Logistics performance is a key role player of the business in the several industries. Imaging without logistics even in a city, at least there would be no food supply, empty mailboxes, full of trash cans, no delivery for favorite fur, no pharmacies for essential treatments, nor any reject collection, everything is going to be halted without its performance.
As the global logistics industry has significantly grown in recent years, the efficiency of logistics implies to sources of employment and competitiveness among the countries. That being so, the performance evaluation in logistics management is essential for our business, as well as for the daily life and survival, it has just now been proven amid of coronavirus outbreak.
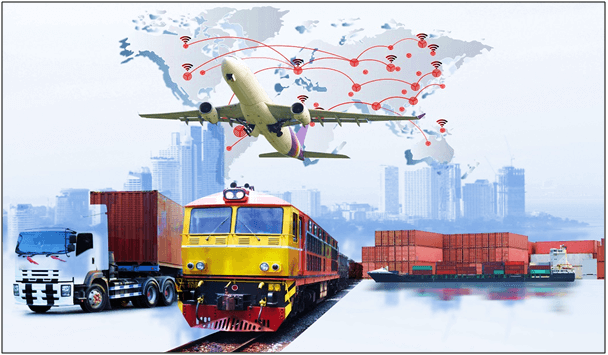
Table of Contents
Transportation
Transportation is a main component of the logistics chain, which connect the sources and end users for the flow of goods, energy, information, services, products, people and so on. The flow of transporting goods can be divided into inbound logistics, internal logistics and outbound logistics. Inbound logistics is the flow of raw materials shipped to a warehouse or a factory for manufacture purpose. Internal logistics is the movement of raw materials or finished goods inside the warehouse or factory from one department to another, and outbound logistics is the ship out of the finished goods to the end customers. To achieve the efficient transportation performance, the transportation cost, time, weight, volume of the shipment, security of goods and mode of transportation are required to consider as mutually related each other.
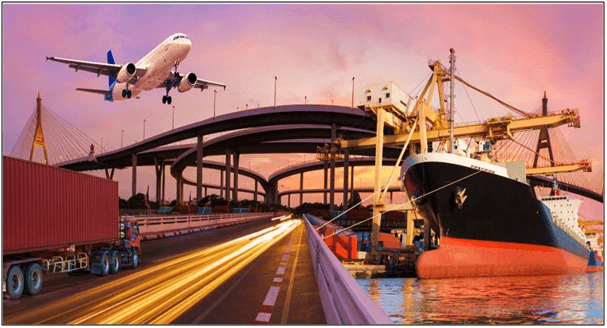
Overall transportation costs are the crucial part of the transportation system and one of the decision makers of business succession. It depends on variation in transportation modes, distance of source to destiny, and transport time managing. To be cost effective, the transportation modes, such as water, air, truck, rail, or pipeline, which shall be selectable is decided as per type of products. Example, small quantity or urgent perishable goods shall be selected to air freight mode for high speed and security despite the high cost. Heavy and large volume goods shall be selected the sea freight mode for volumetric transport at low cost. For all modes of freights, insurances play a vital role to prevent from loss of properties in the event of the failures. Overall transport time is implementing with the time required of goods production, loading, unloading, picking, packing, and transiting, etc. The transit time is the time from warehouse to end customer until completely delivered and this time needs to be managed for reaching the products to customer on agreed time with smooth operation.
Warehousing
Warehousing is the storing of goods at the designated space for onward distribution to the customers. Warehouse action is not only storing of goods, but also acting like a consolidation center, whereas products are combined from several suppliers and delivered to a final consumer or a break bulk warehouse, whereas break out the orders from the same manufacture and deliver to many individual consumers. Moreover, warehouse allows larger consignments for shipping, store for a future date, maintain the longer lead times source of supply, reducing customer lead time as no need to wait of production. If needed, apply postponement strategy for customer satisfaction and support JIT (Just in Time) programs. Warehousing Costs are covering all the equipment and energy costs, inventory cost, store cost and goods loading cost in the warehouse. These costs are related to the warehouse performance factors, such as receiving, inventory accuracy, put-away, cross-docking, picking, packing, responsiveness, and warehouse productivity planning.
