looking for the correct location of the shipment and returning the wrong goods back to the correct location. There are six main warehouse processes i.e. receiving, putting away, storing, picking, packing, and shipping. By optimizing each process, the warehouse can achieve the fundamental warehouse processes through reduced costs, minimized errors, and increased fulfilment rates.
The receiving process is the most crucial. It is the first and foremost of warehouse procedure. Hence, it must be performed properly by ensuring that the goods received are in the proper quantity, good condition, and on time. Otherwise, this will affect the subsequent processes. “Put-away” needs to be done correctly as well. It not only can improve productivity but also the fulfilment rates by improving warehouse operations and goods traceability. When storing goods, the warehousing team will need to ensure that products are properly stored. The goods have to be placed at their respective locations to allow for easier identification. Improper storage rack design coupled with a poor warehouse management system will influence the success rate of a warehouse. A non-optimized picking and packing process can negatively impact the customer’s satisfaction. In shipping process, goods are well-packed into containers or lorries via a different mode of transportation and deliver goods to the customers safely on time, in good condition, and in the correct quantity.
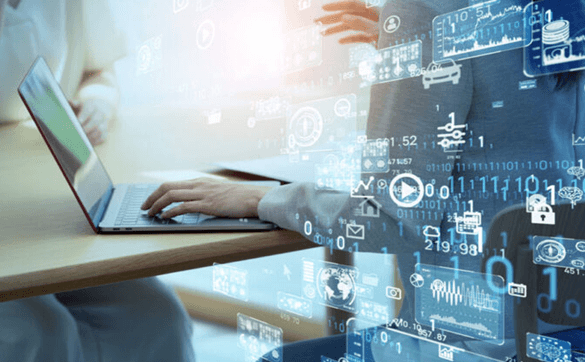
Technologies for Warehouse Productivity
Technologies are crucial for the management of a successful warehouse. Operations in a warehouse needs to be not only fast, accurate but must be efficient in deliveries to customers. WMS, for example, facilitates daily warehouse operations. This is done by providing accurate receiving counts, inventory records, inventory placement, as well as improving the efficiency of shipping processes. It is not only time-consuming to conduct manual stock counting and cargo searching but also high possibilities of human errors and involves more manpower. These mistakes will not only affect efficiency but having more manpower to accomplish a task will also impact productivity. There is a variety of WMS available such as Material Requirement Planning (MRP), System Application and Products (SAP), Oracle, Enterprise Resource Planning (ERP). A company should identify and select the most suited system for its operations.
When checking inventory received and picking items for orders, the warehouse personnel can also utilize scanners instead of manual search, to speed up the process. Among the WMS systems, ERP systems can facilitate successful warehouse management when used with mobile scanners and RFID technology. Automating warehouse operations is another crucial factor. Organizations will be able to achieve productivity and successful warehouse operations by investing in Artificial Intelligence (AI) robotics and automation.
Optimal Inventory System
Control of inventory system is required to determine inventory levels. Where customers’ demands are met without having to incur additional storage space while reducing inventory that does not sell. It is important to have a balanced forecast and decide with the supplier on the quantities and types of goods to be sent to the warehouse. Managers need to forecast accurately when to order goods from suppliers and arrange for delivery to the warehouse. If this is not put into practice, overstocking of goods will happen thus warehouse will be congested. To ensure optimization of operations, it is important not to over-order goods. At the same time to assess and remove those goods that are not selling, from the warehouse. Employees can do so by organizing a discounts sale to clear stocks. By doing so, they can reduce slow-moving inventory, and plan for better movement of goods.
The full content is only visible to SIPMM members
Already a member? Please Login to continue reading.
References
Amran Hossain, DLSM. (2019). “Key Considerations for Warehouse Safety and Health”. Retrieved from SIPMM: https://publication.sipmm.edu.sg/key-considerations-warehouse-safety-health/ , accessed 21/03/2022.
Analyn Enderes Trinidad, DLSM. (2021). “Crucial Factors for Implementing Warehouse Management”. Retrieved from SIPMM: https://publication.sipmm.edu.sg/crucial-factors-implementing-warehouse-management-system/ , accessed 21/03/2022.
Hector Sunol. (2021).“6 primary warehouse processes and How to Optimize Them”. Retrieved from https://articles.cyzerg.com/warehouse-processes-how-to-optimize-them# , accessed 21/03/2022.
Kaviyamuthan s/o Madasamy, DLSM. (2021).” Essential Practices for Warehouse Safety”. Retrieved from SIPMM:https://publication.sipmm.edu.sg/essential-practices-warehouse-safety/ , accessed 21/03/2022.
Prologis. (2022). “Warehouse Storage Security Management”. Retrieved from https://www.prologis.com/what-we-do/resources/guide-to-warehouse-storage-security-management#:~:text=Best%20Practices%20for%20Warehouse, accessed 21/03/2022.
WiSys. (2021). “7 Tips for Effectively Managing Your Warehouse”. Retrieved from https://www.wisys.com/effective-warehouse-management-7-tips-for-effectively-managing-your-warehouse/ , accessed 21/03/2022.
Wong Zhi Wei, DLSM. (2019). “Key Consideration for Warehouse Design and Layout”. Retrieved from SIPMM: https://publication.sipmm.edu.sg/key-considerations-warehouse-design-layout/, accessed 21/03/2022.