When it comes to warehouse safety there are many benefits that are often overlooked. Safety procedures are frequently disregarded in a variety of workplaces due to insufficient time, inadequate resources or an opportunity to cut corners in an attempt to save money. However, when safety procedures are soundly implemented there are major benefits such as higher employee satisfaction as well as increased productivity.
By minimizing the risk of injury, fewer workplace disruptions take place and absenteeism associated with injury is also reduced. Equipment downtime is another factor which can be avoided through the appropriate use of safety procedures.
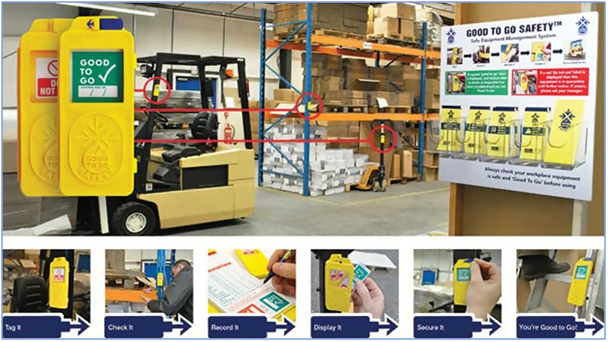
Table of Contents
Key Safety Guidelines for Warehouse Safety
1. Ensure Safety Equipment is Used at all Times
In the warehouse, it is vital that forklifts or hydraulic dollies are used to lift items that are too heavy. Appropriate eyewear and hard hats should also be worn when required. Employees should be aware of emergency exits and the sprinklers installed in the roof should not be blocked at any time. Safety equipment is implemented in order to minimize workplace injury, so although it may be time-consuming to initiate its use, it does pay off in the long run.
2. Eliminate Any Potential Safety Hazards
Ensure all warehousing floors are free of ‘slip and trip’ hazards. It is important that this safety check is carried out on a regular basis, by all employees, and that the floor is always free of stray cords, liquids and any other potentially hazardous items. It is also essential that any cracks and pits in the flooring are attended to as these can cause serious injuries to employers as well as damaging expensive machinery.
3. Clearly Label Designated Hazardous Zones
Dangerous equipment should be stored away in an area that is clearly labeled and safe walkways should be highlighted through necessary signage. The easiest way to illuminate hazardous zones is by using tape or painting black and white stripes on the floor of the designated area. This enables employees to be aware of dangerous surroundings and can be useful in avoiding accidents that can cause serious injury.
4. Always Use Safe Lifting Techniques
When a load requires transporting, firstly assess what method is the best option for its movement. If lifting is the most suitable method; check the route to ensure no obstacles are in the way and ensure there is enough space for the load at its destination. Safe lifting techniques should always be carried out and the load should not obstruct the view of the lifter. Use all materials handling equipment carefully and follow the proper operating procedures including push rather than pull, whenever possible and lean in the direction that is being traveled. Also, never drive a forklift or use other powered equipment without training or authorization.
5. Provide Training and Refresher Courses
Ensure all staff is educated and up to date with knowledge about safe practices within the workplace. This allows for greater adherence to procedures as staff members will be completely aware of the consequences that can emanate from an unsafe workplace. Accidents most commonly occur when corners are cut in an attempt to save time. If staff and management are completely aware of the repercussions that can arise from this fact, procedures may be followed more closely.
6. Promote Awareness in your Warehouse
Having a sense of awareness in the workplace is an important safety factor. This can be achieved through communication between staff members. By employees being vocal and yelling out to others their location, collision incidents can be drastically reduced. When carrying items or driving machinery, a simple “coming through” can alert other co-workers of their whereabouts and can allow them to steer clear of dangerous pathways.
Top World Health and Safety Hazards
The following are listed as top health and safety hazards found in most warehouses around the world.
1. Falls from a Height
There are various regulations in place to protect those working at great heights which include the Work at Height Regulations 2005. By the very nature and structure of warehouses, employees will be asked on a regular basis to store and remove various products at great heights. It is fair to say that safety issues have been improved in recent years with the use of cherry pickers and other elevation machinery reducing the chances of employees falling from a great height. However, not all warehouse facilities are as safe as they should be and there have been instances of employees falling from a great height due to a lack of training, substandard machinery or other employee-related issues for which a warehouse accident claim could be started.
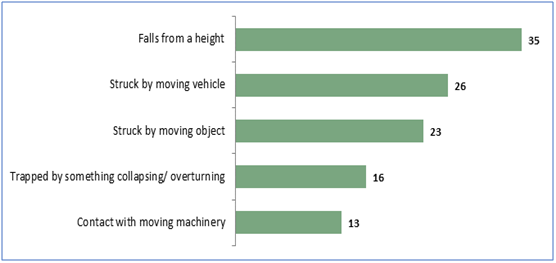
2. Fire Hazard and Risks in Warehouses
According to a study by the German Insurance Association, more than one-third of all industrial and commercial fires occur in warehouses. As such, fire prevention takes on special importance within the storage and logistics sector and needs to play an important role in logistics centers and warehouses right from the planning stages. Most warehouse fires are caused by sparks emitted by overloaded electronic components, such as drive motors or high-back racking units.
The full content is only visible to SIPMM members
Already a member? Please Login to continue reading.
References
Adaptalift Group. (2019). “Warehouse Safety Principles”.Retrieved from https://www.aalhysterforklifts.com.au/index.php/about/blog/,accessed 18/03/2019.
Claims Action. (2018). “Warehouse Accident Claims”. Retrieved from https://www.claimsaction.co.uk/accident-at-work-claim/warehouse-accident-claims, accessed 18/03/2019.
David Chew, DLSM. (2019).“Four Key Areas For Mitigating Warehouse Risks”.Retrieved from SIPMM: https://publication.sipmm.edu.sg/four-key-areas-mitigating-warehouse-risks, accessed 18/03/2019.
Jeff Tan Ai Keong, DLSM. (2018). “Key Performance Indicators Minimising Warehouse Risks”. Retrieved from SIPMM: https://publication.sipmm.edu.sg/key-performance-indicators-minimising-warehouse-risks, accessed 18/03/2019.
Health And Safety Authority. (2019). “Vehicle Overturns”.Retrieved from – https://www.hsa.ie/eng/Vehicles_at_Work/Work_Related_Vehicle_Safety/Vehicle_Risks/Vehicle_Overturns, accessed 18/03/2019.
SIPMM LPS 304 Module Guide. (2019). “Workplace Safety and Health Act- roles and responsibilities”. Retrieved from SIPMM LPS304 Warehouse Management Topic 5, accessed 18/03/2019.