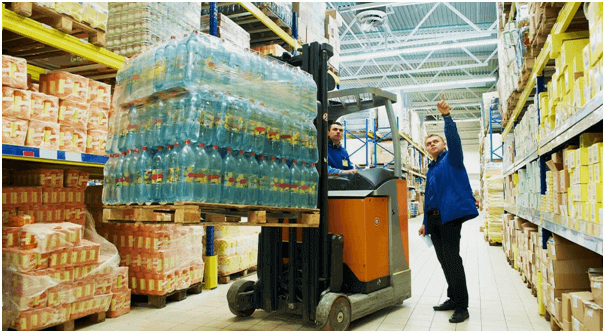
Firstly, receiving is unloading goods from a vehicle, handling products into a warehouse and onto a system. If we need the more times to handle for an item to put into a warehouse or system, the more money will be wasting. In this part, make sure the receive inventory items are accurate with the booking in the system and these are not damaged. If damaged, decision making required to return the item or ask the discount from the manufacturer in this situation. Secondly, the transfer of the receive products to the storage area is Put-Away task.
The warehouse operators scanning the relevant barcodes of goods to be put away and accessing the Enterprise Resource Program (ERP) or Warehouse Management System (WMS). If there is no barcode scanner, manual entry can be confirmed that the goods have been identified. If the cross-docking warehouse is used, it is effective for reducing the storage costs. In cross-docking, instead of the stock being put into the storage, sent across the loading dock directly load onto another vehicle to deliver. Thirdly is picking and packing, they can also be the player of failure warehouse quickly, if the picking or packing method is incorrect.
Picking methods can be first with goods, second in a process and picking by real-time or waves. To accurate at picking, choose the one of the picking methods where using voice systems and no scanning will be used. But Pick-to-voice systems need to scan at all and check the digits of the location serve to ensure the operator is at the correct location. Packing performance can be accurately by packed the item according to their size, value, quantity, hygienic, temperature, fragility, toxicity, and legislative requirements. Packed goods must be traceable too. Besides, warehouse responsiveness also shall be considered to describe how fast the requested service will be completed. For warehouse functioning smoothly, Material Handling Equipment (MHE) types have been chosen as per product types and warehouse space, such as carton clamps, drum clamps, paper roll clamps, rotators, or push-pull elements, etc.
The full content is only visible to SIPMM members
Already a member? Please Login to continue reading.
References
Balaguru Patmanathan, DLSM. (2018). “The Five Essential Techniques for Effective Warehousing”. Retrieved from SIPMM: https://publication.sipmm.edu.sg/the-five-essential-techniques-for-effective-warehousing/, accessed 26/08/2018.
Jean Beh Lee Chin, DLSM. (2020). “Key Transport Considerations for Integrated Logistics”. Retrieved from SIPMM: https://publication.sipmm.edu.sg/key-transport-considerations-integrated-logistics/, accessed 03/03/2020.
Kayla Matthews, (2019). “How Warehouse Robotics Reduce Worker Injuries”. Retrieved from https://www.ehstoday.com/safety-technology/article/21920298/how-warehouse-robotics-reduce-worker-injuries, accessed 15/08/2019.
Theresa Pang Kim Lian, DLSM. (2019). “Key Considerations for Reverse Logistics Operations”. Retrieved from SIPMM: https://publication.sipmm.edu.sg/key-considerations-reverse-logistics-operations/, accessed 19/10/2019.
Way Tian Chai, DPSM. (2019). “Key Stages for Purchasing Heavy Equipment Parts”. Retrieved from SIPMM: https://publication.sipmm.edu.sg/key-stages-purchasing-heavy-equipment-parts/, accessed 06/04/2019.