Warehouse productivity is a number of measurements that management will analyze to monitor the performance of their warehouse operations. The basis of many of the measures used in warehouse productivity is based on how much it costs to perform an operation.
Table of Contents
Improving Warehouse Layout Design
A well-design layout will allow you to exploit every square foot of space. It is the most effective method to increase efficiency and accessibility and when adhered to properly, it can make a substantial difference to your operations.
o Segmentation
Day-to-day warehouse activity is fast paced and dynamic, and as a result, chaos can quickly ensue. By segmenting your physical layout into clearly defined areas, processes become more efficient. It’s recommended to have separate areas for operations such as goods-in, inventory, packing, shipping and returns – designating specific space for special activities.
o Shorten Aisles
A large warehouse with endless rows of racking might look impressive, but in actual fact, your layout efficiency will be extremely poor. If it takes a long time to get from one area of your warehouse to another, or if the transportation of products across you warehouse is time consuming, then it’s time to make a change. By creating cross aisles, or shortening your main aisles you’ll cut pick path routes in half. You’ll also increase the speed of product retrieval, making operatives more productive and picking times much shorter.
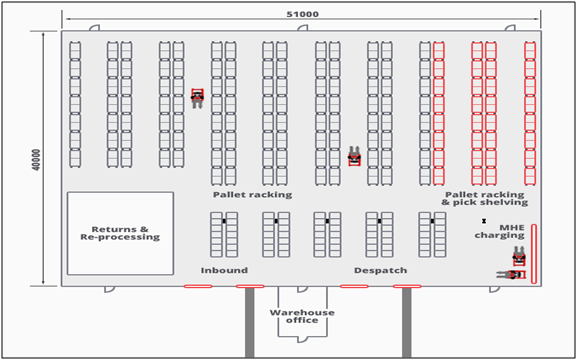
Warehouse Stock Organization
Setting up a warehouse in an efficient and organized manner is beneficial for a number of reasons. Not only does it assist in inventory control and time management, but it also streamlines the entire process of doing business, from ordering and storing, to pulling and shipping.
Use ABC Analysis to Set Up Warehouse Inventory
ABC analysis of inventory is a method of sorting your inventory into 3 categories according to how well they sell and how much they cost to hold:
A-Items – Best-selling items that don’t take up all your warehouse space or cost.
B-Items – Mid-range items that sell regularly but may cost more than A-items to hold.
C-Items – The rest of your inventory that makes up the bulk of your inventory costs while contributing the least to your bottom line.
ABC analysis of inventory is one way of applying Pareto’s 80/20 principle. The bulk of your profits will usually come from about 20% of your total inventory. After grouping your inventory into ABC categories, arrange your pick and pack area in a way that gives your employees the easiest access to A SKUs, then B SKUs, and finally C SKUs.
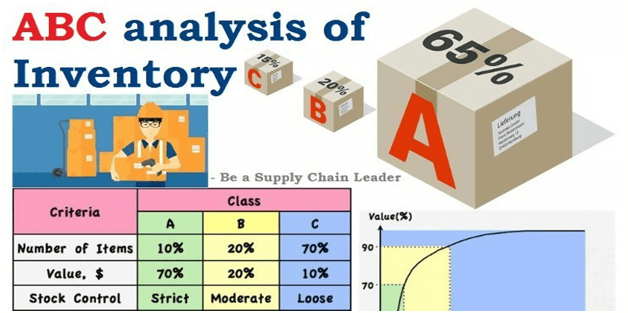
Keep Your Warehouse Clean
There are many benefits Implementing 5S in the Warehouse, as follows:
o Make the Warehouse clean and neat
o Improve Warehouse productivity
o Improve the Quality of Works
o Save Warehouse Operation Cost
o Improve Delivery Performance
o Improve Safety aspects
o Eliminate waste
o Improve Warehouse staffs’ morale
Make Receiving Inventory Easy
Receiving inventory effectively is one of the key warehouse management tips because it sets the tone for the rest of your warehouse and inventory processes. Some benefits include the following
o Optimize your receiving space
o Keep your receiving space clean and organized
o Track inventory in real-time
o Monitor quality control
o Unload received inventory quickly and safely
o Avoid shipping the wrong items to your customers
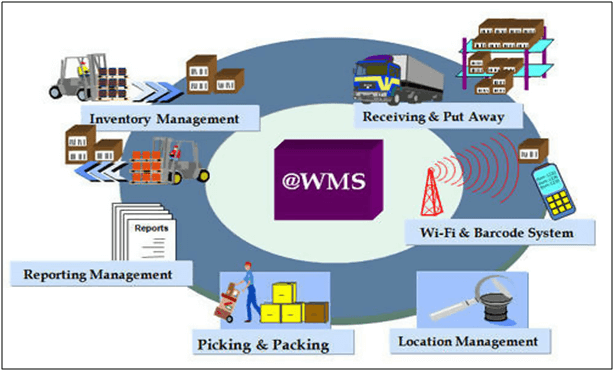
Adopt a cycle counting system
Where inventory is routinely counted one or more times in a given cycle. The cycle can be each month, each quarter, or any other time period you choose. This helps keep inventory numbers far more accurate as well as helps identify missing stock and put-away errors.
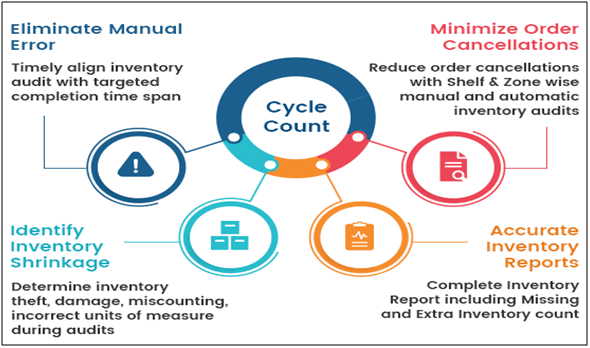
Improve Order Picking Accuracy and Productivity
The order picking process involves pulling items from inventory to fill a customer`s order. This is often seen as the most labor-intensive task within a warehouse. Forming as much as 55 percent of operation costs within a warehouse. Order picking has a direct impact on customer`s satisfaction level, so making it quick and accurate is vital.
Minimize Touches
Ideally, when an order is picked and packed, it should only need to be touched once throughout the process. To accomplish this, the order must be error-free and packed correctly the first time, moving directly from shelf to box to truck without having to be moved in and out of totes or repacked into smaller or larger containers. Minimizing this kind of rework helps make the picking and packing process more efficient.
The full content is only visible to SIPMM members
Already a member? Please Login to continue reading.
References:
Aavon Roderick. (2018). “7 Warehouse Organization Tips That Will Increase Your Productivity Today”. Retrieved from https://dearsystems.com/warehouse-organization-tips/ accessed 11/09/2019.
Prakaash Gunasengaran, DLM. (2017). “Technique to Improve the Warehouse Order Picking Process”. Retrieved from SIPMM: https://publication.sipmm.edu.sg/techniques-to-improve-the-warehouse-order-picking-process/, accessed 08/09/2019.
Rachael Hutchman. (2018). “7 Ways to Improve Your Warehouse Layout”.
Retrieved from: https://expertmanufacturer.com/improve-warehouse-layout/,accessed 08/09/2019.
Reid Curly. (2016). “8 Tips for Maintaining Warehouse Stock Organization”.
Retrieved from: https://info.archon-interactive.com/blog/9-tips-for-maintaining-warehouse-stock-organization , accessed 08/09/2019.
Sam Leong Kim Foong, DLSM. (2019). “Key Performance Indicators (KPIs) for the Logistics Sector”. Retrieved from SIPMM: https://publication.sipmm.edu.sg/key-performance-indicators-kpis-logistics-sector, accessed 08/09/2019.